Abstract
A two-phase flow, three-dimensional, steady-state model is developed to study the flow field and volume fraction distribution in a stirred tank used in the processing of silicon carbide-reinforced aluminum composites in the melt state. The aim is to optimize the stirring to obtain a good mixing of SiC particles. The model is based on the general-purpose code PHOENICS. In addition to the liquid-aluminum phase, the SiC particles are treated as a nonviscous second phase. Interphase momentum transfer occurs through a drag force. Sedimentation is simulated by assigning a high viscosity to the second phase and removing the gravity force when particle concentration reaches a critical value. The stirrers' blades impart a momentum on both phases, proportional to their respective volume fractions. A water model is simulated first, followed by the real Al-SiC melt. The study reveals the importance of particle size that affects the drag force applied on the particles and hence their motion and distribution. The model can be used to study the effect on mixing of tank geometry and the stirrers' operation.
Similar content being viewed by others
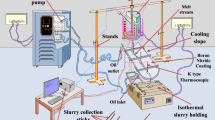
Abbreviations
- a_ :
-
blade area crossing a cell (m2)
- Ā c :
-
cell-averaged blade area (m2)
- Ā f :
-
time-averaged blade area (m2)
- A p :
-
area opposed to flow by the particles (m2)
- C 1, C2 :
-
constants (in log law of wall)
- C D :
-
drag coefficient of cylinder (Eq. [2])
- C d :
-
drag coefficient of blade (Eq. [15])
- C f :
-
skin friction factor (Eq. [8])
- C μ :
-
constant in turbulence model (Eq. [11])
- d :
-
thickness of blade (m)
- D p :
-
diameter of particles (m)
- F D :
-
drag force (Eq. [2]) (N)
- g :
-
acceleration of gravity (m/s2)
- k :
-
kinetic energy of turbulence (m2/s2)
- K 1, K2 :
-
constants (in log law of wall)
- l :
-
total displacement of blade in a cell (m)
- L p :
-
length of particles (m)
- n :
-
number of blades in an impeller
- N p :
-
number of particles in a cell
- r :
-
radius of blade revolution (m)
- r 1, r2 :
-
volume fraction of each phase
- s :
-
displacement of blade in the cell (m)
- S :
-
source term in the conservation equation
- U, V:
-
velocity (vectors) (m/s)
- V c :
-
volume of cell (m3)
- V p :
-
total volume of particles in cell (m3)
- u, v, w :
-
velocity components in three directions (m/s)
- x, y, z :
-
cartesian coordinates (m)
- 0:
-
initial value
- 1,2, i phase 1, phase 2, phaseic :
-
cell eff effective (viscosity)
- g :
-
gravity (force)
- l :
-
laminar (viscosity)
- p :
-
particle ref reference (density)
- t :
-
turbulent (viscosity)
- u, v,w :
-
components ofS in thex, y, z directions ∞ free (fluid flow velocity) Greek letters
- Γϕ :
-
exchange coefficient for the variable ϕ
- ε :
-
dissipation rate of kinetic energy of turbulence (m2/s3)
- ϕ:
-
general variable of conservation equation
- μ:
-
viscosity (dynamic) (kg/m · s)
- v :
-
viscosity (kinematic) (m2/s)
- ρ:
-
density (kg/m3)
- θ:
-
angle of blade tilt (deg)
- ω:
-
speed of blade rotation (r/s)
References
R. Ouellet, R.T. Bui, R. Provencher, and T. Bourgeois:Modeling the Stirring of Al SiC Composites, 32nd Ann. Conf. of Metallurgists, The Metallurgical Society of CIM, Quebec City, 1993, pp. 163–75.
D.B. Spalding:Math. Comput. Simul., 1981, vol. XXIII, pp. 267–76.
P. Gerhart, R. Gross, and J. Hochstein:Fundamentals of Fluid Mechanics, 2nd ed., Addison-Wesley, Don Mills, Ontario, 1992, ch. 8.
E. Khalil:Modelling of Furnaces and Combustors, Abacus Press, Tunbridge Wells, Kent, England, 1982, ch. 3.
I. Ryhming:Dynamique des Fluides, Presses Polytechniques Romandes, Lausanne, Switzerland, 1982, ch. 6.
D.J. Lloyd:Compos. Sci. Technol., 1989, vol. 35, pp. 159–79.
R.M. German:Liquid Phase Sintering, Plenum Press, New York, NY, 1985, ch. 3.
J.F. Richardson and W.N. Zaki:Chem. Eng. Sci., 1954, vol. 3, pp. 65–70.
A. Fortier:Mécanique des Suspensions, Masson et Cie, Paris, 1967, ch. 3.
K. Pericleous and M. Patel:Phys. Chem. Hydrodyn., 1987, vol. 9 (12), pp. 279–97. $
Author information
Authors and Affiliations
Rights and permissions
About this article
Cite this article
Bui, R.T., Ouellet, R. & Kocaefe, D. A two-phase flow model of the stirring of Al-SiC composite melt. Metall Mater Trans B 25, 607–618 (1994). https://doi.org/10.1007/BF02650081
Received:
Issue Date:
DOI: https://doi.org/10.1007/BF02650081