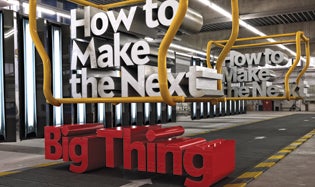
When Thomas Edison invented a practical electric lightbulb more than 130 years ago, he performed thousands of experiments on prototypes, and we still marvel at his methodical patience today. A modern inventor proposing a similar approach, however, would more likely elicit laughter than praise. Product research and development more and more lives in the realm of bits and bytes, with engineers designing, testing, tweaking and even demonstrating new ideas via computer before any physical version exists.
Powerful computer servers performing highly calculation-intensive tasks, aka high-performance computing (HPC), now make all the difference between new technologies that launch and those that languish. This “digital manufacturing” takes place across thousands to millions of processors before a company produces any physical parts. Consumer goods manufacturers are using digital modeling techniques that far exceed those that big firms in industries such as aerospace introduced years ago. The strategy lowers design and production costs and helps to move goods from concept to store shelves faster than ever before. Computer-drawn models and complex digital simulations increasingly dictate what those items look like, how they are made, what they are made of and how they will perform together. Driven by Moore's law, which holds that computer processing power doubles roughly every 18 months, HPC capabilities should advance another 1,000-fold in the coming years. It is no surprise, then, that in the words of the nonprofit Council on Competitiveness, we are entering an age in which “to outcompete is to outcompute.”
On supporting science journalism
If you're enjoying this article, consider supporting our award-winning journalism by subscribing. By purchasing a subscription you are helping to ensure the future of impactful stories about the discoveries and ideas shaping our world today.
The following examples provide a glimpse of state-of-the-art digital manufacturing as well as some hints about where technology will take the process in the near future.
Turning Tide
Procter & Gamble (P&G) engineers realize that most consumers do not devote much thought to how a lot of everyday products are made, dismissing as “easy” the manufacture of essentials such as food, cleaning products and even toilet paper. (The machine P&G uses to manufacture its toilet tissue, by the way, costs nearly $250 million and has more moving parts and lines of code than many military aircraft.) Several years ago, when the company still owned the Pringles brand of potato chips (now in the hands of Kellogg), P&G digitally modeled the airflow over the snacks as they moved—very, very rapidly—down the production line. This research led to adjustments that kept the chips from taking off like little aircraft and crashing in a pile.
Tide Pods were at an entirely different level of complexity. The laundry packets consist of three chambers filled with liquid detergent, stain remover and brightener and are enveloped in a dissolvable film. P&G relied on several million hours of computer processing time to ensure that its Tide Pods properly reacted with washing machine water to release their liquids and effectively clean dirty laundry.
Much of that time went to figuring out how to manufacture the pods. P&G performed structural analysis to calculate and minimize how much the dissolvable film would wrinkle when cut. Fluid dynamics calculations determined how to quickly fill the pods with detergent without splashing any over the edge, which would make the pods hard to seal.
Surfactant-based liquids have interesting behaviors, which meant P&G researchers also needed to perform molecular modeling to understand how the formation of nanoscale structures—micelles and vesicles—might inhibit the product's stability and performance. Digital models depicting how the soft, squishy pods would settle over time when not in use also helped P&G design the container in which they are sold. The work enabled the company to meet its goals for production: each packet is assembled in about a second at a defect rate of less than a one in a billion.
Power Pump
Despite P&G's successes, switching from traditional methods to HPC-based digital manufacturing is a significant challenge. It requires three simultaneous shifts: from physical testing facilities to computing facilities, from approximate methods to more complex but more accurate techniques, and from a culture of troubleshooting to predictive up-front design.
In New York State's Finger Lakes region, ITT Goulds Pumps has made pumps for chemical, mining, power and several other industries since the 1840s. Goulds did not have in-house resources like P&G did to build its own digital manufacturing capability. Instead the company approached the Computational Center for Nanotechnology Innovations, a partnership among Rensselaer Polytechnic Institute, IBM and New York State. Rensselaer helped Goulds transform its computer-aided design (CAD) drawings into “meshed” 3-D models—broken into millions of small areas across which engineers could calculate fluid flow. It also created a process that set up, ran and analyzed pump design options. Goulds went on to develop an award-winning new pump design. Going forward, massively parallel computing will help the company's engineers avoid cavitation—bubble formation—which can rob performance and cause wear.
In Indiana, Jeco Plastic Products tells a similar story. In response to a major auto manufacturer's search for shipping pallets, Jeco proposed plastic transport structures that could outperform metal ones from foreign competitors. Yet the cost of retooling its facility to make and test different prototype plastic pallets—without any guarantee of a buyer—was daunting. Nor could Jeco accurately model new designs on its computers in-house. So the company partnered with Purdue University and the Ohio Supercomputer Center to digitally develop and test Jeco's design. The consortium—a Council on Competitiveness public-private partnership—develops software, purchases supercomputer time and trains smaller manufacturers in this technology. The result: a new order and entry into a market Jeco estimates could bring $23 million in revenue and create 15 jobs.
Born Digital
When there are millions of combinations of materials, manufacturing processes and designs to choose from—rather than the thousands Edison faced—the ability to model and explore many options at once is perhaps the only way to bring new products to market. Pliant Energy Systems knows this well. The Brooklyn-based start-up has a revolutionary concept for generating power from moving water using so-called smart materials that generate power as they flex and bend. Pliant's hydrokinetic devices could literally be dropped into a stream and start generating electricity or be configured as self-powered irrigation pumps. The breadth of design options—and the challenges of building physical prototypes and understanding their behavior—made predictive computational analysis crucial.
Digitally modeling water flow in an open stream requires massively parallel computation that divides the work among many processors to increase speed. Predicting how long, flexible fronds or tubes of electroactive polymers will bend in flowing water—not to mention optimizing the power output of a device using these materials—requires the coupling of device and water-flow models, a feat at the cutting edge of what high-performance computers can do today. Working with Rensselaer, Pliant won a U.S. Small Business Administration grant of nearly $300,000, in part because it demonstrated the digital tools and expertise needed for cost-effective development of its technology. Now the company can create even more sophisticated physics-modeling capabilities and digitally design more advanced prototypes.
Pliant's digital manufacturing success is part of a larger trend. Chris Bystroff, an associate professor in Rensselaer's biology and computer science departments, has developed techniques to design and manufacture custom proteins. Such proteins could act as molecular biosensors that glow in the presence of, for example, dengue fever or H5N1 viruses. Bystroff and the University at Buffalo, S.U.N.Y., are packaging his digital design process behind a Web interface that does in hours what used to take days using antibodies.
Digital manufacturing may seem like a familiar concept, but faster, more affordable computers and increasingly complex software mean that new products, whether they fight grass stains on jeans or viruses invading the human body, will now do so first in the land of 0's and 1's.
For more on the future of manufacturing, go to ScientificAmerican.com/may2013/manufacturing