Abstract
Customized heat treatment is essential for enhancing the mechanical properties of additively manufactured metallic materials, especially for alloys with complex phase constituents and heterogenous microstructure. However, the interrelated evolutions of different microstructure features make it difficult to establish optimal heat treatment processes. Herein, we proposed a method for customized heat treatment process exploration and establishment to overcome this challenge for such kind of alloys, and a wire arc additively manufactured (WAAM) Mg-Gd-Y-Zn-Zr alloy with layered heterostructure was used for feasibility verification. Through this method, the optimal microstructures (fine grain, controllable amount of long period stacking ordered (LPSO) structure and nano-scale β' precipitates) and the corresponding customized heat treatment processes (520 °C/30 min + 200 °C/48 h) were obtained to achieve a good combination of a high strength of 364 MPa and a considerable elongation of 6.2%, which surpassed those of other state-of-the-art WAAM-processed Mg alloys. Furthermore, we evidenced that the favorable effect of the undeformed LPSO structures on the mechanical properties was emphasized only when the nano-scale β' precipitates were present. It is believed that the findings promote the application of magnesium alloy workpieces and help to establish customized heat treatment processes for additively manufactured materials.
Highlights
A method for customized heat treatment exploration and establishment for additively manufactured metallic materials was proposed.
The mechanical properties of the additively manufactured Mg alloy were improved after customized heat treatment.
The favorable effect of the undeformed LPSO structure on the mechanical properties was emphasized only when the nano-scale β' precipitates were present.
Export citation and abstract BibTeX RIS

Original content from this work may be used under the terms of the Creative Commons Attribution 4.0 license. Any further distribution of this work must maintain attribution to the author(s) and the title of the work, journal citation and DOI.
1. Introduction
Additive manufacturing (AM) is a revolutionary technique with computer-aided deposition, and has great potential to be used in various fields due to its remarkable advantages of low material wastage, high freedom in geometric design and optimization, highly integrated and multi-functional fabrication, and accelerating product iterations over traditional manufacturing processes. Given the relatively high cooling rate and unique thermal history caused by cyclic heating and cooling procedures, AM-processed microstructures exhibit special and novel characteristics, which are different from traditionally processed counterparts. Ren et al [1] found that the AM process enabled nano-lamellae formation in high-entropy alloys to achieve an outstanding combination of high strength and uniform elongation. Wang et al [2] engineered a new phase with oxygen-rich face-centered cubic structure in the additively manufactured Ti-6Al-4V alloy, demonstrating great potential for strengthening and work hardening. In addition, AM allows to fabricate heterostructured materials that is unachievable to traditional processes. For instance, Zhang et al [3] reported micron-scale concentration modulations (heterogeneity in chemical composition) in the AM-processed Ti-6Al-4V alloyed with a small amount of 316L steel, which was conducive to improving the mechanical properties. Tan et al [4] achieved spatially heterostructured steels via alternative AM of AISI 420 stainless steel and C300 maraging steel to enhance overall mechanical properties. Many investigations suggest that AM can greatly increase microstructure diversity, thus providing more opportunities for fulfilling various requirements on mechanical and functional properties.
The wide range of unique microstructures achievable to AM makes conventional heat treatment processes unsuitable to fully unlock the potential. It has become a consensus to explore customized heat treatment processes for additively manufactured microstructures [5]. Sui et al [6] found that the Laves phase in the additively manufactured Inconel 718 had a faster dissolution behavior than that in the traditionally fabricated counterparts, and developed a low-temperature and short-duration solution heat treatment for optimization, thus obtaining excellent comprehensive mechanical properties [7, 8]. Zhao et al [9] designed a multi-step heat treatment process to generate a fine equiaxed α phase with a size of approx. 5 μm in AM-processed Ti-6Al-4V-ELI for the first time, resulting in remarkably improved ductility (25.1% total elongation). However, rare investigations are focused on optimizing heat treatment processes for AM-processed Mg alloys currently.
Mg and its alloys, as the lightest metallic materials, have excellent damping properties, superior biocompatibility and large hydrogen capacity, enabling its application in aerospace, medical implants, national defense, automotive, etc. AM contributes to further lightening Mg alloy components via structure design and optimization, which is beneficial to emission reduction and energy conservation, thus attracting increasing attention in recent years. To fulfill the growing need for high strength in industry, AM of Mg-Gd-Y-Zn-Zr alloys is currently receiving more focus for the following two reasons. On the one hand, gadolinium (Gd) and yttrium (Y) can provide considerable precipitation strengthening effects via β-series precipitates [10, 11]. On the other hand, Zn element can promote the formation of long period ordered stacking (LPSO) structures in Mg-Gd-Y-Zr alloy and further boost the mechanical properties [12–15]. Most of the current investigations were mainly focused on laser powder bed fusion (LPBF) of Mg-RE (rare earth) -Zn alloys [16–18]. However, considering that Mg alloy powders are more flammable and explosive than other metallic material powders, safety issues are likely to occur during the preparation, storage and transportation of Mg alloy powders, as well as during the LPBF process and the subsequent cleaning procedure [19]. The wire arc additive manufacturing (WAAM) process, which uses wire as the raw material, exhibits minimal safety hazards and higher production efficiency compared with other AM processes, thus demonstrating huge application potential in the fabrication of Mg alloys [20]. Recently, Li et al [21] fabricated a Mg-RE-Zn-Zr alloy sample using the WAAM technology and improved the mechanical properties by conventional heat treatments. Although the investigation preliminary establishes a good foundation for preparing high-strength Mg-RE-Zn alloys via WAAM, the unique features of the AM-processed microstructure are still not taken into account in the establishment of heat treatment processes, especially for the possibly formed heterogeneous microstructures [22, 23]. Moreover, the complex microstructural characteristics of Mg-Gd-Y-Zn-Zr alloy inevitably increase the difficulty in optimization and limit the accurate understanding of the role of the LPSO structure, since the variations of these structures are normally accompanied with the changes in grain size and grain-boundary eutectic phase, and also affect the following precipitation of β' precipitate. Therefore, exploring the principles for establishing customized heat treatment processes based on the unique microstructures of AM-processed Mg alloys is important to accelerating the relevant application.
In this work, the WAAM process of a Mg-Gd-Y-Zn-Zr (GWZ831K) alloy was focused on. A layered heterogeneous microstructure was generated in the WAAM-processed GWZ831K alloy via using an interlayer dwell time of 30 s since it was proven to be conducive to mechanical property improvement in our previous investigation [23]. Customized heat treatment processes were explored and optimized through detailed and systematic investigations on microstructure evolution and corresponding mechanical properties. The effect of the LPSO structure was analyzed. A method for customized heat treatment exploration and establishment for additively manufactured metallic materials was proposed. It is believed that the findings can provide valuable references for tuning the microstructure and enhancing the mechanical properties of the WAAM-processed Mg-RE-Zn series alloys with complex phase constitutes.
2. Experimental methods
2.1. Manufacturing process
In this work, the GWZ831K Mg alloy (Mg-8.1Gd-2.6Y-0.7Zn-0.5Zr, wt.%) wire was used for the manufacturing process. The WAAM system consists primarily of an ABB industrial robot (travel speed of 7 mm s−1), a Fronius CMT welding equipment (input current of 110A), a wire feeder, a high pure argon gas subsystem (flow rate of 20 L min−1), and a robot controller. In addition, the interlayer dwell time was 60 s for the WAAM process. Figure 1 shows the fabricated multi-layer thin-wall sample.
Figure 1. Schematic diagram of the samples. (a) Diagrammatic representation of the WAAM process; (b) schematic diagram of the thin wall; (c) dimension of the tensile coupon.
Download figure:
Standard image High-resolution image2.2. Heat treatment processes
We employed two criteria to preliminary screen heat treatment processes to avoid the time waste caused by trail-and-error exploration. Firstly, the grain-boundary eutectic phase should be completely eliminated, since it not only occupies the strengthening element and affects the following precipitation of the strengthening phase, but also becomes the crack origin site during bear loading process and causes premature failure [24–26]. Secondly, the grain size should remain almost unchanged after heat treatments, since grain growth inevitably decreases the mechanical properties [27, 28]. Based on the above two principles and our preliminary experiments, the solution heat treatment processes utilized in this work were set as follows: 460 °C/1 h, 490 °C/1 h, 520 °C/30 min, 520 °C/1 h, 520 °C/8 h and 580 °C/15 min. It is evident that several high-temperature and short-duration heat treatment processes were settled to tailor the initial microstructure, which was inspired by our previous investigations on AM-processed nickel-based superalloy, in which the eutectic phase exhibited a rapid dissolution behavior. For the solid solution heat treatment and aging treatment, the samples were put in the quartz tubes and oil bath and then quenched in water.
2.3. Microstructure characterization and mechanical testing
Figure 1(b) shows the macro-morphology of the thin-wall sample with the length, height, and width of approximately 120 mm, 80 mm and 14 mm, respectively. The middle region of the thin wall was used for the subsequent heat treatments. Microstructure observation was conducted using the Olympus GX53 optical microscope (OM) and the TESCAN MIRA3 SEM. The x-ray diffractometer with Cu Kα radiation in the 2θ range of 10° – 90° and the TEM (JEOL JEM-200) were performed for phase identification. A tensile test was performed using the MTS material test instrument with a tensile speed of 1 mm min−1 (figure 1(c)). The Vickers hardness test was performed on the heat-treated samples with a 500 g load and a 15 s dwell time.
3. Results
3.1. As-built microstructure
Figure 2 depicts the microstructure of the as-built GWZ831K alloy. It is evident that the microstructure is characterized by an alternatively layered distribution of fine and coarse grains (figures 2(a) and S1, supplementary materials). The fine grains ((9 ± 1.2) μm, FG) appear at the bottom of each melt pool due to the chilling effect of the previously deposited layer caused by the utilization of the interlayer dwell time, while the coarse equiaxed grains ((15.4 ± 1.1) μm, CG) are formed inside each melt pool because of the synergistic effect of the variation in solidification conditions during the progressive solidification process of the melt pool and the in-situ heat treatment effect caused by subsequent deposition process [23]. In addition, the eutectic phase in the microstructure is the (Mg, Zn)3(Gd, Y) phase, as shown in figures 2(c) and (d). TEM images show the presence of some needle-like lamellar structures. Such structures are precipitated from the eutectic phase and grow towards the grain interior. According to the previous studies [29, 30] and the HAADF-STEM images (figures 2(e) and (f)), the lamellar structure is γ' precipitate with a length of hundreds of nanometers. In general, the γ' precipitate is a metastable phase and can transform into an LPSO structure during heat treatment process [29].
Figure 2. The microscopic characterization of the as-built GWZ831K alloy. (a) OM images; (b) SEM images; (c) XRD pattern; (d) HAADF-STEM images and corresponding SAED pattern of the (Mg, Zn)3(Gd, Y) phase; (e) and (f) STEM images and SAED pattern of the γ' precipitates.
Download figure:
Standard image High-resolution image3.2. Microstructure evolution during heat treatment processes
It is evident from figure 3 that the elimination of the heterostructure is more sensitive to heat treatment temperature than duration. Specifically, heterogeneous layered microstructure is still observed after heat treated at 520 °C for 8 h while it is almost erased after 540 °C for only 15 min as shown in figures 3(c) and (d). Given that the layered microstructure is mainly caused by the alternative distribution of different grain sizes, its elimination suggests that grain growth occurs at 540 °C, which is further verified by the EBSD result that several large grains with the size of higher than 50 μm (indicated by black arrows) appear as shown in figure 3(e). The above observation also indicates that the grain size remains almost unchanged after 520 °C for 8 h since the layered microstructure is still clear (figure 3(c)).
Figure 3. The OM characterization of the solution treated GWZ831K alloys. (a) (460 °C/1 h); (b) (520 °C/30 min); (c) (520 °C/8 h); (d) (540 °C/15 min) with (e) inverse pole figure and grain size map; (f) CG region and (g) FG region in (460 °C/1 h) sample; (h) CG region and (i) FG region in (520 °C/30 min) sample.
Download figure:
Standard image High-resolution imageThe phase constituents in the different regions of the heterogeneous structure exhibit different evolution behaviors, as shown in figures S2 and S3 (supplementary materials). For the sample after 460 °C for 1 h, a large amount of the LPSO structures continuously appear in the FG region (figure 3(g)), while the LPSO structures are formed discontinuously in the CG region (figure 3(f)). The intragranular LPSO structures in the FG region are completely erased after heat treated at 520 °C for 30 min as shown in figure 3(i). In this case, the FG region and the CG region exhibit similar phase constituents that are both characterized by the grain-boundary LPSO structures (figures 3(h) and (i)). In addition, it is noteworthy that the main difference in phase constituents of different heat-treated samples is highlighted in the FG region. Therefore, detailed observation of phase evolution is conducted on the FG regions.
The detailed phase evolution with temperature and time is shown in figure 4. The (Mg, Zn)3(Gd, Y) phase (black phase, indicated by yellow arrows) is gradually dissolved and transformed into the block-like LPSO structure (light-grey phase, indicated by blue arrows) on the grain boundary with increasing the duration at 520 °C, as shown in figures 4(a)–(c). With further prolonging the duration, these LPSO structures are transformed from block shape to lamellar shape (green arrow), as shown in figure 4(d). Some investigations indicate that the block-like LPSO has an 18R-type structure, while the lamellar LPSO is the 14H-type [31, 32]. At the temperatures above 500 °C, the metastable 18R-LPSO structure will eventually change into the 14H-LPSO structure [33]. The TEM test results further evidence the above statement by presenting both two types LPSO structures in the sample after 520 °C for 1 h, as shown in figures 4(j)–(l).
Figure 4. The microstructure characterization of the solution treated samples. (a) (520 °C/5 min); (b) (520 °C/15 min); (c) (520 °C/45 min); (d) (520 °C/1 h); (e) (520 °C/4 h); (f) (520 °C/8 h); (g) (540 °C/15 min); (h) (560 °C/15 min); (i) (580 °C/15 min); (j) and (k) STEM images of the LPSO structures and (l) SAED pattern of 14 H-LPSO structure in (520 °C/1 h) sample.
Download figure:
Standard image High-resolution imageAs the duration is extended from 1 h to 4 h at 520 °C, some lath LPSO structures (indicated by orange arrows) are formed along the grain boundaries, as shown in figure 4(e). Previous investigations demonstrate that the lath LPSO, also known as the X phase, is easily formed at the temperatures over 500 °C [34–36], and shares the same lattice structure with the lamellar LPSO [37]. With further increasing the duration to 8 h, more X phase particles are obviously formed in the microstructure, while the content of the lamellar LPSO structures is reduced (figures 4(e) and (f)).
Under the same duration, the increase in heat treatment temperature will also have an important effect on the phase constituent evolution. High temperature can effectively reduce the content of the (Mg, Zn)3(Gd, Y) phase, while suppressing the formation of the LPSO structure simultaneously. Several block-like LPSO structures are formed after 560 °C for 15 min, and only a small amount of the eutectic phase remains after 580 °C for 15 min treatment (figures 4(g)–(i)).
Three kinds of heat-treated samples (460 °C/1 h, 490 °C/1 h and 520 °C/1 h) with different combinations of eutectic phase and LPSO structures are selected to determine the peak aging time at 200 °C. It is evident from figure 5(a) that the difference in phase constituent does not influence the peak aging time, which is 48 h for all the samples. However, the peak microhardness is changed with different solution heat-treated states, which is ascribed to the different degrees of the strengthening elements consumption by different combinations of eutectic phase and LPSO structures. In the following work, the peak aging time of 48 h is used for all the samples to induce the formation of the strengthening phase.
Figure 5. The microscopic characterization of the GWZ831K alloy. (a) The aging hardening curve of the solution treated (460 °C/1 h), (490 °C/1 h) and (520 °C/1 h) samples at 200 °C; (b)–(d) OM image, inverse pole figure and TEM images in (520 °C/30 min + 200 °C/48 h) sample.
Download figure:
Standard image High-resolution imageFigures 5(b)–(d) show the microstructure of the sample after 520 °C/30 min + 200 °C/48 h. The LPSO structures still remain on the grain boundaries (figure 5(b)) as evidenced by the TEM image (figure 5(d)). According to the EBSD test (figure 5(c)), the average grain size is (16.3 ± 2.4) μm in the CG region. The SAED result shows that the β' precipitates form after the aging treatment (figure 5(d)). The lens-shaped β' precipitates can significantly increase the strength of the Mg-RE alloy by hindering the basal dislocation slip and inducing more slipping systems to activate [38, 39]. Overall speaking, the aging heat treatment process has little effect on the LPSO structures and the grain size. Moreover, the microstructure of the aging treated (200 °C/48 h) sample is also studied as shown in figure S4 (supplementary materials). Since no solution heat treatment is performed, the residual (Mg, Zn)3(Gd, Y) phase particles are observed with the appearance of the β' precipitates.
3.3. Room temperature tensile properties
The mechanical properties of the as-built and heat-treated GWZ831K alloy samples are summarized in figure 6(a), figure S5 and table S1 (supplementary materials). It is evident that the mechanical properties are much enhanced by the solution and aging processes. The sample subjected to 520 °C/30 min + 200 °C/48 h exhibits the best tensile property with the ultimate tensile strength (UTS) of (364 ± 7.8) MPa and the elongation (EL) of (6.2 ± 0.5)%, which is also better than the currently reported properties of the additively manufactured Mg alloys (figure 6(b)). Interestingly, the samples subjected to the heat treatments of 520 °C/1 h + 200 °C/48 h and 540 °C/15 min + 200 °C/48 h both demonstrate the comparable UTS. However, given that the abnormal grain growth (figures 3(e) and S6) (supplementary materials) occurs in the sample subjected to a temperature of 540 °C or higher, such kind of heat treatment process is impracticable. Therefore, it is believed that the most suitable post heat treatment is 520 °C/30 min + 200 °C/48 h for the WAAM-processed Mg-Gd-Y-Zn-Zr alloy with heterogeneous microstructures.
Figure 6. Mechanical properties. (a) Engineering tensile stress-strain curves; (b) UTS versus EL summary graphic of our work and other published WAAM-processed Mg alloys [21, 22, 40–49].
Download figure:
Standard image High-resolution imageThe tensile fracture morphologies of the as-built and 520 °C/30 min + 200 °C/48 h samples are shown in figure 7. For the WAAM-processed sample, a few cleavage planes and many dimples can be found in the fractography. In addition, the main crack and some microcracks extend along the grain boundaries (figure 7(c)). Thus, the additively manufactured sample should be a ductile-brittle mixed fracture. After the solution and aging treatment (520 °C/30 min + 200 °C/48 h), the sample presents deeper dimples and fewer cleavage planes (figures 7(d) and (e)). Additionally, the obvious fracture and kink deformation of the LPSO structure can accommodate tensile strain, which is conducive to improving the ductility of the sample (figure 7(f)).
Figure 7. Fracture morphology by SEM. (a)–(c) As-built sample; (d)–(f) (520 °C/30 min + 200 °C/48 h) sample.
Download figure:
Standard image High-resolution image4. Discussion
4.1. Microstructure evolution
Generally, the cast components usually need to be kept at a temperature of 480 °C–520 °C for 12 h to ensure the dissolution of the eutectic phase [35, 50]. Interestingly, the WAAM-processed samples heat treated at a lower temperature and shorter time can not only dissolve almost all the (Mg, Zn)3(Gd, Y) phase particles, but also promote the precipitation of the LPSO structures (figure 3(g)). The microstructure evolutions of the as-built samples in the different solution treatment states are illustrated in figure 8. The change and optimization of the solid solution heat treatment process can be attributed to the unique solidification characteristics of the WAAM-processed microstructures. Compared with the casting process, the WAAM process possesses a faster cooling rate, which induces the non-equilibrium solidification behavior, resulting in the smaller grain size and less eutectic phase content, which helps to shorten the diffusion distance of alloying atoms [37, 51]. Moreover, fast solidification-induced crystal defects may also provide channels for the diffusion of alloying elements [52], which is supported by the fact that the finer grain region exhibits a higher solid solution effect than the coarse grain region in this study.
Figure 8. Schematic illustrating microstructural evolution of the as-built alloy by post-solid solution treatment.
Download figure:
Standard image High-resolution imageWhen heat treated at 520 °C for 30 min, a better solid solution effect is obtained by further dissolving the LPSO structures into the matrix with no grains growing up. However, long duration at 520 °C (for instance, 520 °C/4 h) induces the formation of the X phase. With the duration reaching 8 h, the X phase fills the whole microstructure. According to the previous investigations [53–55], the X phase usually directly precipitates from the (Mg, Zn)3(Gd, Y) phase. However, most of the (Mg, Zn)3(Gd, Y) phase particles can be completely dissolved at 520 °C for 1 h in this work. It is suggested that the X phase may be directly precipitated from the grains. The as-built GWZ831K alloy has smaller grains and a lower eutectic phase content, which reduces the atom diffusion distance [52]. During the subsequent solution heat treatment process, the gradual dissolution of the (Mg, Zn)3(Gd, Y) phase is continuously accompanied with the formation of the LPSO structures. The abundant LPSO structures provide favorable conditions for the formation of the lath X phase [56]. Deng et al [37] also reported a similar phenomenon in the selective laser melted Mg-RE-Zn-Zr alloys.
When the solid solution temperature is increased to higher than 540 °C, the samples achieve a good solid solution effect in only 15 min, and the mechanical properties are comparable to the best. Unfortunately, abnormal grain growth is observed in several samples. This can be explained by the fact that the absence of the intergranular phase particles makes it difficult to impede the movement of the grain boundaries at high temperatures. Thus, for the as-built GWZ831K alloys, the optimal solution condition should not only dissolve the eutectic phase and part LPSO structures, but also retain the fine grains.
The microstructure evolution of the GWZ831K alloy in the optional solution and aging treatment processes is illustrated in figure 9. The aging process that follows the optimal solid solution treatment helps to further precipitate the dense β' precipitates. In addition, due to the low heat treatment temperature, there is no dissolution of the eutectic phase or generation of the LPSO structures during the aging heat treatment process.
Figure 9. Schematic illustrating microstructural evolution of the as-built alloy during post-heat treatment.
Download figure:
Standard image High-resolution image4.2. Strengthening mechanisms
Compared to the cast alloys, the WAAM-processed GWZ831K alloys have a much higher yield strength. The yield strength () can usually be expressed by the following equation:

where ,
and
represent the intrinsic lattice friction stress (∼46.5 MPa), the grain boundary strengthening effect and the second-phase strengthening effect, respectively [57].
The Hall-Petch relation is normally used to determine the grain boundary strengthening contribution [58]:

where d is the grain diameter and k is the H-P coefficient (210 MPa·μm1/2). In this work, the grain size ((15.4 ± 1.1) μm) in the WAAM-processed microstructure is much smaller than that in the as-cast counterpart [59], and the grain boundary strengthening contribution to the yield strength is calculated to be 53.5 MPa. In addition, the enhancement of the mechanical properties is further facilitated by the heterogeneous grain structure, which is made up of FG and CG regions that are spread alternately. The FG regions are normally stronger than CG regions. The former is considered as the hard regions and the latter soft regions. During the tensile process, the strong restriction of the hard regions on the soft regions promotes the creation of hetero-deformation induced stress, which is believed to improve both ductility and strength at the same time [60].
The main second phase is (Mg, Zn)3(Gd, Y). The contribution of can be expressed [21]:

where is the volume fraction of the second phase. It is estimated that the second phase of the as-built sample contributes 59.0 MPa to the yield strength.
The contribution of the fine grain strengthening has not changed after the heat treatment process. Meanwhile, only a small part of the LPSO structures precipitate. The strengthening effect offered by the solid solution strengthening () may be computed using equation (4) [42]:

where is constant (∼1/2),
is the factor associated and
is the solid solubility. Specifically speaking, the
values are determined to be 683 MPa (at.%)−1/2 for the Gd element and 737 MPa (at.%)−1/2 for the Y element, respectively [57]. According to the energy dispersive spectrometer (EDS) results, the WAAM-processed sample is composed of ∼0.83 at.% Gd and ∼0.54 at.% Y, while the heat-treated samples contain ∼0.89 at.% Gd and ∼0.57 at.% Y. Therefore, it was calculated that the
was 36.9 MPa.
Moreover, the strengthening effect of the LPSO structures () can be assessed by using the following equation [32]:

where is the average aspect ratio and
is the volume fraction. The
is the stress at which the α-Mg matrix bears upon yielding [22]. The LPSO structure strengthening contribution is roughly assessed to be 18 MPa.
After the solution and aging treatment (520 °C/30 min + 200 °C/48 h), the yield strength of the GWZ831K alloy sample is increased significantly, which is due to the appearance of the β' precipitates. The nano-precipitate contribution is calculated using the Orowan equation [61]:
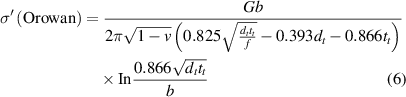
where represents the shear modulus (166 00 MPa),
represents the Poisson's ratio (0.29),
represents the magnitude of the Burgers vector (0.32 nm),
is the average diameter of prismatic plates,
is the planar thickness of prismatic plates and
is the volume fraction of β' precipitates [62]. Depending on the above discussion, figure 10 demonstrates the contribution of the various strengthening mechanisms to the yield strength in the GWZ831K alloy with different states. It is evident from figure 10 that the LPSO structure has limited effect on the yield strength, while the β' precipitates contribute the most.
Figure 10. Strengthening contributions of yield strength for the as-built, (520 °C/30 min) and (520 °C/30 min + 200 °C/48 h) samples.
Download figure:
Standard image High-resolution image4.3. The effect of LPSO structures on mechanical properties
Although many investigations currently try to clarify the effect of the LPSO structures, no consensus has been reached yet. Shao et al [63] indicated the coherent LPSO structures and matrix interface were conducive to enhancing the strength and resisting the fracture. Fan et al [64] believed that the high thermal stability of the LPSO structures prevented the grain boundary movement and restricted the grain growth [32, 65, 66]. However, Liu et al [31] found that the LPSO structures after various heat treatment processes decreased the strength. The nano-scale α-Mg slices embedded between adjacent LPSO structures often act as the weak parts during load-bearing process and are responsible for the decrease in mechanical properties [63]. The reason for the paradox of the effect of the LPSO structure is that its variation is normally accompanied by the evolution of other microstructure features, making it difficult to accurately evaluate the effect of the LPSO structures alone. In this work, the design and utilization of several high-temperature and short-duration heat treatment processes provided an efficient approach to solve this problem.
(1) Comparison between the samples subjected to 520 °C/30 min (Sample-1), 520 °C/8 h (Sample-2) and 580 °C/15 min (Sample-3). Compared with the Sample-1, the Sample-2 has comparable grain size and more LPSO structures, as shown in figure 3. The appearance of large amounts of LPSO structures weakens the solid solution strengthening effect, leading to an inferior room temperature tensile property regarding both strength and elongation in the Sample-2. In addition, the Sample-3 has slightly coarser grains without the LPSO structure compared with the Sample-1, while demonstrating higher YS and UTS with equivalent EL. Considering the negative effect of the increase in grain size on mechanical strength, the strength enhancement in the Sample-3 is ascribed to the improvement of the solution strengthening effect caused by the dissolution of the LPSO structure. Through the above analysis, in the solid-solution heat-treated WAAM-processed Mg alloys (in other words, the microstructure is mainly composed of the LPSO structures), the LPSO structure has no favorable impact on the mechanical properties, or its favorable effect is lower than the solid solution strengthening effect accordingly, thus deteriorating the final mechanical properties.
(2) Comparison between the samples subjected to 520 °C/30 min ± 200 °C/48 h (Sample-4), 520 °C/8 h ± 200 °C/48 h (Sample-5) and 580 °C/15 min ± 200 °C/48 h (Sample-6). When the β'phase precipitates, the situation is changed. The samples with the LPSO structures (Sample-4 and Sample-5) exhibit better room temperature tensile properties than the sample without the LPSO structures (Sample-6) regarding both strength and elongation, although more strengthening phase β' precipitates in the latter. It is reported that the special orientation relationship between nano-β' and LPSO-structure will create nano-scale closed volumes [67, 68]. These closed volumes efficiently limit the stress concentration and the subsequent crack initiation. Meanwhile, the nano-scale closed volumes also obstruct the mobility of both basal and non-basal dislocations [21], thus further enhancing the strength. In addition, the β' precipitates may be efficiently prevented from coarsening by the LPSO structures [69]. However, the formation of a large amount of the LPSO structures will consume more rare earth elements and dramatically decrease the content of the β' precipitates, thus deteriorating the final mechanical properties [70].
It should also be noted that the deformation kink belt formed by the LPSO structures is an effective deformation mode when the base slip is difficult to work [71, 72]. Thus, Hagihara et al [73] proposed that the strengthening contribution provided by the deformation of LPSO structures would increase the yield strength of Mg alloys. However, the WAAM-processed samples do not undergo plastic deformation processes, resulting in a limited kink strengthening effect from the LPSO structures. The above analysis means that the impact of the LPSO structure will be highlighted only when the nano-scale β' phase is present in the WAAM-processed Mg alloys, and the content of the LPSO structure should not be too high. Therefore, the optimal microstructure of the WAAM-processed GWZ831K alloy is characterized by small grains, a certain amount of LPSO structures and nano-scale β' precipitates.
4.4. Customized heat treatment process exploration and establishment
Additively manufactured microstructures require special heat treatment processes to fully exploit their mechanical properties potential. In general, suitable heat treatment processes are established based on an in-depth understanding of the effect of each microstructure feature (such as grain, secondary phases) on the final mechanical properties. However, this procedure is difficult to achieve for such alloys as WAAM-processed Mg-Gd-Y-Zn-Y with sophisticated phase constitutes and layered heterogeneous microstructure, since the evolutions of different microstructure features during heat treatment process are complicated and interrelated. For instance, the undesirable grain-boundary eutectic phase is normally eliminated at high temperature, while the LPSO structure usually precipitates and evolves, and the grain size may be increased at this temperature. In addition, the appearance of the LPSO structure also affects the subsequent precipitation of the nano-scale strengthening phase β'. All these factors will influence the final mechanical properties, resulting in the currently controversial understanding of the effect of the LPSO structure.
In this work, a customized heat treatment process exploration and establishment method is proposed to address the above issue. At first, two criteria are established based on the previous investigations and the strengthening theory, which are involved in eliminating the grain-boundary eutectic phase and keeping grain from growing. Then, several solution heat treatment processes are designed. They are achievable since the eutectic phase in the additively manufactured microstructure exhibits a rapider dissolution behavior compared to that in the traditionally manufactured counterparts. In this case, it is possible to control the grain size and adjust the second phases as well as eliminate the grain-boundary eutectic phase simultaneously. Finally, through comparing the microstructures and mechanical properties of different samples, the effect of the LPSO structure is revealed (section 4.3), and the optimal microstructures (small grain + controllable amount of LPSO structure + nano-scale strengthening phase β') are obtained and the optimized heat treatment process (520 °C/30 min ± 200 °C/48 h) is established. This method can optimize the customized heat treatment exploration and establishment of additively manufactured metallic materials for better performances and wider practical applications.
5. Conclusions
In this study, the customized heat treatment processes were explored and established for the WAAM-processed GWZ831K alloy through detailed and systematic investigations. The main conclusions can be drawn as a result:
- (1)The as-built sample consists of the (Mg, Zn)3(Gd, Y) phase and γ' precipitates. The CG and FG regions in the microstructure are spread alternately.
- (2)The phase constituents of the heterogeneous structure exhibit different evolution behaviors during the heat treatment process. Moreover, with continuously prolonging the duration at 520 °C, the metastable block-like structure is gradually changed into the lamellar LPSO structure, and then into the lath LPSO structure.
- (3)The peak-aging time at 200 °C for the GWZ831K alloy is 48 h to induce the formation of the β' precipitates from the matrix. The aging treatment does not affect the LPSO structures.
- (4)An optimal microstructure (fine grain + a certain amount of LPSO structures + nano-scale β' precipitates) and the corresponding customized heat treatment process (520 °C/30 min + 200 °C/48 h) are obtained to achieve a combination of a high strength of 364 MPa and a considerable elongation of 6.2%.
Acknowledgments
This work is supported by the Projects of Major Scientific and Technological Achievements Local Transformation of Xi'an (2022JH-ZDZH-0039), International Science and Technology Cooperation Program of Shaanxi Province (2023-GHZD-50), Project of Qin Chuangyuan 'Scientist + Engineer' team construction, Key R&D plan of Shaanxi Province (S2023-YF-QCYK-0001-237), Projects of Major Scientific and Technological Achievements Local Transformation of Xi'an (2022JH-ZDZH-0039), National Natural Science Foundation of China (52101134), Natural Science Foundation of Guangdong Province (2022A1515010275), Scientific Research Program Funded by Shaanxi Provincial Education Department (22JK0479), Doctoral Dissertations Innovation Fund of Xi'an University of Technology (101-252072305), Research Start-up Project of Xi'an University of Technology (101-256082204), Natural Science Foundation of Shaanxi Province (2023-JC-QN-0573), Natural Science Basic Research Program of Shaanxi(2023-JC-YB-412).
Conflict of interest
The authors declare that they have no known competing financial interests or personal relationships that could have appeared to influence the work reported in this paper.
Supplementary data (3.2 MB PDF)