Calculation-experimental procedure for determining welding deformations and stresses based on a digital image correlation method
DOI:
https://doi.org/10.15587/1729-4061.2022.265767Keywords:
stressed-strained state, non-destructive testing, digital correlation of images (DIC), laser weldingAbstract
The object of this study is determining the stressed-strained state (SSS) of a welded article by applying quantitative non-destructive testing. The relevance of the study is associated with the need to devise a universal methodology for the non-destructive quantification of SSS using the simplest approaches and means of provision. To solve this task, an estimation-experimental procedure has been developed. This procedure is based on comparing digital stereo images of the individual sections (spatial primitives) of an article before and after its welding, followed by computer processing. To validate the developed procedure, the SSS of a cylindrical article made of aluminum alloy 7005, at the end of which two flanges were welded laserly with ring seams, was determined. It was established that after performing four diametrically opposed point tacks, the residual deformations of the ends of the article can reach 0.02–0.05 mm, and after performing continuous ring seams – to decrease to 0.01–0.02 mm. The calculation showed that the residual deformations of the end of the article after welding a ring seam are at the level of 0.02 mm, and the residual stresses in the same zone – in the range of 50–60 MPa. The deviation in the coincidence of residual deformations is in the range of 10–20 %, which is a satisfactory result and can be considered as an error in the results of determining SSS in general. Based on the developed methodology for determining SSS, an experimental industrial complex has been created that allows TIG and PAW to perform welding of objects from steels and alloys with the ability to determine the resulting stressed-strained state of these objects. The procedure devised and the equipment designed can be used for to non-destructively determine SSS of spatial structures made of steels and alloys
References
- Khaskin, V. Yu., Korzhik, V. N., Sydorets, V. N., Bushma, A. I., Boyi, W., Ziyi, L. (2015). Improving the efficiency of hybrid welding of aluminum alloys. The Paton Welding Journal, 2015 (12), 14–18. doi: https://doi.org/10.15407/tpwj2015.12.03
- Korzhik, V. N., Pashchin, N. A., Mikhoduj, O. L., Grinyuk, A. A., Babich, A. A., Khaskin, V. Yu. (2017). Comparative evaluation of methods of arc and hybrid plasma-arc welding of aluminum alloy 1561 using consumable electrode. The Paton Welding Journal, 2017 (4), 30–34. doi: https://doi.org/10.15407/tpwj2017.04.06
- Huang, X., Liu, Z., Xie, H. (2013). Recent progress in residual stress measurement techniques. Acta Mechanica Solida Sinica, 26 (6), 570–583. doi: https://doi.org/10.1016/s0894-9166(14)60002-1
- Rendler, N. J., Vigness, I. (1966). Hole-drilling strain-gage method of measuring residual stresses. Experimental Mechanics, 6 (12), 577–586. doi: https://doi.org/10.1007/bf02326825
- Lobanov, L. M., Asnis, E. A., Piskun, N. V., Vrzhizhevsky, E. L., Milenin, A. S., Velikoivanenko, E. A. (2019). Investigation of stress-strain state of welded joints of the system TiAl intermetallics. The Paton Welding Journal, 2019 (11), 8–11. doi: https://doi.org/10.15407/tpwj2019.11.02
- Viotti, M. R., Kapp, W., Albertazzi G., Jr., A. (2009). Achromatic digital speckle pattern interferometer with constant radial in-plane sensitivity by using a diffractive optical element. Applied Optics, 48 (12), 2275. doi: https://doi.org/10.1364/ao.48.002275
- Steinzig, M., Ponslet, E. (2003). Residual stress measurement using the hole drilling method and laser speckle interferometry: part 1. Experimental Techniques, 27 (3), 43–46. doi: https://doi.org/10.1111/j.1747-1567.2003.tb00114.x
- Lobanov, L. M., Pivtorak, V. A., Kyjanets, I. V., Savitsky, V. V., Tkachuk, G. I. (2005). Express control of quality and stressed state of welded structures using method of electron shearography and speckle-interferometry. The Paton Welding Journal, 8, 35–40.
- Lord, J. D., Penn, D., Whitehead, P. (2008). The Application of Digital Image Correlation for Measuring Residual Stress by Incremental Hole Drilling. Applied Mechanics and Materials, 13–14, 65–73. doi: https://doi.org/10.4028/www.scientific.net/amm.13-14.65
- Dannemann, K. A., Bigger, R. P., Scott, N. L., Weiss, C. E., Carpenter, A. J. (2016). Application of Digital Image Correlation for Comparison of Deformation Response in Fusion and Friction Stir Welds. Journal of Dynamic Behavior of Materials, 2 (3), 347–364. doi: https://doi.org/10.1007/s40870-016-0070-6
- Lyubutin, P. S., Panin, S. V., Titkov, V. V., Eremin, A. V., Sunder, R. (2019). Development of the digital image correlation method to study deformation and fracture processes of structural materials. PNRPU Mechanics Bulletin, 1, 88–109. doi: https://doi.org/10.15593/perm.mech/2019.1.08
- Sutton, M. A., McNeill, S. R., Helm, J. D., Chao, Y. J. (2000). Advances in Two-Dimensional and Three-Dimensional Computer Vision. Photomechanics, 323–372. doi: https://doi.org/10.1007/3-540-48800-6_10
- Hild, F., Roux, S. (2006). Digital Image Correlation: from Displacement Measurement to Identification of Elastic Properties - a Review. Strain, 42 (2), 69–80. doi: https://doi.org/10.1111/j.1475-1305.2006.00258.x
- Pan, B., Asundi, A., Xie, H., Gao, J. (2009). Digital image correlation using iterative least squares and pointwise least squares for displacement field and strain field measurements. Optics and Lasers in Engineering, 47 (7-8), 865–874. doi: https://doi.org/10.1016/j.optlaseng.2008.10.014
- Jandejsek, I., Vavřík, D. (2016). Experimental Measurement of Elastic-Plastic Fracture Parameters Using Digital Image Correlation Method. Applied Mechanics and Materials, 821, 442–449. doi: https://doi.org/10.4028/www.scientific.net/amm.821.442
- Jandejsek, I., Gajdoš, L., Šperl, M., Vavřík, D. (2017). Analysis of standard fracture toughness test based on digital image correlation data. Engineering Fracture Mechanics, 182, 607–620. doi: https://doi.org/10.1016/j.engfracmech.2017.05.045
- Diachenko, S. S. (2003). Fizychni osnovy mitsnosti ta plastychnosti metaliv. Kharkiv: Vydavnytstvo KhNADU, 226.
- Vincent, Y., Bergheau, J.-M., Leblond, J.-B. (2003). Viscoplastic behaviour of steels during phase transformations. Comptes Rendus Mécanique, 331 (9), 587–594. doi: https://doi.org/10.1016/s1631-0721(03)00147-5
- Vora, J., Patel, V. K., Srinivasan, S., Chaudhari, R., Pimenov, D. Y., Giasin, K., Sharma, S. (2021). Optimization of Activated Tungsten Inert Gas Welding Process Parameters Using Heat Transfer Search Algorithm: With Experimental Validation Using Case Studies. Metals, 11 (6), 981. doi: https://doi.org/10.3390/met11060981
- Liu, Z. M., Cui, S., Luo, Z., Zhang, C., Wang, Z., Zhang, Y. (2016). Plasma arc welding: Process variants and its recent developments of sensing, controlling and modeling. Journal of Manufacturing Processes, 23, 315–327. doi: https://doi.org/10.1016/j.jmapro.2016.04.004
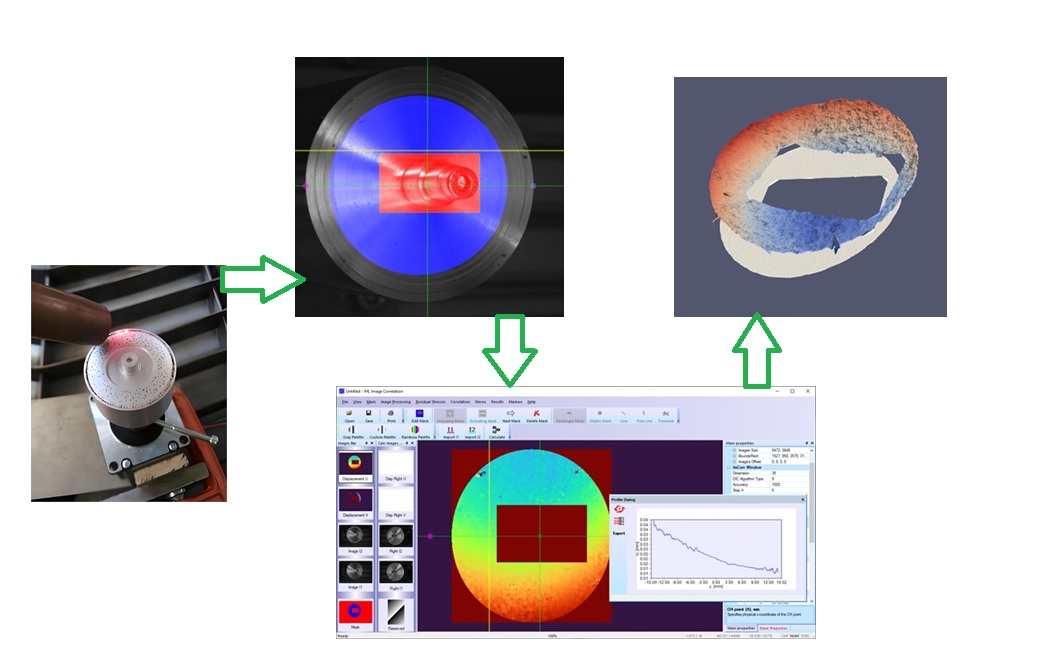
Downloads
Published
How to Cite
Issue
Section
License
Copyright (c) 2022 Volodymyr Korzhyk, Vladyslav Khaskin, Viktor Savitsky, Illia Klochkov, Viktor Kvasnytskyi, Andrii Perepichay, Sviatoslav Peleshenko, Andriy Grinyuk, Andrii Aloshyn, Oleksii Shutkevych

This work is licensed under a Creative Commons Attribution 4.0 International License.
The consolidation and conditions for the transfer of copyright (identification of authorship) is carried out in the License Agreement. In particular, the authors reserve the right to the authorship of their manuscript and transfer the first publication of this work to the journal under the terms of the Creative Commons CC BY license. At the same time, they have the right to conclude on their own additional agreements concerning the non-exclusive distribution of the work in the form in which it was published by this journal, but provided that the link to the first publication of the article in this journal is preserved.
A license agreement is a document in which the author warrants that he/she owns all copyright for the work (manuscript, article, etc.).
The authors, signing the License Agreement with TECHNOLOGY CENTER PC, have all rights to the further use of their work, provided that they link to our edition in which the work was published.
According to the terms of the License Agreement, the Publisher TECHNOLOGY CENTER PC does not take away your copyrights and receives permission from the authors to use and dissemination of the publication through the world's scientific resources (own electronic resources, scientometric databases, repositories, libraries, etc.).
In the absence of a signed License Agreement or in the absence of this agreement of identifiers allowing to identify the identity of the author, the editors have no right to work with the manuscript.
It is important to remember that there is another type of agreement between authors and publishers – when copyright is transferred from the authors to the publisher. In this case, the authors lose ownership of their work and may not use it in any way.