1. 引言
随着全球环境意识的增强和对气候变化的关注,电动汽车作为一种清洁、低碳的交通工具,正逐渐成为汽车行业的主流趋势 [1] 。电动汽车的电池组在工作过程中会产生大量的热量,如果不能有效地管理和控制这些热量,将会严重影响电池的性能、寿命和安全性 [2] [3] 。
传统的电动汽车电池热管理系统通常采用液冷方式,即通过循环泵将冷却剂引入电池组,通过冷却剂吸收电池产生的热量,并将热量带走 [4] 。然而,由于冷却液自身物理属性导致其传热速率较低。其次,冷却液需要首先经过板式换热器(chiller)换热来降低或升高温度,然后再通过水冷板与电池交换热量,导致其换热热阻大,导热路径长,不可避免地导致系统的能量耗散,换热效率降低。液冷方式布置管道多,结构复杂,给电池的可靠性和维护带来了一定的挑战 [5] [6] 。
直冷式热管理系统通过直接将冷媒引入电池组直冷板进行冷却,从而简化了热管理系统结构 [7] 。低温冷媒直接与电池包通过铝制冷板传热,大大提高了换热速率,降低了换热内阻,提高了电动汽车的能量利用率 [8] 。
韩国大学Seong Ho Hong等人基于实车工况下的全尺寸实验,将两相制冷剂冷却的热性能与相同外形尺寸的传统液体冷却进行了比较,与液冷系统相比,直冷系统多出16.1%的电池容量,降低了15.0%的内阻 [9] 。上海交通大学聂磊等人采用蜂窝型单面吹胀铝板作为电池冷板,在6 kW的发热量下,电池冷板表面平均温度可控制在15℃~20℃区间,温差小于4℃,且系统COP稳定在2.8以上 [10] ;中国科学院广州能源研究所林必超等人设计一种18,650型电池模组,基于PID算法控制电子膨胀阀,研究R134a制冷剂直接气液两相流冷却电池模组的换热性能。结果表明电池模组以1 C倍率放电,电池最大温差小于4℃,并且最高温度低于36℃。
本文旨在研究和探讨电动汽车电池包直冷板的三维建模与仿真,通过实验数据,对标直冷板仿真模型,验证了该仿真方案的可行性与精度。
2. 几何模型
2.1. 三维模型
根据冷板实际参数,使用CAD软件建立1:1直冷板模型。如图1所示。冷板长宽高分别为L * W * H。材料为铝。
流道分布如图2所示。冷板具有一个入口与一个出口,入口与出口截面均为矩形。流道在入口处附近一分为二,分别延伸出位于冷板左右的两大块区域。冷板流道具有很多分支,流体在冷板内被分流再合并至出口端。
2.2. 网格划分
对直冷板进行网格划分,最终体网格数量大约位6,000,000。网格无关性检验如图3所示,当网格数量增加到很大时,网格数量的增加并没有显著提高模型的计算精度。此模型网格最小正交质量(minimum orthogonal quality)为0.16。网格质量较好。为仿真计算工作打下良好基础。具体网格划分见图3和图4。
冷板仿真参数如表1所示。冷板内部流体属性为:液相属性:密度1147.4 k/m3,比热容1490 J/(kg·K),热导率0.075 w/(m·K),粘度0.000162 kg/(m·s),分子量102 kg/kmol。气相属性:密度设为理气体,比热容1140 J/(kg·K),热导率0.0154 w/(m·K),粘度1.2e−5 kg/(m·s),分子量102 kg/kmol。
3. 两相流模型
3.1. 传质理论
Ansys Fluent使用两种模型之一通过蒸发冷凝进行相间传质。对于VOF和混合物配方,使用Lee模型。Lee模型是一种具有物理基础的机械模型。它与mixture或VOF多相模型一起使用。
在Lee模型中,液–气传质(蒸发和冷凝)由蒸汽传递方程控制:
(1)
其中,v为气相;αv为蒸汽体积分数;ρv为蒸汽密度;
为气相速度;
为分别由蒸发和冷凝引起的传质速率。
Fluent定义液相向气相传质为正:
当液相温度大于饱和温度(蒸发)时,有:
(2)
当气相温小大于饱和温度(冷凝)时,有:
(3)
Coeff是必须微调的系数,可以解释为弛豫时间。必须对系数进行微调以匹配实验数据。默认情况下,蒸发和冷凝的系数均为0.1。但是,在实践中,数量级可以高达103。蒸发只有液相向气相传质,冷凝只有气相向液相传质。能量源项等于质量源项乘以潜热。与UDF Lee模型定义相同。式中的coeff (单位1/s)。
3.2. 不同传质系数对比
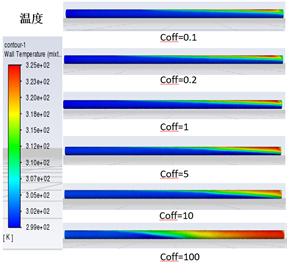
Figure 5. Fine tube surface temperature and internal gas phase rate
图5. 细管表面温度与内部气相率
传质系数对模型仿真的准确性存在明显的影响,受到计算资源的限制,先使用用小管模型观察传质系数对冷板进出口前后气相率以及温度分布。建立直径为10 mm,长度为100 mm的直管。进口为全液相,出口为压力出口,压力为587 kpa,壁面热通量为1880 w/m2。分别设置传质系数(coff)为,0.1,0.2,1.0,5.0,10,100。
由图5可以看出,当coff为0.1时,制冷剂相变速率较慢。进口为全液相,液相流到管道全长的三分之一时,开始出现气相,气相浮在管道上部,呈现明显的分层现象。液相从进口至出口在管道下部均有沉积,大部分液相并未转化为气相。出口处仍有大量液相。壁面温度除出口上部附近在325 k以上,其余部分温度都在299 k左右。该传质系数下的仿真结果与实际不符。
当coff为100时,制冷剂相变速率较快。纯液相由进口流入,在出口附近就迅速相变为气相。气相与液相形成气液两相混合物,有大面积气液两相区,使得气液交界面模糊。管道内大部分为气相。壁面温度在进口前三分之一处较低,为300 k。在管道后段,因气相率过高,导致流体的吸热速率降低,从而导致温度升高。
4. 仿真结果分析
设置管道初始化气相率为1(即管道初始状态内部全为气体),初始压力约为600 Kpa。仿真得到了600 s内冷板表面温度,内部气相率以及内部压力的变化。
温度变化:如图6所示,冷板初始温度与环境温度相同,为298 K。冷板上表面在第0秒开始加热,与此同时,液体制冷剂从入口流入。制冷剂在入口流入时,入口附近液体制冷剂迅速气化,液相制冷剂在转变为气相时吸收冷板中大量热量,冷板温度迅速降低至296 K。第100 s时,制冷剂流过的路径的中心温度最低,一直保持在296 K,并且与冷板周围形成温度梯度。随着制冷剂在管路中流过,此时冷板中制冷剂未流经区域温度不断升高,冷板温差呈现增大趋势,如图所示。第200 s时,冷板中心温度开始下降。制冷剂在第470 s时流经冷板全部区域,此时冷板表面温度在296 K的区域面积约占整体的80%。第600 s时,冷板表面温度基本达到稳定状态,此时冷板出口处温度最高,达到304 K,冷板其余90%区域表面温度大约在296~300 K之间。
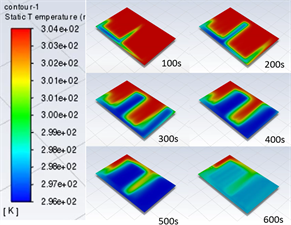
Figure 6. Cold plate surface temperature variation
图6. 冷板表面温度变化
气相率变化:如图7所示,为了减少不必要的相间传质带来的算力需求,减轻计算机运行压力以及更好地观察制冷剂相变过程,设置冷板内部初始气相率为1,也就是冷板内部管道内全为气相制冷剂。因为冷板上表面一直有一个固定的热通量,所以气相制冷剂一直处于饱和或者过热状态,不会发生冷凝现象,继而不会对冷板表面温度以及内部气相率产生影响。制冷剂从冷板入口进入,此时制冷剂迅速相变为饱和蒸汽,气相率为0.2左右。第0~300 s,气相持续生成,气相与液相梯度呈现减小趋势。第500 s时,制冷剂流经冷板全部管道,且管道内70%以上区域的气相率为0.5左右。0~600 s冷板内部制冷剂气相率如图所示。
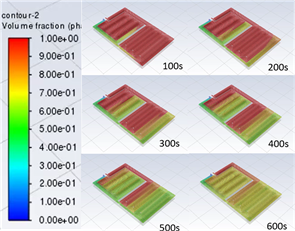
Figure 7. Variation of gas phase rate inside the cold plate
图7. 冷板内部气相率变化
压力变化:如图8所示,冷板内初始压力为587 kpa。随着制冷剂流入,冷板入口处压力缓慢上升。冷板内部压力趋势为从入口至出口压力逐渐减小。在500~600 s之间,冷板整体压力呈现明显上升趋势。最终冷板最高压力达到627 kpa。
综合分析冷板表面温度,内部气相率以及压力可以得出以下结论:冷板表面温度随着直冷剂的蒸发而降低。液相制冷剂受热迅速蒸发,吸收大量热量。液相向气相传质过程越剧烈,冷板表面温度越低。冷板在仿真阶段后期,随着制冷剂从入口以液体状态不断流入,制冷剂大量存在于冷板管道内,液相制冷剂不断相变为气相,导致气相多的管道吸热能力变差,温度继续升高,从而产生更多的换热能力差的气相制冷剂。这些气体如不能及时排出,最终就会导致冷板部分管道区域温度升高,使得整块冷板表面温度分布不均。
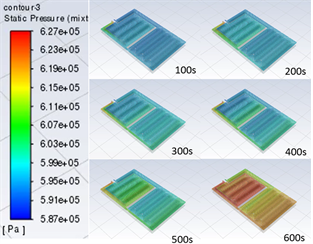
Figure 8. Pressure variation inside the cold plate
图8. 冷板内部压力变化
如图9和图10所示,观察冷板内部流速矢量图可知,两相流体在冷板内流动,在直管内流体流动平缓。流体在弯角处出现湍流。气相率越高,气体密度越小。液相制冷剂不断吸收热量并持续相变成气相,气相组分越来越多,从而导致流体流速加快。流体速度随着气相率的升高而升高。在出口附近,由于气体汇聚,该处流速高达26 m/s。
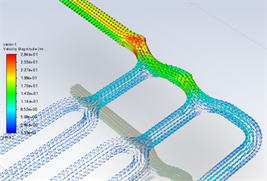
Figure 10. Vector plot of flow velocity at the outlet
图10. 出口处流速矢量图
5. 实验验证
5.1. 实验系统
针对直冷板进行温升实验需要使用一系列实验设备和部件,主要包括:直冷板:通常采用铝材料制作,通过冲压和焊接等工艺加工成型,具有良好的导热性能和散热能力。空调:用于控制实验环境的温度和湿度,保证实验过程的稳定性。压力传感器:用于监测制冷剂在冷板进出口的压力,及时发现并解决可能的质量流量问题。温度采集器:安装在直冷板测试的各个位置,用于测量不同位置的温度值,以便分析温度分布情况。点温仪:用于监测制冷剂出口的过热度,及时发现冷却系统的异常情况,保证实验的安全性。加热膜:可在直冷板的表面进行加热,模拟电池的发热过程,用于验证直冷系统的散热能力。膨胀阀:用于调节制冷剂的流量和压力,保证冷却系统的正常运行。通过上述实验设备和部件,可以对直冷板的散热能力进行全面的测试和分析,为电池包直冷系统的设计和优化提供重要依据。具体的实验系统示意图如图11所示。
加热膜贴于冷板表面模拟电池生热。在冷板表面布置若干热电偶,采集各点温度参数。冷板进出口布置有压力以及流量传感器,以采集进出口压力和制冷剂流量。
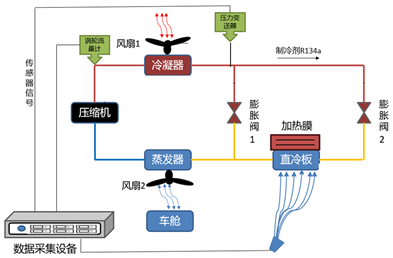
Figure 11. Schematic diagram of the experimental system
图11. 实验系统示意图
5.2. 结果讨论
如图12所示,仿真值与实验值对比,平均误差为1.3℃。进出口温度误差较小,最大误差出现在冷板左侧,为2.0℃。实验条件下,冷板最大温差为7.5℃。最高温度出现在冷板出口,为31.4℃,最低温度出现在冷板进口,为24℃。仿真最高温度同样出现在冷板出口附近,为29.4℃,最低温度出现在进口处,为24.2℃。仿真与实验值温度趋势一致,说明该两相流传热模型能较好的模拟出直冷板的温度分布情况。
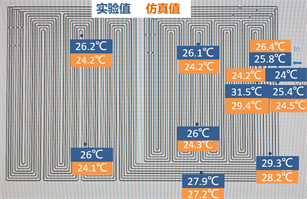
Figure 12. Comparison of experimental and simulated values
图12. 实验值与仿真值对比
5.3. 误差分析
所对比温度值均为冷板表面温度,内部压力及其他物理状态处于稳定后的温度值。由图可见,仿真温度相比实验值略低1℃~2℃,但总体温度趋势与实验相符合。猜测冷板实验采用加热膜加热冷板,仅加热冷板一面,且温度测点在冷板加热面表面,使得实验温度值偏高。
6. 结论
本文采用了计算机模拟方法,开发出了大尺寸冷板仿真方法,并用实验证明了该模型的准确性,为直冷板仿真提供了解决方案。
1) 随着传质系数的增大,制冷剂气相率增大,传热速率降低。仿真模型中具体的传质系数需要与实验对标。
2) 仿真值最高温度出现在出口附近,为29.4℃。实验结果表明,冷板最高温度同样出现在出口过热区,最高温度为31.5℃。
3) 仿真值与实验值对比,平均误差为1.3℃。进出口温度误差较小,最大误差7.8%,出现在冷板左侧,为2.0℃。
参考文献
NOTES
*第一作者。
#通讯作者。