Selective Production of Phenol-Rich Bio-Oil From Corn Straw Waste by Direct Microwave Pyrolysis Without Extra Catalyst
- Guangdong Provincial Key Laboratory of Environmental Pollution Control and Remediation Technology, School of Environmental Science and Engineering, Sun Yat-sen University, Guangzhou, China
We report a sustainable strategy to cleanly address biomass waste with high-value utilization. Phenol-rich bio-oil is selectively produced by direct pyrolysis of biomass waste corn straw (CS) without use of any catalyst in a microwave device. The effects of temperature and power on the yield and composition of pyrolysis products are investigated in detail. Under microwave irradiation, a very fast pyrolysis rate and bio-oil yield as high as 46.7 wt.% were obtained, which were competitive with most of the previous results. GC-MS analysis showed that temperature and power (heating rate) had great influences on the yield of bio-oil and the selectivity of phenolic compounds. The optimal selectivity of phenols in bio-oil was 49.4 area% by adjusting the operating parameters. Besides, we have made detailed statistics on the change trend of some components and different phenols in bio-oil and given the law and reason of their change with temperature and power. The in situ formed highly active biochar from CS with high content of potassium (1.34 wt.%) is responsible for the improvement of phenol-rich oils. This study offers a sustainable way to fully utilize biomass waste and promote the achievement of carbon neutrality.
Introduction
In China, corn straw (CS) is the most abundant biomass waste, and its annual output has exceeded 216 million tons (Li et al., 2016a). How to valuably utilize this CS waste with minimum effect on the environment is crucial for peak carbon dioxide emissions before 2030 and achieving carbon neutrality before 2060. The conversion of biomass to high-value–added chemicals has attracted growing attention (Yi et al., 2020; Zhang et al., 2020). So far, gasification, pyrolysis, and liquefaction methods have been developed to deal with biomass waste (Hildebrandt et al., 2009; Vispute et al., 2010). However, biomass gasification is limited by high cost and low efficiency (Díaz González and Pacheco Sandoval, 2020). Furthermore, the liquid fuel from biomass liquefaction with low calorific value and more complex chemical composition needs further separation (Pang, 2019). Pyrolysis technology has been extensively exploited because it can convert biomass wastes from agricultural and forestry industry into liquid fuels (also called bio-oil) with wide adaptability (Liu et al., 2020; Al-Harahsheh et al., 2021; Hoang Pham et al., 2021). A number of highly valuable products can be separated from bio-oil. Among them, phenols in bio-oil are more environmentally friendly and have the potential to replace the phenolic compounds from the petroleum industry. Besides, they can be used as part of the phenolic resin instead of adhesive, disinfectant, developer, and so on.
Over the past few decades, efforts have been made to develop technologies for efficient pyrolysis of biomass and high product utilization systems (Durak, 2015; Durak, 2016; Durak et al., 2019). Microwave-assisted pyrolysis (MAP) with unique heating property is considered to be a very attractive technology for the production of high-value–added chemicals from biological residues (Pianroj et al., 2016; Bundhoo, 2018). Compared with traditional pyrolysis methods, MAP technology has some excellent properties, including fast heating rate (Borges et al., 2014), high yield of production, low oxygen content of bio-oil (Ferrera-Lorenzo et al., 2014a; Ravikumar et al., 2017), and volumetric heating (Mašek et al., 2013). Moreover, MAP can produce high-performance syngas, bio-oil (Kostas et al., 2020; Yu et al., 2020), and biochar (coal char) (Li et al., 2016b; Parvez et al., 2019). However, the bio-oil obtained by MAP of CS still contains considerable oxygen content (29.5 wt.%), which will inevitably lead to the generation of organic compounds with high oxygen contained in the pyrolysis organisms, among which phenols are the representative (Ferrera-Lorenzo et al., 2014b). For example, Dai et al. (Dai et al., 2020) prepared phenol-rich bio-oil by catalytic pyrolysis of corn cob with supported catalyst containing iron, and the phenol content reached 49.7 area% and the yield of bio-oil was 26.9 wt.%. By adjusting the composition of the catalyst and the reaction conditions, the selectivity reached 91.1 area%. Idris et al. (Idris et al., 2021) reported that the total phenolic compounds were 73.6 area% at low pyrolysis temperature (300°C) using activated carbon as a catalyst, but the yield of bio-oil was only 30.0 wt.%. Alisa et al. (Mamaeva et al., 2016) used activated carbon as a catalyst to convert raw biomass through MAP. By adjusting the proportion of catalysts and biomass and cracking conditions, the selectivity of total phenols reached 61.2 area% at 300°C, but the yield of bio-oil was less than 15.0 wt.%. Similarly, Joy et al. (Omoriyekomwan et al., 2016) used activated carbon for producing bio-oils from raw biomass materials. The selectivity of phenols reached 71.3 area%, and the conversion of bio-oil reached 36.8 wt.%. Albeit the previous works have made great progress, the following challenges are still faced: 1) extra catalyst is associated with the cost and the environmental issue in the synthesis; 2) the selectivity of phenols and yield of bio-oil failed to increase at the same time; and 3) the catalytic effect of biochar produced by microwave pyrolysis and alkali metal from biomass is often ignored.
In this work, we report the selective and green synthesis of phenol-rich bio-oils from CS waste by rapid pyrolysis without extra catalyst. This study will exhibit the following unique features: 1) No catalyst is used, avoiding the cost and the associated environmental issues in using organic solvents. 2) The in situ generated biochar formed in the process of pyrolysis and the alkali metal of biomass-self are found to play a crucial role in product distribution. 3) Through a series of characterization and adjustment of process parameters, the yields and selectivity of bio-oils are analyzed in detail. This work may offer a new way to clean processing of biomass waste.
Experimental Section
Raw Materials
The grain size of corn straw treated in Donghai County of Jiangsu Province in China ranged from 20 to 30 mesh. In each experiment, dichloromethane was mainly from Macklin Company with the purity of 99.5%. The microwave device was purchased from Changyi Microwave Company.
Microwave Setup
The microwave pyrolysis experiment was carried out on a self-designed microwave device platform, as shown in Figure 1. The microwave device mainly consists of four parts: 1) the ventilation part is mainly composed of a nitrogen cylinder and cylinder valve; 2) the pyrolysis part is mainly completed in a microwave instrument, so it is mainly composed of a crucible (specific for microwave heating) and its surrounding semi-closed system; 3) the collection part is mainly composed of a bio-oil collection bottle and condensing tube; and 4) the gas collection part contains the air bag to collect the generated gas and GC analysis facility.
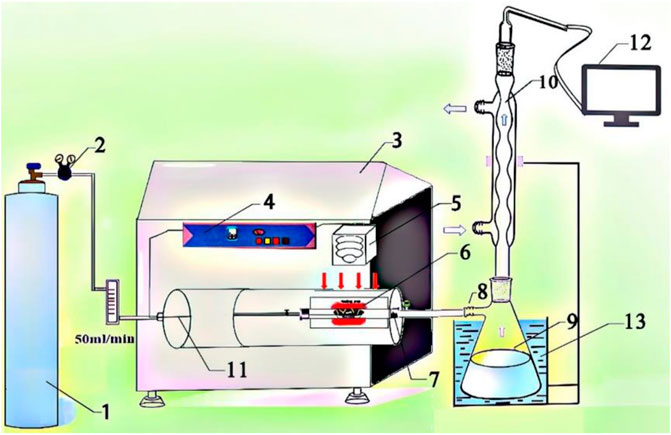
FIGURE 1. Schematic diagram of the microwave-assisted pyrolysis setup: (1) nitrogen cylinder; (2) cylinder valve; (3) microwave reaction equipment; (4) control panel; (5) thermocouple; (6) crucible (specific for microwave heating); (7) thermal insulation position; (8) rubber tube; (9) bio-oil collection bottle; (10) condensing tube; (11) temperature probe; (12) gas chromatograph; (13) cooling water.
The first part is the carrier gas, the gas used in this work is high-purity nitrogen, and the ventilation rate is adjusted according to different purposes. The second part is pyrolysis reaction, which is mainly composed of a reaction device and raw materials. The reaction device here is mainly composed of a crucible (specific for microwave heating) and the surrounding semi-closed space. This is because the condensable gas produced by cracking reaction will have secondary cracking reaction in the surrounding semi-closed system, so the reaction part should be the whole quartz tube. The third part is the cooling device, which is mainly composed of three parts: the electric heating device in the microwave instrument, the condensing tube, and the water bath beaker. Condensation is an essential part of the pyrolysis reaction unit. Its condensation mode and condensation temperature have great influence on the yield and composition of bio-oil. The first-stage condensing device in this experiment is at thermal insulation position in the microwave equipment shown in Figure 1. The temperature of this position is controlled by a control panel. We set the temperature of heat preservation at 200°C. The secondary condensing device is the conventional condensation of tap water on the condensing tube and the water bath condensation formed by the conical flask and the beaker filled with water. We add dichloromethane into the conical flask in advance to facilitate the absorption of volatile matter. The condensation device and condensation temperature in the laboratory are universal, which have guiding significance for industrial production and other scientific research work. Too high or too low condensation temperature will lead to insufficient utilization of biomass pyrolysis resources. Therefore, we adopt a self-designed condensation mode to collect phenol-rich bio-oil, which provides the basis for other related work.
MAP Experiments
CS (1.50 ± 0.05 g) was placed in a crucible that is specially made for microwave heating to absorb microwaves. The crucible was put into a quartz tube, where it was pushed to the middle position. When the reaction temperature was below 150°C, the ventilation rate was set as 150 ml/min. It then reduced to 50 ml/min when increasing the temperature above 150°C. Taking 100°C as the interval and 400, 500, 600, and 700°C as the reaction conditions, the effects of temperature on the yield and different components of bio-oil were studied. When doing the experiment of temperature influencing factors, we set the power to the maximum of 1300 W, raise it to the target temperature at the fastest rate, and keep it for 20 min, so as to reduce the influence of power on temperature. Under the reaction conditions of 600, 800, 1000, and 1200 W, the effect of power on the yield and composition of bio-oil was explored, and each experiment lasted for 20 min. The reaction time is determined according to the principle that there is no phenomenon at the end of pyrolysis reaction.
After the pyrolysis reaction is completed, there is a small amount of water in the connection between the reaction device and the cooling device, and part of the bio-oil is found in the six places in Figure 1. The specific value of the residue was calculated by weighing the mass of the device (6, 7, 8, and 9) before and after the reaction, and the error was within ±1%. Finally, we explored the composition and distribution of bio-oil in the quartz wall around the crucible, thermal insulation position, rubber tube, and bio-oil collection bottle, especially in the analysis of bio-oil in the rubber tube and bio-oil collection bottle. The yield of pyrolysis products was obtained by the following formulas:
where Ybio-oil represents the yield of bio-oil, Ybiochar represents the yield of biochar, and Ygas represents the yield of syngas.
Measurement and Analysis
The metal elements of corn straw before and after pyrolysis were detected on an Agilent 5000 inductively coupled plasma-optical emission spectrometer (ICP-OES), and the chlorine elements were detected by a halogen analyzer (LC-2010plus). The thermal behavior analysis of CS was studied on an STA449F3 thermal analyzer (Netzsch, Germany) heating from 30 to 800°C with different heating rates. In a typical experiment, about 5 mg CS powder was introduced into the crucible and heated in N2 from 30 to 800°C. N2 was used as a protective gas, and the flow rate was 50 ml/min.
The chemical compositions of bio-oil were detected using a gas chromatography–mass spectrometry system (DSQII, Thermo Fisher, United States) equipped with a TG-5 SilMS capillary column. High-purity (99.999%) helium was used as the carrier gas, and the flow rate was 1 ml/min. The injection size was 0.2 μL with the split ratio of 1:20. The initial temperature of the column temperature chamber was 40°C and maintained for 3 min, which then raised to 320°C at a heating rate of 10°C/min for 5 min. The injection port temperature was 250°C, the ion source temperature was 230°C, and the interface temperature was 280 °C. The scanning range of MS was 19–500°m/z, and the scanning speed was 2009.4. The final results were compared with the National Institute of Standards and Technology (NIST-2.0) mass spectrometry database to identify the compounds in the bio-oil.
Results and Discussion
TG-DTG Analysis of CS
The thermal degradation of corn straw with different heating rates was examined by thermogravimetry (TG), as shown in Figure 2. The related weight loss rate in the TG curves is listed in Table 1. The TG curves can be divided into four stages: 1) The physisorbed water was completely evaporated at 30∼170°C. The total weight loss of the drying stage at 5, 10, 30, and 50°C/min was 3.4 wt.%, 3.5 wt.%, 1.8 wt.%, and 3.7 wt.%, respectively. 2) Hemicellulose and lignin in CS were degraded at 170∼330°C with different heating rates. The weight loss rate of 20.7, 21.0, 24.6, and 26.2 wt.% was achieved at different heating rates of 5, 10, 30, and 50°C/min, respectively, revealing that high heating rate could improve the weight loss in this stage. 3) Cellulose and lignin in CS were degraded at 280∼400°C with different heating rates, and the weight loss in this stage is very obvious. In this stage, the weight loss with different heating rates was relatively stable (about 35 wt.%). The weight loss at different heating rates of 5, 10, 30, and 50°C/min was 38.2, 30.7, 29.0, and 31.5 wt.% (Table 1), respectively. 4) The residue was continuously pyrolyzed at 400∼800°C. In this stage, slow weight loss occurred because of the slow carbonization of residual materials. The above results revealed that high heating rate could improve hemicellulose pyrolysis. The heating rate also affected the results of the total weight loss. The total weight loss corresponding to the four heating rates is 72.2, 64.3, 65.4, and 74.1 wt.%, respectively.
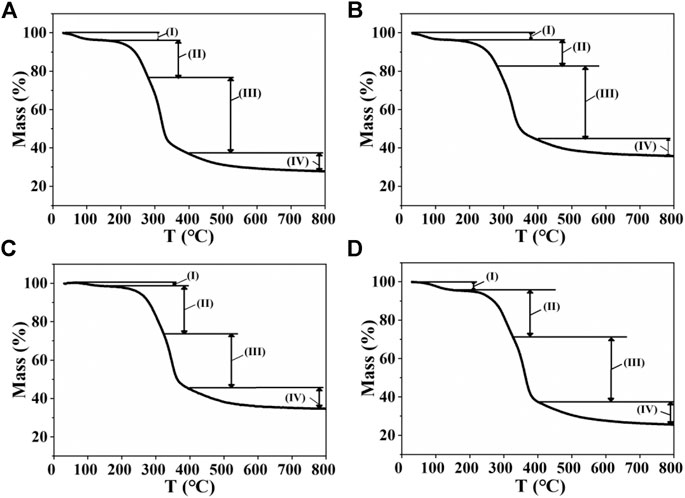
FIGURE 2. Thermogravimetric curves at different heating rates of (A) 5°C/min, (B) 10°C/min, (C) 30°C/min, and (D) 50°C/min.
Figure 3 shows the DTG curves of CS with different heating rates. In particular, the shoulder peaks in the DTG curve at 318∼362°C were assigned to the degradation of hemicellulose, and the sharp peaks at 354∼398°C were caused by the degradation of cellulose. Furthermore, the shoulder peaks and sharp peaks shifted to high temperature with increasing heating rates from 5 to 50°C/min. This may be because a slow heating rate can prolong the residence time of the sample particles, thus promoting the degradation and carbonization of cellulose and hemicellulose at a lower temperature.
Effect of Different Conditions on the Bio-Oil Yield
The yields of three products (bio-oil, biochar, and gas) corresponding to different temperatures and power are shown in Figure 4. The reaction time for CS through MAP at different temperatures is 20 min. With the increase of temperature, the yield of bio-oil increased from 43.8 wt.% at 400°C to a maximum value of 46.7 wt.% at 500°C. In contrast, the yield of syngas decreased from 24.8 to 22.0 wt.% and the yield of biochar basically remained unchanged (about 31 wt.%). Further increasing the reaction temperature from 500 to 700°C, the yields of bio-oil and biochar sharply reduced and the yield of syngas significantly improved. This may be attributed to the further decomposition of the generated bio-oil or biochar, leading to the generation of syngas. Bio-oil was mainly derived from the pyrolysis of cellulose and hemicellulose, while biochar was from lignin (Kumar et al., 2020). Furthermore, the pyrolysis temperatures of the three components in biomass (hemicellulose, cellulose, and lignin) were 200–300°C (Kong et al., 2014), 247–427°C (Ding et al., 2020), and 205–500°C (Chen and Kuo, 2010), respectively. This result showed that increasing temperature is conducive to the pyrolysis reaction and improving the yield of bio-oil at temperatures below 500°C. Further increasing the temperature caused the reduction of bio-oil yield. Therefore, the optimal operation temperature for the generation of bio-oil from CS pyrolysis is 500°C.
The effect of power ranging from 600 to 1200 W on the yield of bio-oil from CS was studied. The reaction time for CS through MAP under different power is 40 min. Similarly, with the increase of power, the yield of bio-oil increases first and then decreases. The maximum yield of bio-oil is around 38.1 wt.% under 800 W, which is lower than that achieved at reaction temperature 500°C. This can be explained by that long reaction time could have resulted in the degradation of the obtained bio-oil. Further increasing the operation power resulted in a lower yield of bio-oil and a higher yield of syngas. This could be because a high power caused a high reaction temperature (above 500°C) and thus reduced the yield of bio-oil.
Effects of Different Conditions on Bio-Oil Components
GC-MS was used to explore the component distribution of bio-oil under different reaction temperatures and power. The distribution of main components in bio-oil obtained by microwave pyrolysis of CS at different temperatures and power is shown in Figure 5. The partial analysis results of the bio-oils are also listed in Tables 2,3. The analysis results of other conditions are shown in the supplementar1111111111y information (Supplementary Tables S1–S6). In addition, the corresponding GC-MS chromatograms under different conditions are shown in Supplementary Figures S1, S2.
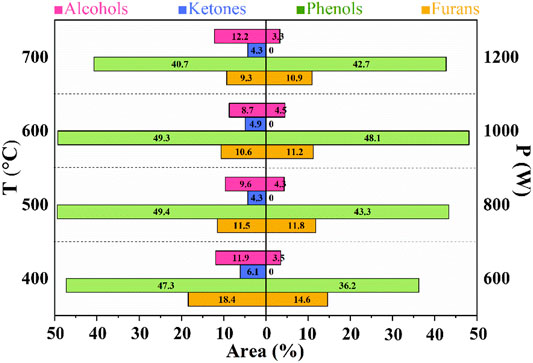
FIGURE 5. Distribution of main components of bio-oil by microwave pyrolysis of CS at different temperatures and power.
Ketones, phenols, acids, alcohols, aldehydes, esters, furans, and hydrocarbons in the bio-oil can be obtained from CS in our work, which is consistent with results from other groups (Kumar et al., 2020; Pang et al., 2020). The effect of temperature on the component in bio-oil was studied. With the increase of temperature, the total phenol content first increased and then decreased. The highest content of phenols was 49.4 area% at 500°C. After 500°C, the content of phenolic compounds decreased, which is consistent with the results reported by Lou et al. (Lou et al., 2010), and the lowest content of phenols was 40.7 area% at 700°C. As we all know, phenols are derived from lignin in CS and the decomposition temperature of lignin is below 500°C. The high content of phenols at 500°C could be explained by that lignin was cracked thoroughly and converted into phenols. Further increasing the temperature (above 500°C) improved the degradation of the obtained phenols and caused a decrease in the phenol content. The result verified that the reaction temperature could make great impacts on the phenol content in the obtained bio-oil. As the reaction temperature increased from 400 to 700°C, the furan content gradually decreased from 18.4 area% to 9.3 area%, indicating that the furans can be converted into other products at a relatively high temperature. The alcohol content first reduced from 11.9 area% at 400°C to 7.3 area% at 600°C and then increased to 12.2 area% at 800°C, confirming that alcohols may be produced from phenols or furans. The ketone content in the whole reaction temperature had basically no change (about 5.4 area%).
Different power from 800 to 1200 W was carried out for the microwave pyrolysis of CS. Similarly, with the increase of power, the yield of phenol content firstly enhanced (below 1000 W) and then decreased (above 1000 W). The highest content of phenols was 48.1 area% under 1000 W. As the reaction power increased from 600 to 1200 W, the furan content gradually decreased from 14.6 area% to 10.9 area%, indicating that the furans can be converted into other products with the increase of power. The content of alcohols at different power basically remained unchanged (about 4 area%), which was lower than that obtained at different temperatures. Furthermore, no ketones can be achieved for CS through MAP under different power. The reaction time at different temperatures (20 min) was less than that under different power (40 min). Therefore, long reaction time could cause degradation of alcohols as well as ketones and decrease their contents.
Effects of Different Conditions on the Content of Phenols
The pathways of lignin decomposition for the production of phenols are generally divided into the following categories: (I) phenol, (II) alkylphenols, (III) alkoxyphenols, (IV) syringol, and (V) guaiacol. Because guaiacol and syringol belong to alkoxyphenols, only three kinds of phenol can be produced from lignin. However, guaiacol and syringol are widely used as research objects because of their wide application range and high added value.
As shown in Figure 6, the relative content of the three phenols was decreased in the following order: alkoxyphenols (including syringol and guaiacol) > alkylphenols > phenol, at different temperatures or power. With the increase of temperature, the relative content of alkoxyphenols first increased to a maximum of 24.5 area% at 600°C and then decreased at 700°C, indicating that a higher temperature leads to the degradation of alkoxyphenols. The relative content of alkylphenols (about 16.4 area%) was unchanged, confirming a well stability of alkylphenols in the temperature range between 400 and 700°C. The relative content of phenol basically stayed invariable (about 8 area%) from 400 to 600°C and then decreased to 3.4 area% at 700°C. With the increase of power, the relative content of alkoxyphenols first increased from 19.9 area% under 600 W to 25.1 area% under 1000 W and then decreased slightly to 23.7 area% under 1200 W. The relative content of alkylphenols first increased to a maximum of 17.3 area% under 1000 W and then decreased. The average content of phenol under different power was about 4.5 area%. The above results revealed that a higher temperature (above 600°C) caused the degradation of alkoxyphenols and phenol and a higher power (above 1000 W) caused the degradation of alkoxyphenols and alkylphenols. The distribution of eugenol, guaiacol, and other alkoxyphenols under different conditions was also analyzed and is shown in Figure 7. The average contents of eugenol and guaiacol were 4.8 area% and 5.1 area% under different temperature conditions and 4.7 area% and 5.6 area% under different power conditions.
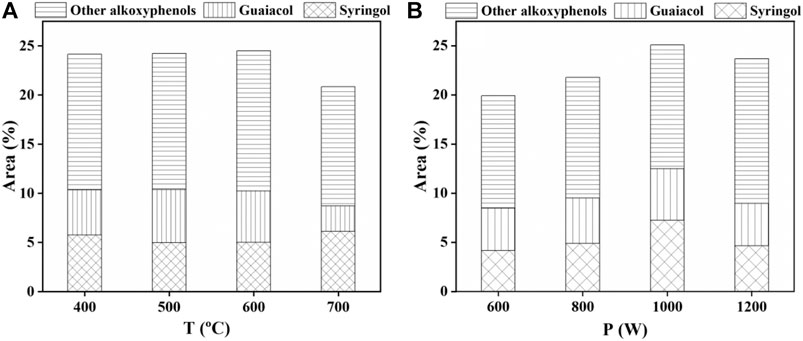
FIGURE 7. Distribution of alkoxyphenols in bio-oil obtained at different (A) temperatures and (B) power.
Comparison of Alkali Metals in the Pyrolysis Process
Alkali metals, alkaline earth metals (Lv et al., 2010), and chlorine (Tang et al., 2014) could significantly improve the bio-oil yield and enhance the phenol selectivity in bio-oil during biomass pyrolysis. Therefore, the metal content of corn straw before and after pyrolysis was determined by the ICP method, and the chlorine content of corn straw before and after pyrolysis was determined by a halogen analyzer. The results are listed in Table 4. It was obvious that the content of K and Cl elements in corn straw is much more than that of other metal elements (Na, Mn, Fe, Ni, and Ce). After pyrolysis, the contents of K and Cl in corn straw increased sharply from 1.34 wt.% and 0.79 wt.% to 4.67 wt.% and 2.82 wt.%, respectively. As a result, the high yield of bio-oil and high selectivity of phenols could possibly be related to the high content of K and Cl.
Compared with the work of other researchers, the selectivity of phenol content in this work is particularly high. The possible reasons are as follows: 1) Cellulose or hemicellulose can promote the pyrolysis of lignin to produce more phenolic compounds (Sun et al., 2020). 2) The microwave device is suitable for the production of phenolic substances because the first-stage condensation temperature of this work is higher. When the first-stage condensation temperature is higher than 100°C, the proportion of the lignin pyrolysis oligomer in bio-oil is increasing (Sui et al., 2014). 3) Biochar formed in the process of microwave pyrolysis worked as an auto-catalyst (microwave absorbent) forming a hot spot effect. These hot spots can generate hydrogen under the action of microwaves (Bu et al., 2013). Hydrogen contributes to the degradation of lignin in CS and promotes the deoxidation of these degraded fragments. After a series of decarboxylation and dehydration, the selectivity of phenolic components is improved. 4) Alkali metals from biomass-self would promote the production of phenol-rich oils.
Conclusion
We have successfully produced phenol-rich bio-oil by the direct pyrolysis process of CS without use of any catalyst in a microwave device. The highest bio-oil yield (46.7 wt.%) was obtained at 500°C, and the highest bio-oil yield was 38.2 wt.% at 800 W. Besides, we have thoroughly explored some characteristic parameters (e.g., pyrolysis temperature and power of microwaves) and analyzed the weight loss rate as well as degree at various stages of different pyrolysis processes. This work offers the following features: 1) We developed a facile procedure for high value utilization of biomass waste without extra catalyst, avoiding the additional cost and environmental issues in the synthesis of the catalyst. 2) Over 46.7 wt.% yield of bio-oil yield at a low temperature of 500°C and 38.2 wt.% yield at 800 W power were obtained, which are the highest values in comparison with those of previous studies. 3) The alkali metal from CS and the in situ generated biochar worked as self-catalysts (microwave absorbents) to enhance the yields of phenols. 4) The effects of different power and temperatures on various kinds of oxygenated organic compounds were studied, and a scheme for producing high yield of bio-oil by microwave pyrolysis without catalyst was provided. The methodology developed in this work may cater for microwave pyrolysis of various biomass wastes to produce phenol-rich bio-oils.
Data Availability Statement
The raw data supporting the conclusions of this article will be made available by the authors, without undue reservation.
Author Contributions
ZZ and ZJ performed the experiment and analysis. HX analyzed the partial samples. KY supervised the work and provided the ideas. ZZ, ZJ, HX, and KY co-wrote this paper.
Funding
This work was supported by the National Key R&D Program of China (2018YFD0800703 and 2020YFC1807600), National Ten Thousand Talent Plan, National Natural Science Foundation of China (22078374, 21776324, and 21905309), Key-Area Research and Development Program of Guangdong Province (2019B110209003), Guangdong Basic and Applied Basic Research Foundation (2019B1515120058 and 2020A1515011149), Fundamental Research Funds for the Central Universities (19lgzd25), and Hundred Talent Plan (201602) from Sun Yat-sen University.
Conflict of Interest
The authors declare that the research was conducted in the absence of any commercial or financial relationships that could be construed as a potential conflict of interest.
Supplementary Material
The Supplementary Material for this article can be found online at: https://www.frontiersin.org/articles/10.3389/fchem.2021.700887/full#supplementary-material
References
Al-Harahsheh, M., Orabi, Y., and Al-Asheh, S. (2021). Comparative study on the pyrolysis and leachability of washed/unwashed electric arc furnace dust-PVC mixtures and their residues. Journal of Environmental Chemical Engineering 9 (4), 105410. doi:10.1016/j.jece.2021.105410
Borges, F. C., Du, Z., Xie, Q., Trierweiler, J. O., Cheng, Y., Wan, Y., et al. (2014). Fast microwave assisted pyrolysis of biomass using microwave absorbent. Bioresource Technology 156, 267–274. doi:10.1016/j.biortech.2014.01.038
Bu, Q., Lei, H., Wang, L., Wei, Y., Zhu, L., Liu, Y., et al. (2013). Renewable phenols production by catalytic microwave pyrolysis of Douglas fir sawdust pellets with activated carbon catalysts. Bioresource Technology 142, 546–552. doi:10.1016/j.biortech.2013.05.073
Bundhoo, Z. M. A. (2018). Microwave-assisted conversion of biomass and waste materials to biofuels. Renewable and Sustainable Energy Reviews 82, 1149–1177. doi:10.1016/j.rser.2017.09.066
Chen, W.-H., and Kuo, P.-C. (2010). A study on torrefaction of various biomass materials and its impact on lignocellulosic structure simulated by a thermogravimetry. Energy 35 (6), 2580–2586. doi:10.1016/j.energy.2010.02.054
Dai, L., Zeng, Z., Yang, Q., Yang, S., Wang, Y., Liu, Y., et al. (2020). Synthesis of iron nanoparticles-based hydrochar catalyst for ex-situ catalytic microwave-assisted pyrolysis of lignocellulosic biomass to renewable phenols. Fuel 279, 118532. doi:10.1016/j.fuel.2020.118532
Díaz González, C. A., and Pacheco Sandoval, L. (2020). Sustainability aspects of biomass gasification systems for small power generation. Renewable and Sustainable Energy Reviews 134, 110180. doi:10.1016/j.rser.2020.110180
Ding, Y., Huang, B., Li, K., Du, W., Lu, K., and Zhang, Y. (2020). Thermal interaction analysis of isolated hemicellulose and cellulose by kinetic parameters during biomass pyrolysis. Energy 195, 117010. doi:10.1016/j.energy.2020.117010
Durak, H. (2015). Thermochemical conversion of Phellinus pomaceus via supercritical fluid extraction and pyrolysis processes. Energy Conversion and Management 99, 282–298. doi:10.1016/j.enconman.2015.04.050
Durak, H. (2016). Pyrolysis ofXanthium strumariumin a fixed bed reactor: Effects of boron catalysts and pyrolysis parameters on product yields and character. Energy Sources, Part A: Recovery, Utilization, and Environmental Effects 38 (10), 1400–1409. doi:10.1080/15567036.2014.947446
Durak, H., Genel, S., and Tunç, M. (2019). Pyrolysis of black cumin seed: Significance of catalyst and temperature product yields and chromatographic characterization. Journal of Liquid Chromatography & Related Technologies 42 (11-12), 331–350. doi:10.1080/10826076.2019.1593194
Ferrera-Lorenzo, N., Fuente, E., Bermúdez, J. M., Suárez-Ruiz, I., and Ruiz, B. (2014a). Conventional and microwave pyrolysis of a macroalgae waste from the Agar-Agar industry. Prospects for bio-fuel production. Bioresource Technology 151, 199–206. doi:10.1016/j.biortech.2013.10.047
Ferrera-Lorenzo, N., Fuente, E., Bermúdez, J. M., Suárez-Ruiz, I., and Ruiz, B. (2014b). Conventional and microwave pyrolysis of a macroalgae waste from the Agar-Agar industry. Prospects for bio-fuel production. Bioresource Technology 151, 199–206. doi:10.1016/j.biortech.2013.10.047
Hildebrandt, D., Glasser, D., Hausberger, B., Patel, B., and Glasser, B. J. (2009). CHEMISTRY: Producing Transportation Fuels with Less Work. Science 323 (5922), 1680–1681. doi:10.1126/science.1168455
Hoang Pham, L. K., Vi Tran, T. T., Kongparakul, S., Reubroycharoen, P., Ding, M., Guan, G., et al. (2021). Data-driven prediction of biomass pyrolysis pathways toward phenolic and aromatic products. Journal of Environmental Chemical Engineering 9 (2), 104836. doi:10.1016/j.jece.2020.104836
Idris, R., Chong, W. W. F., Ali, A., Idris, S., Hasan, M. F., Ani, F. N., et al. (2021). Phenol-rich bio-oil derivation via microwave-induced fast pyrolysis of oil palm empty fruit bunch with activated carbon. Environmental Technology & Innovation 21, 101291. doi:10.1016/j.eti.2020.101291
Kong, S.-H., Loh, S.-K., Bachmann, R. T., Rahim, S. A., and Salimon, J. (2014). Biochar from oil palm biomass: A review of its potential and challenges. Renewable and Sustainable Energy Reviews 39, 729–739. doi:10.1016/j.rser.2014.07.107
Kostas, E. T., Durán-Jiménez, G., Shepherd, B. J., Meredith, W., Stevens, L. A., Williams, O. S. A., et al. (2020). Microwave pyrolysis of olive pomace for bio-oil and bio-char production. Chemical Engineering Journal 387, 123404. doi:10.1016/j.cej.2019.123404
Kumar, R., Strezov, V., Weldekidan, H., He, J., Singh, S., Kan, T., et al. (2020). Lignocellulose biomass pyrolysis for bio-oil production: A review of biomass pre-treatment methods for production of drop-in fuels. Renewable and Sustainable Energy Reviews 123, 109763. doi:10.1016/j.rser.2020.109763
Li, D., Wang, Q., Li, J., Li, Z., Yuan, Y., Yan, Z., et al. (2016a). Mesophilic-hydrothermal-thermophilic (M-H-T) digestion of green corn straw. Bioresource Technology 202, 25–32. doi:10.1016/j.biortech.2015.11.073
Li, J., Dai, J., Liu, G., Zhang, H., Gao, Z., Fu, J., et al. (2016b). Biochar from microwave pyrolysis of biomass: A review. Biomass and Bioenergy 94, 228–244. doi:10.1016/j.biombioe.2016.09.010
Liu, R., Sarker, M., Rahman, M. M., Li, C., Chai, M., Nishu, Cotillon R, et al. (2020). Multi-scale complexities of solid acid catalysts in the catalytic fast pyrolysis of biomass for bio-oil production - A review. Progress in Energy and Combustion Science 80, 100852. doi:10.1016/j.pecs.2020.100852
Lou, R., Wu, S.-b., and Lv, G.-j. (2010). Effect of conditions on fast pyrolysis of bamboo lignin. Journal of Analytical and Applied Pyrolysis 89 (2), 191–196. doi:10.1016/j.jaap.2010.08.007
Lv, D., Xu, M., Liu, X., Zhan, Z., Li, Z., and Yao, H. (2010). Effect of cellulose, lignin, alkali and alkaline earth metallic species on biomass pyrolysis and gasification. Fuel Processing Technology 91 (8), 903–909. doi:10.1016/j.fuproc.2009.09.014
Mamaeva, A., Tahmasebi, A., Tian, L., and Yu, J. (2016). Microwave-assisted catalytic pyrolysis of lignocellulosic biomass for production of phenolic-rich bio-oil. Bioresource Technology 211, 382–389. doi:10.1016/j.biortech.2016.03.120
Mašek, O, Budarin, V, Gronnow, M, Crombie, K, Brownsort, P, Fitzpatrick, E, et al. (2013). Microwave and slow pyrolysis biochar—Comparison of physical and functional properties. J. Anal. Appl. Pyrolysis 100, 41–48. doi:10.1016/j.jaap.2012.11.015
Omoriyekomwan, J. E., Tahmasebi, A., and Yu, J. (2016). Production of phenol-rich bio-oil during catalytic fixed-bed and microwave pyrolysis of palm kernel shell. Bioresource Technology 207, 188–196. doi:10.1016/j.biortech.2016.02.002
Pang, S. (2019). Advances in thermochemical conversion of woody biomass to energy, fuels and chemicals. Biotechnology Advances 37 (4), 589–597. doi:10.1016/j.biotechadv.2018.11.004
Pang, Y. X., Yan, Y., Foo, D. C. Y., Sharmin, N., Zhao, H., Lester, E., et al. (2020). The Influence of Lignocellulose on Biomass Pyrolysis Product Distribution and Economics via Steady State Process Simulation. Journal of Analytical and Applied Pyrolysis, 104968. doi:10.1016/j.jaap.2020.104968104968
Parvez, A. M., Wu, T., Hong, Y., Chen, W., Lester, E. H., Mareta, S., et al. (2019). Gasification reactivity and synergistic effect of conventional and microwave pyrolysis derived algae chars in CO2 atmosphere. Journal of the Energy Institute 92 (3), 730–740. doi:10.1016/j.joei.2018.02.009
Pianroj, Y., Jumrat, S., Werapun, W., Karrila, S., and Tongurai, C. (2016). Scaled-up reactor for microwave induced pyrolysis of oil palm shell. Chemical Engineering and Processing: Process Intensification 106, 42–49. doi:10.1016/j.cep.2016.05.003
Ravikumar, C., Senthil Kumar, P., Subhashni, S. K., Tejaswini, P. V., and Varshini, V. (2017). Microwave assisted fast pyrolysis of corn cob, corn stover, saw dust and rice straw: Experimental investigation on bio-oil yield and high heating values. Sustainable Materials and Technologies 11, 19–27. doi:10.1016/j.susmat.2016.12.003
Sui, H., Yang, H., Shao, J., Wang, X., Li, Y., and Chen, H. (2014). Fractional Condensation of Multicomponent Vapors from Pyrolysis of Cotton Stalk. Energy Fuels 28 (8), 5095–5102. doi:10.1021/ef5006012
Sun, T., Li, Z., Zhang, Z., Wang, Z., Yang, S., Yang, Y., et al. (2020). Fast corn stalk pyrolysis and the influence of catalysts on product distribution. Bioresource Technology 301, 122739. doi:10.1016/j.biortech.2020.122739
Tang, Q., Zheng, Y., Wang, T., and Wang, J. (2014). Vacuum pyrolysis of plant oil asphalt for transport fuel production catalyzed by alkali metal compounds. Fuel Processing Technology 126, 192–198. doi:10.1016/j.fuproc.2014.05.008
Vispute, T. P., Zhang, H., Sanna, A., Xiao, R., and Huber, G. W. (2010). Renewable Chemical Commodity Feedstocks from Integrated Catalytic Processing of Pyrolysis Oils. Science 330 (6008), 1222–1227. doi:10.1126/science.1194218
Yi, Z., Hu, D., Xu, H., Wu, Z., Zhang, M., and Yan, K. (2020). Metal regulating the highly selective synthesis of gamma-valerolactone and valeric biofuels from biomass-derived levulinic acid. Fuel 259, 116208. doi:10.1016/j.fuel.2019.116208
Yu, Z., Jiang, L., Wang, Y., Li, Y., Ke, L., Yang, Q., et al. (2020). Catalytic pyrolysis of woody oil over SiC foam-MCM41 catalyst for aromatic-rich bio-oil production in a dual microwave system. Journal of Cleaner Production 255, 120179. doi:10.1016/j.jclepro.2020.120179
Keywords: corn straw, microwave pyrolysis, temperature, power, phenol-rich bio-oil
Citation: Zhao Z, Jiang Z, Xu H and Yan K (2021) Selective Production of Phenol-Rich Bio-Oil From Corn Straw Waste by Direct Microwave Pyrolysis Without Extra Catalyst. Front. Chem. 9:700887. doi: 10.3389/fchem.2021.700887
Received: 27 April 2021; Accepted: 14 June 2021;
Published: 01 July 2021.
Edited by:
Svetlana Ivanova, University of Seville, SpainCopyright © 2021 Zhao, Jiang, Xu and Yan. This is an open-access article distributed under the terms of the Creative Commons Attribution License (CC BY). The use, distribution or reproduction in other forums is permitted, provided the original author(s) and the copyright owner(s) are credited and that the original publication in this journal is cited, in accordance with accepted academic practice. No use, distribution or reproduction is permitted which does not comply with these terms.
*Correspondence: Kai Yan, yank9@mail.sysu.edu.cn