Abstract
This paper presents a new measurement system based on integration method that can provide all-weather dependability and higher precision for the measurement of FAST's feed support system. The measurement system consists of three types of measuring equipments, and a processing software with the core data fusion algorithm. The Strapdown Inertial Navigation System (SINS) can autonomously measure the position, speed and attitude of the carrier. Its own shortcoming is that the measurement data diverge rapidly over time. SINS must combine the Global Positioning System (GPS) and the Total Station (TS) to obtain high-precision measurement data. The Kalman filtering algorithm is adopted for the integration measurement system, which is an optimal algorithm to estimate the measurement errors. A series of tests are carried out to evaluate the performance. For the feed cabin, the maximum RMS of the position is 14.56mm, the maximum RMS of the attitude is 0.095°, these values are less than 15mm and 0.1° as the precision for measuring the feed cabin. For the Stewart manipulator, the maximum RMS of the position is 2.99mm, the maximum RMS of the attitude is 0.093°, these values are less than 3mm and 0.1° as the precision for measuring the Stewart manipulator. As a result, the new measurement meets the requirement of measurement precision for FAST's feed support system.
Export citation and abstract BibTeX RIS
1. Introduction
The Five-hundred-meter Aperture Spherical radio Telescope (FAST) is the world's largest single dish and the most sensitive radio telescope, which is located in Guizhou Province, China. The construction was completed in September 2016. After 3 years of commissioning work, the telescope is now ready for open running.
The orientation of the telescope receiver is controlled by the feed support system. As shown in Figure 1, the telescope's feeds aremounted in a 30-ton feed cabin at a height of about 140 meters and with a movement range of about 206 meters. The feed cabin is suspended and driven by six parallel cables. To realize high-accurate positioning of the feeds, a fine-adjusting mechanism including an AB rotator and a Stewart manipulator is inserted between feeds and the cabin body to compensate for the vibration and deviation caused by large-span cables. The real-time position and attitude of the feed cabin are measured and compared with the theoretical planning value. The difference value is provided to the control mechanism of six parallel cables as control information. To accurately locate the feeds, the real-time position and attitude of Stewart manipulator need to be measured to provide a basis for adjusting the Stewart manipulator.
Fig. 1 (a) Illustration of the FAST telescope, (b) the feed cabin and Stewart manipulator.
Download figure:
Standard imageAccording to the sensitivity requirements of the telescope, the pointing accuracy of the telescope receiver is required to be 16'', the control accuracy of the feed cabin is 30mm. The measurement accuracy of the feed-cabin's position is 15 mm, the measurement accuracy of its attitude is about 0.1°, the measurement accuracy of the Stewart manipulator's position is 3 mm, and the measurement accuracy of its attitude is about 0.1° (Jiang et al. 2019).
In the early stage of FAST's commissioning, the measurement scheme of the feed support system adopted total station. The angle accuracy of total station can reach 0.5'', the position accuracy of short-range can reach less than 0.5mm. However, total station has the disadvantages of uncertain time delay and it is sensitive to the weather conditions. Weather such as rain, fog and light intensity can cause the total station to fail to find the target and the measurement accuracy also decreases significantly. This decrease affects the control accuracy of the feed support system and results in the pointing deviation of the telescope feeds. When the deviation is too large, the telescope fails to observe.
To extend the effective observation time of FAST, the measurement scheme of the feed support system should meet the all-weather requirement. However, the total station cannot meet this demand and so the measurement scheme has been upgraded to the integration measurement. The new measurement scheme includes a strapdown inertial navigation system (SINS), global positioning system (GPS) and total station (TS). SINS provides position, speed and attitude data without external information, but SINS can only guarantee short-term accuracy. However, SINS works independently for a long time, the measurement data diverge rapidly and the measurement accuracy decreases significantly (Qin 2014). The current RealTime Kinematic (RTK) GPS can achieve centimetre-level position accuracy with a local reference station. It is wellknown that multiple GPS antennas can be used to determine the attitude (Crassidis & Markley 1997). However, GPS has shortcomings such as satellite signal loss, wholecycle ambiguity, and signal multipath effect. The integrated SINS/GPS can make up these shortcomings and provide all-weather and high-accuratemeasurement data about position and attitude. The measurement of the feed cabin uses integrated GPS/SINS. The position measurement accuracy of the Stewart manipulator is 3mm. Only TS can meet this high demand, consequently the Stewart manipulator uses integrated TS/SINS. The integration algorithm utilizes a Kalman filter, which has became a standard data fusion approach in GPS/SINS integration system. A Kalman filter is also used for the integrated TS/SINS on the Stewart manipulator.
2. Description of Integration Measurement Scheme
The tracking speed of the feed cabin is 22 mm s−1, and the maximum speed of the changing source is 400 mm s−1. The maximum inclination of the feed cabin is 15°, and the maximum inclination of the Stewart manipulator is 30°. As shown in Figure 2(a), on the outer frame of the feed cabin, six choke antennas are installed at equal intervals to receive satellite signals, among which three are BeiDou receivers and the other three are Leica receivers. They are used as mutual backups to improve the system's reliability. Two local reference stations are installed on the mountain near the telescope, whose position coordinates are known accurately. RTK was used to obtain the center position of the feed cabin. Two high-precision strapdown inertial navigation system devices are installed in the feed cabin: one for the feed cabin measurement and the other for the Stewart manipulator measurement. SINS device consists of a three-axis gyroscope, and a three-axis accelerometer. Six high-precision total station instruments are placed on the measurement stations through FAST's reflecting surface, to measure position of the Stewart manipulator by the distance intersection method in Figure 2(b).
Fig. 2 Illustration of the hardware in the integration measurement system.
Download figure:
Standard image2.1. Hardware Specifications
To ensure high-precision position and attitude measurement, the integration measurement system uses highprecision measurement devices such as SINS, GPS receiver and TS. The error distribution of each device is shown in Tables 1 to 3.
Table 1. SINS Performance
Index name | gyro value | acc value |
---|---|---|
Scale factor repeatability | 20 ppm | 100 ppm |
Scale factor nonlinearity | 20 ppm | 100 ppm |
Measurement range | ±400° s−1 | ±50 g |
Stability of zero offset | 0.01° h−1(1σ) | 100 μg |
Repeatability of zero offset | 0.01° h−1(1σ) | 100 μg |
Random walk | 0.001° h−1/2 | N/A |
Table 2. GPS Receiver Performance
Index name | Value |
---|---|
Plane static accuracy | ±6 mm |
Altitude static accuracy | ±8.5 mm |
Combined postprocessing accuracy | ±5 mm+1 ppm |
Data update frequency | 20 Hz |
Table 3. TS Performance
Index name | Value |
---|---|
Angle error | 0.5'' |
Position error | 0.5 mm+1 ppm |
Time delay | 10 ms |
Measure range | 1.5 m–3500 m |
Measure time | 2.4 s (one time) |
2.2. Measurement Process
The process of the measurement system is shown in Figure 3. The integration measurement system starts, TS initializes to find the measurement targets and receives the real-time data from the weather station. GPS receivers search for the available satellite signals and establish a communication link with the local reference stations. SINS conducts initial alignment to determine the initial attitude of the measured object; i.e., yaw, pitch and roll. Then the SINS updates the attitude, speed and position, and finally Kalman filter is used for information integration to obtain the high-accurate measurement results. Because the feed support system moves at a low speed, the yaw error calculated by SINS is large, and a multiple GPS antennas scheme is adopted to determine the yaw of the feed cabin. Both the A-B axis and the Stewart manipulator are rigid bodies, consequently the yaw of the Stewart manipulator can be derived by extrapolating attitude of the GPS/SINS integration system. When TS cannot use, the position and attitude of the Stewart manipulator are calculated with the feed cabin's measurement information and the moving value of A-B axis and six bars in the feed cabin. The A-B axis and six bars are controlled by the optical encoder multiturn absolute, this encoder's attitude accuracy is less than 0.4'', its position accuracy is less than 1 mm. This precision can meet the requirement, such as attitude accuracy is 0.1° and position accuracy is 3 mm, for measuring the Stewart manipulator.
Fig. 3 Process of the integration measurement system.
Download figure:
Standard image3. Calculation Method of Integrated Measurement
3.1. SINS Initial Alignment
The initial alignment of SINS is a process of determining the reference navigation coordinate frame. SINS is just a startup. The orientation of the feed-cabin body coordinate frame (b-frame), relative to each axis of the reference navigation coordinate frame (n-frame), is completely unknown or not accurate enough. Therefore, it cannot enter the navigation state immediately. The coarse alignment method can determine the angle between b-frame and n'-frame with two vectors such as gb and . When the feed support system is stationary or moving at a constant speed, the gyros measure the similar earth rotation rate, the accelerometers measure the local gravitational acceleration (Gu et al. 2008).
The attitude matrix , which relates the body frame (b-frame) to the computational navigation frame (n'-frame), could be calculated by the following equation:
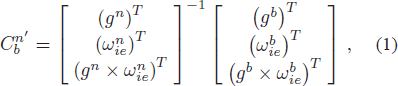

where gn is the gravity vector in n frame, is specific force vector from accelerometers output.
is the earth rotation rate resolved in n frame,
is angular rate vector from gyro output.
After coarse alignment, a fine alignment follows. This calculates the misalignment angle (ϕ) between n'-frame and n-frame. The attitude matrix is modified by ϕ to get a more accurate attitude matrix
:

3.2. SINS Numerical Update
The updating algorithm of SINS consists of position-updating, velocity-updating and attitude-updating. The attitude -updating is the core, and its precision plays a decisive role in the accuracy of the SINS. The attitude-updating can be calculated as follows:

The velocity-updating can be described as follows:

The position-updating can be calculated as follows:

where superscript n refers to the n-frame, superscript b refers to the b-frame. is attitude matrix,
is attitude rate matrix.
is the angular rate vector of b-frame with respect to n-frame projected in b-frame,
is the angular rate vector of n-frame with respect to earth frame (e-frame) projected in n-frame. Vn is velocity vector,
is velocity rate vector, rn is position vector,
is position rate vector.
By simultaneous Equations (4) to (6), the attitude, velocity and position of the carrier can be calculated. However, the SINS has inherent defects such as divergence of navigation accuracy over time and poor long-term stability. To solve this problem, the measurement system aids the GPS and TS devices.
3.3. Kalman Filter
The essence of integration measurement is state estimation. The Kalman filter is a set of mathematical equations that provides an efficient computational means to estimate the state of a process, andminimizes the rootmean squared error of that state (Welch & Bishop 2001). The state vector of the Kalman filter is 15 dimensions in the integration measurement system, which is described as follows:

where E, N and U are, respectively, east, north and up. The last six terms are the gyro zero drift error and the accelerometer sensor error, which are repeatability errors of inertial devices that have great impact on the accuracy of the system. The first nine terms are,respectively, attitude, velocity, and position error vectors, which can be derived from Equations (4) to (6).
The derivation of attitude error vectors is as follows:

Substitute Equations (8) and (3) into Equation (4) and use the attitude quaternion method, and obtain the attitude error vector Equation (9):

The derivation of velocity error vectors is as follows:
Equation (5) is the ideal velocity equation, and the actual velocity equation is as follows:

Subtract Equation (10) from Equation (5)
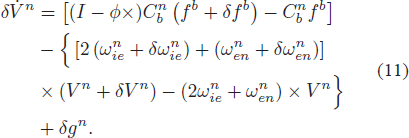
Expand Equation (11) and omit the second order small quantities of the error, the velocity error vectors Equation (12):
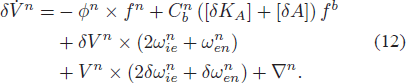
The derivation of position error vectors is as follows:
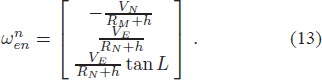
Substitute the angular rate of b-frame into Equation (6), and solve the differential equation to get the position vectors, they are as follows:

Take the derivatives of Equation (14), and get Equations (15)–(17):

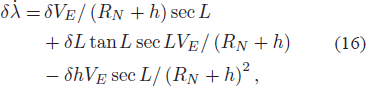

where L is latitude, λ is longitude, h is height. KG is the gyro scale coefficient error, G is the gyro installation error. KA is the accelerometer scale coefficient error, A is the accelerometer installation error. RM and RN are constants.
In integration measurement system, the measurement error is often used as a state vector. Because the Kalman filter is a linear filter, the prediction equation of the measurement error is linear. Generally, the measurement error is relatively small, its higher order items can be ignored to simplify the prediction equation of the measurement error (Yan 2007). The Kalman filter equation includes state equation and measurement equation, which are as follows:


where subscript k − 1 is the last time, k is the current time. F is the state transition matrix, H is the measurement matrix, W is the system noise, V is the measurement noise, Z is a measurement vector, in the integration of GPS and SINS, the form of measurement vector ZG – S is as Equation (20), and in the integration of TS and SINS, the form of measurement vector ZT − S is as Equation (21):


In practice, due to the strong observability of position and velocity vector, the initial value of state vector and corresponding root mean square error matrix is allowed to be relatively large, and they will converge rapidly with the update of filtering. Secondly, the smaller the variance matrix of system noise is, the lower the utilization rate of the measurement vector is. However, the utilization rate of measurement vector is higher when the variance matrix of measurement noise is smaller, and vice versa (Yan 2019). The Kalman filter automatically adjusts the utilization rate of state information and measurement information according to the size of state noise and measurement noise, which makes the most reasonable estimation of the current state. In the process of filtering, the optimal estimation value of state vector is continuously used to modify the SINS calculation value, to make it close to the real position and attitude value. The feedback of Kalman filter is helpful to keep the measurement error equation linear.
4. Data Analysis
The experiment has been conducted on FAST, in Guizhou province, China, to evaluate the integration measurement system. In the experiment, the total stations and the astronomical observation trajectory were used as the references to evaluate the accuracy of the integration measurement solution. The experiment was carried out when the weather conditions is available without rain, fog and strong sunshine, which ensures stable operation of TS. The telescope changes the source in first 180 seconds of the experiment to lock onto the observed objects, followed by about 600 seconds of tracking the objects. Because the integration measurement's accuracy of the tracking source is the main focus, the analyzing of tracking source is described in detail. The analyzing process of changing source is similar to the tracking source, so only Table 6 is used to show the integration measurement's accuracy in the changing source state. The experiment's source is 0029+349, the observation time is from 15:32:10 to 15:45:02 on 2020 February 25. The right ascension of this source is 00:29:14.24, its declination is 34°56'32.2''. In tracking state, the zenith angle is [11.5°, 12.9°], the azimuth is [319.4°, 326.6°].
Table 4. The Error between GPS/SINS and TS in Tracking
Feed cabin | X | Y | Z | yaw | pitch | roll |
---|---|---|---|---|---|---|
Tracking Ave | –0.11mm | 0.27mm | 2.84mm | –0.175° | –0.002° | –0.001° |
Tracking Rms | 5.58mm | 4.05mm | 5.62mm | 0.018° | 0.095° | 0.095° |
Table 5. The Error between Planned Trajectory and TS/SINS in Tracking
Stewart manipulator | X | Y | Z | yaw | pitch | roll |
---|---|---|---|---|---|---|
Tracking Ave | –2.82 mm | –1.00 mm | 2.48 mm | 0.110° | –0.004° | –0.001° |
Tracking Rms | 2.62 mm | 1.91 mm | 2.76 mm | 0.027° | 0.078° | 0.093° |
Table 6. The Error between Reference and Measuring in Changing Source
various error | X | Y | Z | yaw | pitch | roll |
---|---|---|---|---|---|---|
Feed cabin Ave | –0.96 mm | 6.72 mm | 2.90 mm | –0.120° | –0.141° | –0.137° |
Feed cabin Rms | 14.56 mm | 6.43 mm | 6.12 mm | 0.088° | 0.094° | 0.061° |
Stewart manipulator Ave | –0.62 mm | –0.13 mm | 4.26 mm | 0.078° | 0.006° | –0.172° |
Stewart manipulator Rms | 2.99 mm | 2.48 mm | 2.99 mm | 0.049° | 0.093° | 0.075° |
4.1. Verifying the Accuracy of the GPS/SINS Results
The GPS/SINS measurement scheme is used for the feed cabin. The measurement data of total station can be used as a reference. The total station's attitude measurement accuracy is 0.5'', the position measurement accuracy is 5 mm, which are all superior to the measurement requirements of the feed cabin. At the outermost edge of the feed cabin, there are six optical targets. The total station can track these six targets to work out the real-time position and attitude of the feed cabin, which can be used as a reference value to verify the accuracy of GPS/SINS results.
In the accuracy experiment of GPS/SINS, because the difference between TS data and GPS/SINS integrated data is a very small value compared with the experimental data range, TS data and GPS/SINS integrated data cannot be differentiated in a figure. Therefore, only the integrated GPS/SINS result are shown in Figures 4 and 5, the error results between GPS/SINS data and TS data are shown in Figures 6 and 7.
Fig. 4 Integrated position of the feed cabin while tracking the source.
Download figure:
Standard imageFig. 5 Integrated attitude of the feed cabin while tracking the source.
Download figure:
Standard imageFig. 6 Position error between GPS/SINS and TS while tracking the source.
Download figure:
Standard imageFig. 7 Attitude error between GPS/SINS and TS while tracking the source.
Download figure:
Standard imageFrom Table 4, the maximum root mean squared error of the angle is 0.095°, the maximum root mean squared error of the position is 5.62 mm. These values are less than 15 mm and 0.1° as the precision for measuring the feed cabin, so the position and attitude accuracy of integrated GPS/SINS can meet the measurement requirements of the feed cabin.
4.2. Verifying the Accuracy of the TS/SINS Results
The TS/SINS measurement scheme is used for the Stewart manipulator. According to the design requirements, the position measurement accuracy of the Stewart manipulator is 3 mm. However, in a scale of 206 meters and a height of 140 m, there is no measurement equipment with a higher precision than 3 mm. No specific measuring equipment can be found as a reference. From the perspective of practical application, the main task of the Stewart manipulator is making telescope receivers to accurately accept the radio source signal. Therefore, the astronomical observation trajectory is used as a reference for the measurement accuracy of the Stewart manipulator.
The astronomical observation trajectory (azimuth and zenith angle) in the horizontal coordinate system can be calculated according to the right ascension, declination and observation time of the source 0029+349, as shown in Figure 8. With this value, the planned position trajectory (X-Y-Z) of Stewart manipulator in the FAST coordinate system can be derived, then the planned attitude trajectory (yaw-pitch-roll) of Stewart manipulator can be calculated according to the deformation strategy of the telescope. By comparing the error between the planned trajectory of the Stewart manipulator and the TS/SINS integrated measurement, we can verify accuracy of TS/SINS Results. The planned trajectory of the Stewart manipulator and the integrated TS/SINS result of tracking source are shown in Figures 9 and 10. In Figure 9, the red line is the planned position trajectory of the Stewart manipulator and the blue line is the TS/SINS integrated position. In Figure 10, there is the red line is the planned attitude trajectory of the Stewart manipulator and the blue line is TS/SINS integrated attitude. The error results between the planned trajectory and TS/SINS data are shown in Figures 11 and 12.
Fig. 8 Astronomical observation trajectory in the horizontal coordinate.
Download figure:
Standard imageFig. 9 Position of planned trajectory and TS/SINS while tracking the source.
Download figure:
Standard imageFig. 10 Attitude of planned trajectory and TS/SINS while tracking the source.
Download figure:
Standard imageFig. 11 Position error between planned trajectory and TS/SINS in tracking.
Download figure:
Standard imageFig. 12 Attitude error between planned trajectory and TS/SINS in tracking.
Download figure:
Standard imageFrom Table 5, the maximum root mean squared error of the angle is 0.093°, the maximum root mean squared error of the position is 2.76 mm. These values are less than 3 mm and 0.1° as the precision for measuring the Stewart manipulator, so the position and attitude accuracy of integrated TS/SINS can meet the measurement requirements of the Stewart manipulator.
In Table 6, the errors between reference and measuring in changing source are shown. For the feed cabin in the changing source state, the maximum root mean squared error of the angle is 0.094°, the maximum root mean squared error of the position is 14.56 mm. For the Stewart manipulator in the changing source state, the maximum root mean squared error of the angle is 0.093°, the maximum root mean squared error of the position is 2.99 mm. Consequently, the position and attitude accuracy of integrated measurement can meet the requirements of the changing source state.
5. Conclusions
The integration measurement system can provide all-weather dependability and higher precision for the measurement of FAST's feed support system. A Kalman filter algorithm is used to integrate SINS data with GPS data to generate the attitude and position solutions of the feed cabin. Meanwhile, the algorithm fuses SINS data with TS data to generate the attitude and position solutions of the Stewart manipulator. To ensure a non-divergence and available solution in the long term, the Kalman filter algorithm constantly updates the estimation of measurement errors. The TS and the astronomical trajectory are used as the references to evaluate the accuracy of the integration measurement solution. The experimental results show that the integration measurement system is stable and can correctly determine attitude and position of the feed support system. Therefore, the RMS meets our precision requirements.
Acknowledgements
This work was funded by the National Natural Science Foundation of China (Grant No. 11673039), the Open Project Program of the Key Laboratory of FAST, NAOC, Chinese Academy of Sciences and the Key Laboratory of Radio Astronomy, Chinese Academy of Sciences.