Simulation of Nanofluid Flow in a Micro-Heat Sink With Corrugated Walls Considering the Effect of Nanoparticle Diameter on Heat Sink Efficiency
- 1Mechanical Engineering Department, Faculty of Engineering, King Abdulaziz University, Jeddah, Saudi Arabia
- 2Center Excellence of Renewable Energy and Power, King Abdulaziz University, Jeddah, Saudi Arabia
- 3Department of Chemistry, College of Science, Taif University, Taif, Saudi Arabia
- 4Independent Researcher, Braunschweig, Germany
- 5Department of Nutrition, Cihan University-Erbil, Erbil, Iraq
- 6Department of Phytochemistry, SRC, Soran University, Soran, Iraq
- 7Department of Mechanical and Aeronautical Engineering, University of Pretoria, Pretoria, South Africa
- 8Department of Medical Research, China Medical University Hospital, China Medical University, Taichung, Taiwan
In this numerical work, the cooling performance of water–Al2O3 nanofluid (NF) in a novel microchannel heat sink with wavy walls (WMH-S) is investigated. The focus of this article is on the effect of NP diameter on the cooling efficiency of the heat sink. The heat sink has four inlets and four outlets, and it receives a constant heat flux from the bottom. CATIA and CAMSOL software were used to design the model and simulate the NF flow and heat transfer, respectively. The effects of the Reynolds number (
Introduction
Advances in technology and electronic devices have posed a formidable challenge for related industries. Increasing the power of electronic devices in many cases causes them to heat up; in some cases it reduces the performance of the devices and, in certain circumstances, causes the electronic devices to fail. Hence, it is of absolute necessity to cool this equipment properly. The application of electronic equipment in devices such as cellphones and tablets in a small space has caused heat transfer to occur in a tiny space. CPUs are one of these electronic devices and cooling them is required in all of the abovementioned devices. As their computing power enhances, the generated heat increases, and as a result, they need to be cooled down by heat sinks (H-Ss) to prevent the reduction in their performance (Ghani et al., 2017; Sohel Murshed and Nieto de Castro, 2017; Bahiraei and Heshmatian, 2018a; Ahmed et al., 2018; Pordanjani et al., 2021). Owing to the tiny size of the CPUs, it is necessary to employ micro-heat sinks (MH-Ss) in this regard. In MH-Ss, the fluid flows in the microchannels and cools the H-S and consequently the electronic equipment. The growing needs of industries for MH-Ss with increased cooling capacities has led to an increment in studies in recent decades (Tullius et al., 2011; Shalchi–Tabrizi and Seyf, 2012; Mohammed Adham et al., 2013; Sohel et al., 2015; Kumar et al., 2018). So far, particularly in recent years, several researchers have conducted various studies on the analysis of cooling devices (Bagherzadeh et al., 2019; Ahmadi et al., 2020a; Peng et al., 2020; Shadloo et al., 2020; Safdari Shadloo, 2021). In one of these studies, Kumar and Singh (2019) numerically inspected the influence of inlet and outlet on the thermal performance of an H-S. They studied an H-S comprising some parallel microchannels and utilized
In general, researchers have used both numerical and experimental methods for their studies in the field of fluid mechanics (Kalbasi et al., 2019; Guan et al., 2020; Hu et al., 2020; Giwa et al., 2021; Hu et al., 2021). The use of experimental methods is reliable, but costly. In many numerical studies, validation has been done by the comparison of the numerical results with experimental data, and as a result, experimental work has been expanded (Esfe et al., 2018; Hemmat Esfe et al., 2018; Bahrami et al., 2019; Pordanjani et al., 2019; Zheng et al., 2020). Numerical research is less expensive than laboratory work and can be done in less time (Afrand et al., 2014; Osman et al., 2019; Ahmadi et al., 2020b; Sokhal et al., 2021).
In a myriad of conducted studies, NFs have been used to cool down different types of heat devices (Aybar et al., 2015; Ghodsinezhad et al., 2016; Sharifpur et al., 2016; Awais and Kim, 2020; Irandoost Shahrestani et al., 2020). NFs exhibit higher thermal conductivity than simple fluids (Toghyani et al., 2019; Vahedi et al., 2019; Ghalandari et al., 2020; Yan et al., 2020; Pordanjani and Aghakhani, 2021). Numerous articles have recommended the application of nanotechnology in the industry (Hajatzadeh Pordanjani et al., 2019; Zhang et al., 2020; Handschuh–Wang et al., 2021; Tian et al., 2021; Wang et al., 2021). In this regard, studies by Ambreen and Kim (2020), Wu et al. (2016), Alfaryjat et al. (2018), and Arani et al. (2017) can be referred. In one of these research studies, Bahiraei and Heshmatian (2018b) examined the influence of the presence of hybrid NFs on the performance of a rectangular H-S. They examined a heat sink comprising four similar sections, each containing five microchannels ,and a fixed thermal flux of 100 W/cm2 applied on the bottom of the H-S. Their simulation results demonstrated that increasing the NF velocity from 1 to 3 m/s decreased the
Nanoparticles (NPs) can be made in different dimensions in nanoscale. Many NPs have different dimensions. Alumina NPs, one of the most widely used NPs, are produced in various dimensions. The dimensions of the NPs can affect the thermal conductivity and viscosity of the NF. However, few researchers have considered the effect of the NP diameter on heat transfer, especially in heat sinks. Owing to the importance of cooling electronic devices, particularly CPUs in various functional devices, this article numerically studied a new H-S. This H-S had four similar sections where the fluid entered through 4 inlets and exited out of 4 outlets. In order to improve heat transfer, NFs were employed for cooling, and microchannels with wavy walls (WW) were also considered. The model used for single-phase viscosity and thermal conductivity also depended on the diameter of the nanoparticles (NPs),and its influence on the thermal performance of the WW in H-S has also been investigated. An innovation of this study is to use wavy channel walls in the heat sink and to assess the effect of the nanoparticle diameter on the thermal efficiency of a heat sink .
Problem Definition
The studied WMH-S, presented in Figure 1, had four inlets and four outlets. This aluminum WMH-S comprised of four similar sections. The height of the WMH-S was 0.5 mm and its overall dimension was 18 × 6.2 mm. The dimensions of the heat sink inlet are 1.8 mm, and the height of microchannels is 0.4 mm. A 0.2-mm-thick aluminum door is placed on the heat sink. Within the WMH-S, nanomaterials,
Governing Equations
The general equations governing the fluid flow within the H-S in the single-phase form are as follows. These equations include the conservation of mass, momentum, and energy. The fluid flow is laminar and steady, and the fluid is an incompressible Newtonian (Akbari et al., 2011).
where
In the above-mentioned equations, the indices p and f refer to the NPs and the base fluid, respectively. The NF viscosity was calculated using the following equation, which is specific to the
where
where
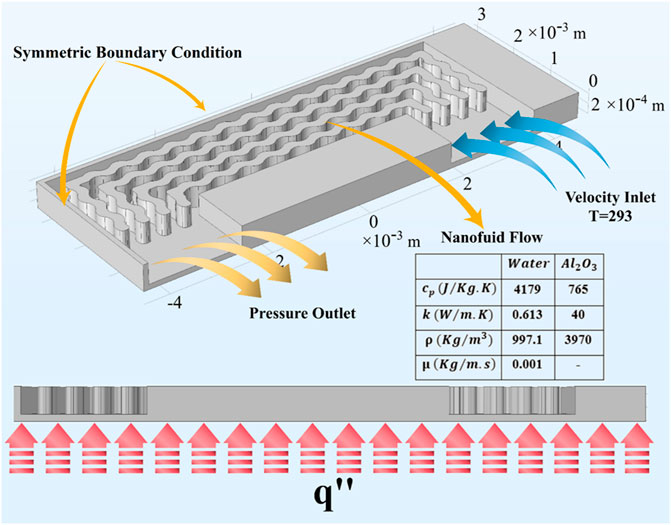
FIGURE 2. Boundary conditions applied to the problem geometry and thermophysical properties of
Boundary Conditions
Figure 3 shows the boundary condition of the problem. The temperature values and boundary conditions at the inlet and outlet of the heat sink are displayed in Figure 2. The properties of water and NPs are also present in this figure. A constant flux of 100 W/cm2 is applied to the bottom of the heat sink as shown. According to Figure 2, the upper, front, and left walls of the heat sink are insulated, and the symmetry boundary condition is applied to the back and right walls.
Numerical Method and Validation
For simulating the problem model, its geometry was first drawn in CATIA software. In the next step, the mentioned geometry was transferred to CAMSOL software. Next, an all-hexagonal mesh was applied to the geometry. Then, by entering the properties of NFs and other boundary conditions in this software, the equations were solved and the necessary simulations were performed using the finite element method. The convergence criterion for Eqs 7–10 is considered. To achieve a proper grid for geometry, many changes were made to the number of elements. Finally it was found that these yield the best results in terms of the solution time as well as the accuracy of the results for the number of 1,550,000 elements. The average temperature changes of the heat sink for the number of different elements are given in Table 1 in the Re = 300 for 5% nanofluid. The trend of the changes in the heat sink average temperature shows the accuracy of selecting this number of elements.
In order to validate the numerical solution, the results of the present study were compared with some articles, one of which is provided below. Thus, the average Nusselt number obtained from the present work is compared with the experimental work of Ho and Chen (2013) for different channel lengths (Table 2). It can be observed that the amount of error between the present results and those reported by Ho and Chen (2013) is less than 4%, indicating that the present simulations are acceptable.
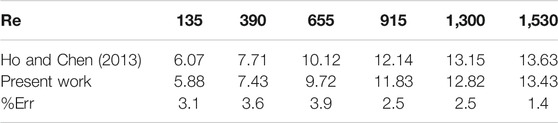
TABLE 2. Average Nusselt number along the channel for the present work and Ho and Chen (2013).
Data Reduction
To assess the thermal performance of the H-S, it was of necessity to investigate parameters such as the heat transfer coefficient (HTC) and the pumping power PP. The convective HTC for the H-S was defined as follows (Bahiraei and Heshmatian, 2017).
In the following relations, two increased ratios of HTC and PP are introduced.
In the PP relation,
Other parameters can also be utilized to measure the thermal performance of H-Ss. Two important parameters in evaluating the performance of H-Ss are the thermal resistance and temperature uniformity, the relationships of which are listed below. The lower the two parameters, the better the performance of H-Ss.
In the above equations, the indices Max and Min represent the maximum and minimum temperatures on the lower surface of the H-S.
A parameter that is considered when using NFs in various devices is the figure of merit (FOM), whose relationship is presented below, indicates the ratio of convective HTC of NF to
Results and Discussion
Figure 3 demonstrated the temperature contour of the WMH-S for
Figure 4 shows the
Figure 5 displays the average temperature of the bottom of the H-S for variations of Re, d, and Fi. As it can also be observed, an intensification in the Re diminished the average temperature in the WMH-S and an intensification in the Fi decreased the average temperature. As mentioned above, the increase in these two parameters increased the heat transfer between the WMH-S and the fluid, thus reducing the overall temperature of WMH-S and making its temperature closer to the temperature of the fluid. The changes in the average temperature varied based on the changes in the NP diameter at different volume percentages. Of course, the amount of these changes was far less than the temperature changes with the Fi and Re. The average temperature appeared to be lower in medium-sized NPs, especially at high volumetric percentages.
Figure 6 demonstrated the PP required to flow the fluid for dissimilar values of Re, d, and Fi. The intensification in Re and, consequently, the escalation in fluid velocity greatly increased the PP. Increasing the
Figure 7 demonstrates the increase percentage in the HTC for different values of Re, d, and Fi. Increasing the Re and the Fi always increased the HTC. It was seen that growing the Fi maintained the upward trend of increasing the HTC and always increased it. However, with the intensification of the Re in the high volume percentages of NPs, the increase in the HTC was initially low, but in higher Re, the increasing trend was steeper and increased significantly; while in the low Fi, the increase in the Re always created an increasing trend in the HTC. It was also noticed that in high and low Re, the effect of adding NPs was more promising than that in medium Re. Furthermore, the increase in the HTC was higher for the average-sized NPs.
Figure 8 demonstrates the temperature uniformity on the bottom of the WMH-S for dissimilar values of Re, d, and Fi. Here, the intensification in the Re and the volumetric percentage of the NPs reduced the Theta, indicating that the temperature at the bottom of the WMH-S was uniform. The decrease in temperature caused the temperature to be uniform in this part, stemming from better heat transfer between the fluid and the solid walls. In the average diameters of NPs, Theta was higher, meaning that the larger diameter of NPs had better temperature uniformity.
Figure 9 shows the FOM for dissimilar values of Re, d, and Fi. The best case for adding NPs in terms of heat transfer to
Conclusion
In this article, a new WMH-S with five microchannels was simulated. The walls of the microchannels were wavy.
1) Increasing the Re and the percentage of NPs reduced the maximum and minimum temperatures at the bottom of the WMH-S.
2) Increasing the diameter of the NPs at a higher Fi increased the
3) With increasing the Re and volume percentage, more PP was required. Thus, the cost of PP also increases.
4) In high percentages of NPs, the increase in the size of NPs also raised the PP.
5) The HTC augmented with increasing Re and Fi.
6) The temperature uniformity increased with the intensification of Re and the volumetric percentage of NPs, and its thermal resistance decreased.
7) The highest FOM was approximately 1.25, occurring in high Res and volume percentages of NPs.
Data Availability Statement
The original contributions presented in the study are included in the article/Supplementary Material, further inquiries can be directed to the corresponding authors.
Author Contributions
All authors wrote the manuscript, provided critical feedback, and helped shape the research, analysis, and manuscript. All authors discussed the results and commented on the manuscript.
Funding
This work was supported by the Taif University Researchers Supporting grant number (TURSP-2020/266) of Taif University, Taif, Saudi Arabia.
Conflict of Interest
The authors declare that the research was conducted in the absence of any commercial or financial relationships that could be construed as a potential conflict of interest.
Publisher’s Note
All claims expressed in this article are solely those of the authors and do not necessarily represent those of their affiliated organizations, or those of the publisher, the editors and the reviewers. Any product that may be evaluated in this article, or claim that may be made by its manufacturer, is not guaranteed or endorsed by the publisher.
References
Afrand, M., Farahat, S., Nezhad, A. H., Ali Sheikhzadeh, G., and Sarhaddi, F. (2014). 3-D Numerical Investigation of Natural Convection in a Tilted Cylindrical Annulus Containing Molten Potassium and Controlling it Using Various Magnetic fields. Int. J. Appl. Electromagnetics Mech. 46, 809–821. doi:10.3233/jae-141975
Ahmadi, A., Arabbeiki, M., Ali, H. M., Goodarzi, M., and Safaei, M. R. (2020). Configuration and Optimization of a Minichannel Using Water–Alumina Nanofluid by Non-dominated Sorting Genetic Algorithm and Response Surface Method. Nanomaterials (Basel) 10 (5), 901. doi:10.3390/nano10050901
Ahmadi, M. H., Mohseni-Gharyehsafa, B., Ghazvini, M., Goodarzi, M., Jilte, R. D., and Kumar, R. (2020). Comparing Various Machine Learning Approaches in Modeling the Dynamic Viscosity of CuO/water Nanofluid. J. Therm. Anal. Calorim. 139 (4), 2585–2599. doi:10.1007/s10973-019-08762-z
Ahmed, H. E., Salman, B. H., Kherbeet, A. S., and Ahmed, M. I. (2018). Optimization of thermal Design of Heat Sinks: A Review. Int. J. Heat Mass Transfer 118, 129–153. doi:10.1016/j.ijheatmasstransfer.2017.10.099
Akbari, M., Galanis, N., and Behzadmehr, A. (2011). Comparative Analysis of Single and Two-phase Models for CFD Studies of Nanofluid Heat Transfer. Int. J. Therm. Sci. 50 (8), 1343–1354. doi:10.1016/j.ijthermalsci.2011.03.008
Alfaryjat, A. A., Mohammed, H. A., Adam, N. M., Stanciu, D., and Dobrovicescu, A. (2018). Numerical Investigation of Heat Transfer Enhancement Using Various Nanofluids in Hexagonal Microchannel Heat Sink. Therm. Sci. Eng. Prog. 5, 252–262. doi:10.1016/j.tsep.2017.12.003
Alihosseini, Y., Zabetian Targhi, M., Heyhat, M. M., and Ghorbani, N. (2020). Effect of a Micro Heat Sink Geometric Design on Thermo-Hydraulic Performance: A Review. Appl. Therm. Eng. 170, 114974. doi:10.1016/j.applthermaleng.2020.114974
Ambreen, T., and Kim, M.-H. (2020). Influence of Particle Size on the Effective thermal Conductivity of Nanofluids: A Critical Review. Appl. Energ. 264, 114684. doi:10.1016/j.apenergy.2020.114684
Arani, A. A. A., Sadripour, S., and Kermani, S. (2017). Nanoparticle Shape Effects on thermal-hydraulic Performance of Boehmite Alumina Nanofluids in a Sinusoidal-Wavy Mini-Channel with Phase Shift and Variable Wavelength. Int. J. Mech. Sci. 128-129, 550–563. doi:10.1016/j.ijmecsci.2017.05.030
Awais, A. A., and Kim, M.-H. (2020). Experimental and Numerical Study on the Performance of a Minichannel Heat Sink with Different Header Geometries Using Nanofluids. Appl. Therm. Eng. 171, 115125. doi:10.1016/j.applthermaleng.2020.115125
Aybar, H. Ş., Sharifpur, M., Azizian, M. R., Mehrabi, M., and Meyer, J. P. (2015). A Review of Thermal Conductivity Models for Nanofluids. Heat Transfer Eng. 36 (13), 1085–1110. doi:10.1080/01457632.2015.987586
Bagherzadeh, S. A., D’Orazio, A., Karimipour, A., Goodarzi, M., and Bach, Q.-V. (2019). A Novel Sensitivity Analysis Model of EANN for F-MWCNTs-Fe3O4/EG Nanofluid thermal Conductivity: Outputs Predicted Analytically Instead of Numerically to More Accuracy and Less Costs. Physica A: Stat. Mech. its Appl. 521, 406–415. doi:10.1016/j.physa.2019.01.048
Bahiraei, M., and Heshmatian, S. (2017). Application of a Novel Biological Nanofluid in a Liquid Block Heat Sink for Cooling of an Electronic Processor: Thermal Performance and Irreversibility Considerations. Energ. Convers. Manage. 149, 155–167. doi:10.1016/j.enconman.2017.07.020
Bahiraei, M., and Heshmatian, S. (2018). Electronics Cooling with Nanofluids: A Critical Review. Energ. Convers. Manage. 172, 438–456. doi:10.1016/j.enconman.2018.07.047
Bahiraei, M., and Heshmatian, S. (2018). Thermal Performance and Second Law Characteristics of Two New Microchannel Heat Sinks Operated with Hybrid Nanofluid Containing Graphene-Silver Nanoparticles. Energ. Convers. Manage. 168, 357–370. doi:10.1016/j.enconman.2018.05.020
Bahrami, M., Akbari, M., Bagherzadeh, S. A., Karimipour, A., Afrand, M., and Goodarzi, M. (2019). Develop 24 Dissimilar ANNs by Suitable Architectures & Training Algorithms via Sensitivity Analysis to Better Statistical Presentation: Measure MSEs between Targets & ANN for Fe-CuO/Eg-Water Nanofluid. Physica A: Stat. Mech. its Appl. 519, 159–168. doi:10.1016/j.physa.2018.12.031
Esfe, M. H., Esfandeh, S., Afrand, M., Rejvani, M., and Rostamian, S. H. (2018). Experimental Evaluation, New Correlation Proposing and ANN Modeling of thermal Properties of EG Based Hybrid Nanofluid Containing ZnO-DWCNT Nanoparticles for Internal Combustion Engines Applications. Appl. Therm. Eng. 133, 452–463. doi:10.1016/j.applthermaleng.2017.11.131
Ghalandari, M., Maleki, A., Haghighi, A., Safdari Shadloo, M., Alhuyi Nazari, M., and Tlili, I. (2020). Applications of Nanofluids Containing Carbon Nanotubes in Solar Energy Systems: A Review. J. Mol. Liquids 313, 113476. doi:10.1016/j.molliq.2020.113476
Ghani, I. A., Sidik, N. A. C., and Kamaruzaman, N. (2017). Hydrothermal Performance of Microchannel Heat Sink: The Effect of Channel Design. Int. J. Heat Mass Transfer 107, 21–44. doi:10.1016/j.ijheatmasstransfer.2016.11.031
Ghodsinezhad, H., Sharifpur, M., and Meyer, J. P. (2016). Experimental Investigation on Cavity Flow Natural Convection of Al 2 O 3 -water Nanofluids. Int. Commun. Heat Mass Transfer 76, 316–324. doi:10.1016/j.icheatmasstransfer.2016.06.005
Giwa, S. O., Sharifpur, M., Goodarzi, M., Alsulami, H., and Meyer, J. P. (2021). Influence of Base Fluid, Temperature, and Concentration on the Thermophysical Properties of Hybrid Nanofluids of Alumina–Ferrofluid: Experimental Data, Modeling through Enhanced ANN, ANFIS, and Curve Fitting. J. Therm. Anal. Calorim. 143 (6), 4149–4167. doi:10.1007/s10973-020-09372-w
Guan, H., Huang, S., Ding, J., Tian, F., Xu, Q., and Zhao, J. (2020). Chemical Environment and Magnetic Moment Effects on point Defect Formations in CoCrNi-Based Concentrated Solid-Solution Alloys. Acta Materialia 187, 122–134. doi:10.1016/j.actamat.2020.01.044
Hajatzadeh Pordanjani, A., Aghakhani, S., Afrand, M., Mahmoudi, B., Mahian, O., and Wongwises, S. (2019). An Updated Review on Application of Nanofluids in Heat Exchangers for Saving Energy. Energ. Convers. Manage. 198, 111886. doi:10.1016/j.enconman.2019.111886
Handschuh-Wang, S., Wang, T., and Tang, Y. (2021). Ultrathin Diamond Nanofilms—Development, Challenges, and Applications. Small 17 (30), 2007529. doi:10.1002/smll.202007529
Hemmat Esfe, M., Rostamian, H., Esfandeh, S., and Afrand, M. (2018). Modeling and Prediction of Rheological Behavior of Al2O3-Mwcnt/5w50 Hybrid Nano-Lubricant by Artificial Neural Network Using Experimental Data. Physica A: Stat. Mech. its Appl. 510, 625–634. doi:10.1016/j.physa.2018.06.041
Ho, C. J., and Chen, W. C. (2013). An Experimental Study on thermal Performance of Al2O3/water Nanofluid in a Minichannel Heat Sink. Appl. Therm. Eng. 50 (1), 516–522. doi:10.1016/j.applthermaleng.2012.07.037
Hu, P., Cao, L., Su, J., Li, Q., and Li, Y. (2020). Distribution Characteristics of Salt-Out Particles in Steam Turbine Stage. Energy 192, 116626. doi:10.1016/j.energy.2019.116626
Hu, Y., Qing, J. x., Liu, Z. H., Conrad, Z. J., Cao, J. N., and Zhang, X. P. (2021). Hovering Efficiency Optimization of the Ducted Propeller with Weight Penalty Taken into Account. Aerospace Sci. Technol. 117, 106937. doi:10.1016/j.ast.2021.106937
Irandoost Shahrestani, M., Maleki, A., Safdari Shadloo, M., and Tlili, I. (2020). Numerical Investigation of Forced Convective Heat Transfer and Performance Evaluation Criterion of Al2O3/Water Nanofluid Flow inside an. Axisymmetric Microchannel 12 (1), 120. doi:10.3390/sym12010120
Kalbasi, R., Afrand, M., Alsarraf, J., and Tran, M.-D. (2019). Studies on Optimum Fins Number in PCM-Based Heat Sinks. Energy 171, 1088–1099. doi:10.1016/j.energy.2019.01.070
Kant, K., Shukla, A., Sharma, A., and Henry Biwole, P. (2017). Heat Transfer Study of Phase Change Materials with Graphene Nano Particle for thermal Energy Storage. Solar Energy 146, 453–463. doi:10.1016/j.solener.2017.03.013
Khanafer, K., and Vafai, K. (2011). A Critical Synthesis of Thermophysical Characteristics of Nanofluids. Int. J. Heat Mass Transfer 54 (19), 4410–4428. doi:10.1016/j.ijheatmasstransfer.2011.04.048
Kumar, S., Kumar, A., Darshan Kothiyal, A., and Singh Bisht, M. (2018). A Review of Flow and Heat Transfer Behaviour of Nanofluids in Micro Channel Heat Sinks. Therm. Sci. Eng. Prog. 8, 477–493. doi:10.1016/j.tsep.2018.10.004
Kumar, S., and Singh, P. K. (2019). A Novel Approach to Manage Temperature Non-uniformity in Minichannel Heat Sink by Using Intentional Flow Maldistribution. Appl. Therm. Eng. 163, 114403. doi:10.1016/j.applthermaleng.2019.114403
Mohammed Adham, A., Mohd-Ghazali, N., and Ahmad, R. (2013). Thermal and Hydrodynamic Analysis of Microchannel Heat Sinks: A Review. Renew. Sustain. Energ. Rev. 21, 614–622. doi:10.1016/j.rser.2013.01.022
Nguyen, T. K., Saidizad, A., Jafaryar, M., Sheikholeslami, M., Barzegar Gerdroodbary, M., Moradi, R., et al. (2019). Influence of Various Shapes of CuO Nanomaterial on Nanofluid Forced Convection within a Sinusoidal Channel with Obstacles. Chem. Eng. Res. Des. 146, 478–485. doi:10.1016/j.cherd.2019.04.030
Osman, S., Sharifpur, M., and Meyer, J. P. (2019). Experimental Investigation of Convection Heat Transfer in the Transition Flow Regime of Aluminium Oxide-Water Nanofluids in a Rectangular Channel. Int. J. Heat Mass Transfer 133, 895–902. doi:10.1016/j.ijheatmasstransfer.2018.12.169
Peng, Y., Parsian, A., Khodadadi, H., Akbari, M., Ghani, K., Goodarzi, M., et al. (2020). Develop Optimal Network Topology of Artificial Neural Network (AONN) to Predict the Hybrid Nanofluids thermal Conductivity According to the Empirical Data of Al2O3 - Cu Nanoparticles Dispersed in Ethylene Glycol. Physica A: Stat. Mech. its Appl. 549, 124015. doi:10.1016/j.physa.2019.124015
Pordanjani, A. H., Aghakhani, S., Afrand, M., Sharifpur, M., Meyer, J. P., Xu, H., et al. (2021). Nanofluids: Physical Phenomena, Applications in thermal Systems and the Environment Effects- a Critical Review. J. Clean. Prod. 320, 128573. doi:10.1016/j.jclepro.2021.128573
Pordanjani, A. H., and Aghakhani, S. (2021). Numerical Investigation of Natural Convection and Irreversibilities between Two Inclined Concentric Cylinders in Presence of Uniform Magnetic Field and Radiation. Heat Transfer Eng. 43 (11), 1–21. doi:10.1080/01457632.2021.1919973
Pordanjani, A. H., Raisi, A., and Ghasemi, B. (2019). Numerical Simulation of the Magnetic Field and Joule Heating Effects on Force Convection Flow through Parallel-Plate Microchannel in the Presence of Viscous Dissipation Effect. Numer. Heat Transfer, A: Appl. 76, 1–18. doi:10.1080/10407782.2019.1642053
Safdari Shadloo, M. (2021). Application of Support Vector Machines for Accurate Prediction of Convection Heat Transfer Coefficient of Nanofluids through Circular Pipes. Int. J. Numer. Methods Heat Fluid Flow 31 (8), 2660–2679. doi:10.1108/hff-09-2020-0555
Shadloo, M. S., Rahmat, A., Karimipour, A., and Wongwises, S. (2020). Estimation of Pressure Drop of Two-phase Flow in Horizontal Long Pipes Using Artificial Neural Networks. J. Energ. Resour. Technol. 142 (11), 112110. doi:10.1115/1.4047593
Shalchi-Tabrizi, A., and Seyf, H. R. (2012). Analysis of Entropy Generation and Convective Heat Transfer of Al2O3 Nanofluid Flow in a Tangential Micro Heat Sink. Int. J. Heat Mass Transfer 55 (15), 4366–4375. doi:10.1016/j.ijheatmasstransfer.2012.04.005
Sharifpur, M., Yousefi, S., and Meyer, J. P. (2016). A New Model for Density of Nanofluids Including Nanolayer. Int. Commun. Heat Mass Transfer 78, 168–174. doi:10.1016/j.icheatmasstransfer.2016.09.010
Sohel, M. R., Saidur, R., Khaleduzzaman, S. S., and Ibrahim, T. A. (2015). Cooling Performance Investigation of Electronics Cooling System Using Al2O3-H2o Nanofluid. Int. Commun. Heat Mass Transfer 65, 89–93. doi:10.1016/j.icheatmasstransfer.2015.04.015
Sohel Murshed, S. M., and Nieto de Castro, C. A. (2017). A Critical Review of Traditional and Emerging Techniques and Fluids for Electronics Cooling. Renew. Sustain. Energ. Rev. 78, 821–833. doi:10.1016/j.rser.2017.04.112
Sokhal, G. S., Dhindsa, G. S., Sokhal, K. S., Ghazvini, M., Sharifpur, M., and Sadeghzadeh, M. (2021). Experimental Investigation of Heat Transfer and Exergy Loss in Heat Exchanger with Air Bubble Injection Technique. J. Therm. Anal. Calorim. 145, 727. doi:10.1007/s10973-020-10192-1
Teng, T.-P., Hung, Y.-H., Teng, T.-C., Mo, H.-E., and Hsu, H.-G. (2010). The Effect of Alumina/water Nanofluid Particle Size on thermal Conductivity. Appl. Therm. Eng. 30 (14), 2213–2218. doi:10.1016/j.applthermaleng.2010.05.036
Tian, M.-W., Rostami, S., Aghakhani, S., Goldanlou, A. S., and Qi, C. (2021). A Techno-Economic Investigation of 2D and 3D Configurations of Fins and Their Effects on Heat Sink Efficiency of MHD Hybrid Nanofluid with Slip and Non-slip Flow. Int. J. Mech. Sci. 189, 105975. doi:10.1016/j.ijmecsci.2020.105975
Toghyani, S., Afshari, E., Baniasadi, E., and Shadloo, M. S. (2019). Energy and Exergy Analyses of a Nanofluid Based Solar Cooling and Hydrogen Production Combined systemEnergy and Exergy Analyses of a Nanofluid Based Solar Cooling and Hydrogen Production Combined System. Renew. Energ. 141, 1013–1025. doi:10.1016/j.renene.2019.04.073
Tullius, J. F., Vajtai, R., and Bayazitoglu, Y. (2011). A Review of Cooling in Microchannels. Heat Transfer Eng. 32 (7-8), 527–541. doi:10.1080/01457632.2010.506390
Vahedi, S. M., Pordanjani, A. H., Raisi, A., and Chamkha, A. J. (2019). Sensitivity Analysis and Optimization of MHD Forced Convection of a Cu-Water Nanofluid Flow Past a Wedge. The Eur. Phys. J. Plus 134 (3), 124. doi:10.1140/epjp/i2019-12537-x
Wang, X., Handschuh‐Wang, S., Xu, Y., Xiang, L., Zhou, Z., Wang, T., et al. (2021). Hierarchical Micro/Nanostructured Diamond Gradient Surface for Controlled Water Transport and Fog Collection. Adv. Mater. Inter. 8 (12), 2100196. doi:10.1002/admi.202100196
Wu, J., Zhao, J., Lei, J., and Liu, B. (2016). Effectiveness of Nanofluid on Improving the Performance of Microchannel Heat Sink. Appl. Therm. Eng. 101, 402–412. doi:10.1016/j.applthermaleng.2016.01.114
Yan, S.-R., Aghakhani, S., and Karimipour, A. (2020). Influence of a Membrane on Nanofluid Heat Transfer and Irreversibilities inside a Cavity with Two Constant-Temperature Semicircular Sources on the Lower wall: Applicable to Solar Collectors. Physica Scripta 95 (8), 085702. doi:10.1088/1402-4896/ab93e4
Zhang, X., Sun, X., Lv, T., Weng, L., Chi, M., Shi, J., et al. (2020). Preparation of PI Porous Fiber Membrane for Recovering Oil-Article Insulation Structure. J. Mater. Sci. Mater. Electron. 31 (16), 13344–13351. doi:10.1007/s10854-020-03888-5
Keywords: heat sink, electronic component, nanoparticles diameter, alumina–water nanofluid, numerical simulation
Citation: Khetib Y, Abo-Dief HM, Alanazi AK, Cheraghian G, Sajadi SM and Sharifpur M (2021) Simulation of Nanofluid Flow in a Micro-Heat Sink With Corrugated Walls Considering the Effect of Nanoparticle Diameter on Heat Sink Efficiency. Front. Energy Res. 9:769374. doi: 10.3389/fenrg.2021.769374
Received: 01 September 2021; Accepted: 23 September 2021;
Published: 10 November 2021.
Edited by:
Cong Qi, China University of Mining and Technology, ChinaReviewed by:
Basharat Jamil, Rey Juan Carlos University, SpainHossein Nasiri, Brazil University, Brazil
Copyright © 2021 Khetib, Abo-Dief, Alanazi, Cheraghian, Sajadi and Sharifpur. This is an open-access article distributed under the terms of the Creative Commons Attribution License (CC BY). The use, distribution or reproduction in other forums is permitted, provided the original author(s) and the copyright owner(s) are credited and that the original publication in this journal is cited, in accordance with accepted academic practice. No use, distribution or reproduction is permitted which does not comply with these terms.
*Correspondence: Yacine Khetib, ykhetib@yahoo.com; Mohsen Sharifpur, mohsen.sharifpur@up.ac.za