Abstract
Flexible micro-catheter for minimally invasive medical diagnosis and therapy is highly desirable, but still a challenge. Here, an active interventional micro-catheter based on square tubular conducting polymer actuator is developed. This actuator is composed of two conducting polymer composite electrodes and a square tubular gel polymer electrolyte layer between the electrodes layer. To fabricate the square tubular gel polymer electrolyte layer, a simple, solution-based, gradual phase inversion technique was used. A high ionic conductivity and low tensile modulus Poly(vinylidenefluoride-co-hexafluoropropylene) (PVDF-HFP) square tube that could act as the actuator body and electrolyte layer to allow the actuator operate without the need of external ions was fabricated. Also, since the electrodes are supposed to be largely deformed under low voltage, which has great significance for the safe application of the catheter for the human body, conducting polymers with good electrical and mechanical properties are great choice for the catheter. Therefore, we developed a PEDOT:PSS/carboxylic SWCNT (SWCNT-COOH)/ionic liquid (IL) composite electrode film. With the addition of SWCNT-COOH and IL, the conductivity reached more than ten times higher than that of pristine PEDOT:PSS and the specific capacitance was three times higher than that of PEDOT:PSS film. Additionally, the stretchability and flexibility of the electrode film were highly enhanced because of the doping of IL. Due to the high electrical conductivity of composite electrode and low tensile modulus of actuator body, the obtained square tubular actuator can bend in two dimensions under a low voltage (∼1 V) in open air. A simulated vessel model was constructed and the square tubular actuator succeeded in real-time active bending and guiding, which will have broad application prospects in the interventional medicine field.
Export citation and abstract BibTeX RIS
1. Introduction
In recent years, minimally invasive diagnosis and therapy have become increasingly popular. To inject a contrast medium or medicine into the blood vessel, or to measure blood pressure locally, a catheter, which is a hollow flexible micro tube, is used. As doctors have to control the tip of the catheter from outside the body, operations with catheters require a certain level of skill, particularly when the blood vessel has a loop or complex configuration [1]. Therefore, developing smart catheters with active bending and guiding functions is essential fpr improving the success rate and reducing operation times.
Conducting polymers (CPs), such as polypyrrole, polythiophene and polyaniline, have been regarded as promising candidates for the preparation of lightweight, flexible and biocompatible EAP actuators. Actuators based on CPs, which dimensional changes resulting from electrochemical doping, transportation of dopant ions between the polymer matrix and the surrounding electrolyte solution, have the following advantages: combination of low driving voltage (typically 1–3 V), large deformation and fast response speed compared with traditional ionic polymer metal composites (IPMC). The reversible volume change of the conducting polymers actuator can be attributed to the electro-oxidation-reduction reaction of the conductive polymers at low voltage. When a voltage is applied to both surfaces of the CPs actuator, an electric field is formed inside the polymer driver. Under the action of the electric field, anions and cations migrate towards the anode and cathode, and the conductive polymers undergoes a redox reaction. The oxidized side absorbs the anion to expand, while the reduced side repels the anion and shrinks it [2, 3].
Catheters are a general term for luminal products that connect people inside and outside the body. It is widely used as a pathway in drug administration, blood collection, detection, and introduction of other medical devices. However, ordinary catheters only have the infusion function and cannot achieve intelligent bending deformation to perform complicated surgical operations. Lu et al [4] integrated a micro actuator made of memory alloy at the tip of the guide wire to enable precise control of the catheter in the vessel. Due to the inherent nature of the material, vascular damage is still caused during catheter intervention, causing complications during treatment [5, 6]. The biocompatibility of some forms of conducting polymers including polypyrrole, poly(3,4-ethylenedioxythiophene) (PEDOT) makes them potentially suitable for use in medical devices [7]. Conducting polymers have been applied on existing commercial catheters by chemical and electrochemical deposition. Such catheters have been shown to operate in an electrolyte bath, as demonstrated by Shoa et al [8, 9]. Hanayama et al used a silicone rubber tube as the catheter body and coated it with SEPLEGYDA® (Shin-Etsu Polymer) and polypyrrole [10]. The entire device was coated with an electrolyte gel outside of the polypyrrole so that it can operate in air. In the first conducting polymer driven catheter built, developed by Mazzoldi and De Rossi, conducting polymers fibers surround a solid polymer electrolyte creating a bending tube with a 0.8 mm outer diameter [11–13]. Large radius of curvature due to high Young's Modulus of the solid polymer electrolyte and the use of a stiff copper wire as a counter electrode are some of the disadvantages of this approach. Farajollahi et al fabricated a hollow interpenetrating polymer network (IPN) tube as the catheter body and solid polymer electrolyte layer [14]. The active layer was PEDOT deposited on the surface of the IPN tube via oxidative polymerization. The low Young's modulus of IPN allows the actuator easy to bend and achieve a small radius of curvature. This actuator showed 6.5 mm deflection in open air under 2 V.
In this work, we fabricated a square tubular conducting polymer actuator. In order to operate the square tubular actuator in open air, a polymer square tube acting as the actuator body and electrolyte layer is necessary. Poly(vinylidenefluoride-co-hexafluoropropylene) (PVDF-HFP) is often used as the supporting polymer of the gel polymer electrolyte [15–17]. However, the PVDF-HFP based gel polymer electrolyte layers reported before were all thin films. PVDF-HFP microporous membrane was fabricated by phase inversion method using water as the non-solvent [18]. And PVDF-HFP hollow fiber was fabricated by wet-spinning method with water as coagulating bath [19]. Here, we proposed a simple, solution-based, gradual phase inversion technique to obtain a PVDF-HFP square tube. This PVDF-HFP square tube acting as the actuator body and gel polymer layer before soaked with ionic liquid of 1-ethyl-3-methyl imidazolium tetra-fluoroborate (EMIBF4). Because the PVDF-HFP square tube has a high ionic conductive of 7.29 mS · cm−1, the actuator can operate in open air without the need of external ions. Besides, the PVDF-HFP square tube fabricated by gradual phase inversion technique has lower crystallinity and tensile modulus.
To drive the actuator under low voltage, the electrodes should have high electrical and mechanical properties. In our previous work, we reported a high performance conducting polymer actuator based on poly(3,4-ethylenedioxythiophene):poly(styrenesulfonic acid) (PEDOT:PSS) electrodes doped with carboxylic multi-walled carbon nanotube (MWCNTs) [20]. However, single-walled carbon nanotubes (SWCNTs) have more excellent electrical properties than MWCNTs due to fewer structure defects in the SWCNT [21]. Fukushima et al reported that SWCNTs ground with ionic liquids (ILs) of imidazolium ions can form bucky-gel [22]. And they fabricated a fully plastic actuator based on bucky-gel composite electrodes [16]. The electrodes of the actuator were prepared by casting the mixture of bucky gel and PVDF-HFP solution. Here, we developed the PEDOT:PSS electrode doped with bucky-gel, which composed of carboxylic SWCNTs (SWCNTs-COOH) and ionic liquid of 1-ethyl-3-methyl imidazolium tetra-fluoroborate (EMIBF4). With the addition of carboxylic SWCNTs and ionic liquid (IL), the conductivity reached more than 10 times higher than pristine PEDOT:PSS, and the specific capacitance was three times higher than PEDOT:PSS film.
Furthermore, we fabricated square tubular actuator composed of two conducting polymer composite electrodes and a square tubular gel polymer electrolyte layer between the electrodes layer. Figure 1 presents the schematic diagrams and photographs of the tubular actuator. Benefit from the good electrical and mechanical properties of composite electrodes and the low tensile modulus of actuator body, the obtained square tubular actuator can bend in two dimensions under a low voltage (∼1 V) in open air, which is necessary for safety when it works in the blood vessels. Additionally, a simulated vessel model is constructed and the square tubular actuator succeeded in real-time active bending and guiding.
Figure 1. Schematic diagrams and photographs of the square tubular actuator. (a) Appearance of actuator schematic diagram. (b) Side view of actuator schematic diagram. (c) Cross-section of actuator schematic diagram, (d) appearance of actuator photograph. (e) Side view of actuator photograph. (f) Cross-section of actuator photograph.
Download figure:
Standard image High-resolution image2. Experimental section
2.1. Materials
PEDOT:PSS (Clevios, PH1000, 1.3 wt%) was commercially available in the form of water dispersion from Heraeus. The carboxylic SWCNTs (SWCNTs-COOH) were bought from Nanjing XF NANO Materials Tech Co., Ltd Poly(vinylidene fluoride-co-hexafluoropropylene) (PVDF-HFP) purchased from Sigma-Aldrich. Ionic liquid of 1-ethyl-3-methyl imidazolium tetra-fluoroborate (EMIBF4, 99%) was obtained from Shanghai Cheng Jie Chemical Co., Ltd N,N-Dimethylformamide (DMF) was obtained from Sinopharm Chemical Reagent Co., Ltd and deionized water was puried through Ultrapure Milli-Q system.
2.2. Preparation of PEDOT:PSS/SWCNT-COOH/IL electrode layer
The SWCNTs-COOH and EMIBF4 (1/3, w/w) were ground with an agate mort. Then the mixed gel was added to the water dispersion of PEDOT:PSS and stired vigorously to obtain a homogeneous solution. The PEDOT:PSS/SWCNT-COOH/IL electrode solution was typically composed of 60 wt% PEDOT:PSS, 10 wt% SWCNTs-COOH and 30 wt% IL. Then 4 ml homogeneous solution mentioned above was casted on a PTFE substrate (2.5 cm × 6 cm size) and dried at 40 °C for 1 day to obtain free-standing PEDOT:PSS/SWCNT-COOH/IL electrode film. Printine PEDOT:PSS electrode film was prepared by the same casting method.
2.3. Preparation of electrolyte layer
As illustrated in figure 2, we can fabricate PVDF-HFP square tube by the gradual phase inversion method. To prepare the PVDF-HFP square tube, a customized PTFE mould was used. A metal wire was placed in the middle of the mould to create the hollow structure for the square tube. The 10 wt% PVDF-HFP solution was prepared by dissolving 1.05 g PVDF-HFP pellets in 10 ml DMF and poured into the PTFE mould in air condition at room temperature, the PVDF-HFP solution gradually transformed into solid state because of phase inversion with water vapor in air as the non-solvent. Then the solid state PVDF-HFP was dried in a vacuum oven at 30 °C, after that the metal wire was pulled out and the PVDF-HFP square tube was obtained. The porous PVDF-HFP square tube was soaked in EMIBF4 at 50 °C to form tubular electrolyte layer. The conventional PVDF-HFP based gel polymer electrolyte film was prepared by the casting method reported previously [23].
Figure 2. Schematic diagrams for the fabrication procedure of the PVDF-HFP square tube.
Download figure:
Standard image High-resolution image2.4. Assembly of the actuator
The actuator was assembled by hot pressing method. Two pieces of the as-prepared electrode films were laminated on tubular PVDF-HFP/EMIBF4 electrolyte layer and heat pressed at 120 °C for 1 h under 16 KPa and naturally cooled to room temperature, obtaining a square tubular actuator about 0.7 mm thick, 3 mm width and 25 mm long. When the tubular PVDF-HFP/EMIBF4 electrolyte layer has been heated to 120 °C, it became soft and viscid, so that the PVDF-HFP/EMIBF4 electrolyte layer and the electrode films can adhere together [24, 25]. Additionally, as it is presented in figures 1(d)–(f), the hollow structure of the PVDF-HFP square tube remained after hot pressing procedure.
2.5. Characterization
FE-SEM was recorded by Hitachi S-4800. The samples were dried in the vacuum oven overnight before capturing the surface and cross-sectional images. The electrical conductivity of electrode was tested by the multifunction digital four-probe tester (ST-2258C). The mechanical properties were evaluated by the tensile test with a mechanical tester (AGS-X, Shimadzu), where tensile modulus, tensile strength, and elongation at break were calculated from the stress–strain curves. Raman spectra was conducted with LabRAM HR800 from JY Horiba. X-ray powder diffraction analysis was measured by Philips X'Pert PRO diffractometer with nickel-filtered Cu Kα radiation.
Figure 3 shows the displacement measurement setup of the tubular actuator. The tubular actuator was performed in a two-electrode configuration with 20 mm free length from electrode contacts. Actuation performance was tested by Multi-potential step to the actuator using CHI660D electrochemical work station. Actuation displacements were recorded by laser locator (Keyence, LK-G80).
Figure 3. The displacement measurement setup of the tubular actuator.
Download figure:
Standard image High-resolution imageElectrochemical properties of electrode films were tested by electrochemical work station (Shanghai Chenghua, CHI660D) using a three-electrode system with a 1 M H2SO4 electrolyte. In a three-electrode cell, the as-prepared PEDOT:PSS/SWCNT-COOH/IL and PEDOT:PSS film was characterized as a working electrode with Pt wire as counter electrode and Ag/AgCl electrode as the reference electrode. cyclic voltammograms (CV) curves were measured in the potential range of 0–0.8 V versus Ag/AgCl at the scan rate of 10 mV · s−1. Electrochemical impedance spectroscopy (EIS) was performed from 10 mHz to 100 kHz with a voltage amplitude of 10 mV.
Specific capacitance (C, F · g−1) of the electrode films were calculated by using the following equation [20]:
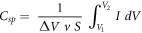
,where ΔV is the potential window, v is the scan rate and S is the weight taken of the PEDOT:PSS/SWCNT-COOH/IL or PEDOT:PSS electrodes.
Ionic conductivity (σ, mS · cm−1) of the electrolyte films are calculated from the impedance spectroscopy by using the following equation [26]:

,where D is the thickness of electrolyte membrane, S is the contact area of the electrolyte with stainless steel electrode, represents the series resistance obtained from the EIS curve.
Ionic liquid uptake of polymer electrolyte was determined by weighting the membranes before and after absorbing EMIBF4 and calculated through the following equation [26]:

,where wo and ws represent the mass of the membrane before and after the absorbing EMIBF4.
3. Results and discussion
3.1. Properties of PEDOT:PSS/SWCNT-COOH/IL electrode
In order to investigate the influence of the addition of carboxylic SWCNTs and IL on the micro-structure of the PEDOT:PSS, SEM images have been presented in figure 4. Figures 4(a) and (c) reveal that the surface morphology of the pristine PEDOT:PSS and PEDOT:PSS/SWCNT-COOH/IL electrode films. In figure 4(a), it can be seen that the surface morphology of pristine PEDOT:PSS electrode film is dense and smooth. With the addition of carboxylic SWCNTs and IL, the surface morphology of the electrode film becomes rough, as shown in figure 4(c). The internal morphology of two kinds of electrode films are showed in figures 4(b) and (d). The internal morphology of the PEDOT:PSS/SWCNT-COOH/IL becomes porous because of the doping of carboxylic SWCNTs and IL, and the carboxylic SWCNTs are homogenous distributed in the PEDOT:PSS matrix.
Figure 4. SEM images of PEDOT:PSS film, (a) surface, (b) cross-section. SEM images of PEDOT:PSS/SWCNT-COOH/IL film, (c) surface, (d) cross-section.
Download figure:
Standard image High-resolution imageIn order to expound the effect of the carboxylic SWCNTs and IL on the mechanical properties of the electrode films, tensile test was performed and presented in figure 5(a). Figure 5(a) displays stress–strain curves of the pristine PEDOT:PSS and PEDOT:PSS/SWCNT-COOH/IL electrode films. Pristine PEDOT:PSS electrode film fractured at the maximum stress of 14.64 MPa, whereas PEDOT:PSS/SWCNT-COOH/IL electrode film fractured at the maximum stress of 12.38 MPa. It is noted that the elongation at break of the PEDOT:PSS/SWCNT-COOH/IL electrode film attained 38.15%, which is almost four times higher than the pristine PEDOT:PSS electrode film (10.39%). The calculated tensile modulus is listed in table 1. The tensile modulus of the pristine PEDOT:PSS electrode film is 213.43 MPa, with the addition of carboxylic SWCNTs and IL the tensile modulus slightly decreases to 132.33 MPa. According to the results, we can conclude that the mechanical strength of the electrode film decreases slightly, while the flexibility clearly improves.
Figure 5. (a) Stress–strain curves of the pristine PEDOT:PSS and PEDOT:PSS/SWCNT-COOH/IL electrode films, (b) I–V curves of the pristine PEDOT:PSS and PEDOT:PSS/SWCNT-COOH/IL electrode films. (c) Comparison of XRD patterns of the pristine PEDOT:PSS and PEDOT:PSS/SWCNT-COOH/IL electrode films. (d) Raman spectra of pristine PEDOT:PSS and PEDOT:PSS/SWCNT-COOH/IL films.
Download figure:
Standard image High-resolution imageTable 1. Mechanical properties and electrical properties of electrode films.
Electrode material | Tensile Modulus (MPa) | Tensile Strength (MPa) | Elongation (%) | Thickness (μm) | Conductivity (S · cm−1) |
---|---|---|---|---|---|
PEDOT:PSS | 213.43 | 14.64 | 10.39 | 72 | 0.29 |
PEDOT:PSS/SWCNT-COOH/IL | 132.33 | 12.38 | 38.15 | 93 | 3.14 |
The electrical conductivity of pristine PEDOT:PSS and PEDOT:PSS/SWCNT-COOH/IL electrode films are also listed in table 1. Also, the I–V curves of the pristine PEDOT:PSS and PEDOT:PSS/SWCNT-COOH/IL electrode films are showed in figure 5(b). The electrical conductivity of the PEDOT:PSS/SWCNT-COOH/IL film is 10 times higher than pristine PEDOT:PSS film. The carboxylic SWCNTs weaken the ionic interaction between PEDOT and PSS by forming conjugate effect and hydrogen bond with PEDOT and PSS respectively. The interactions between them will bring about tiny separation between PEDOT unit and PSS chain [20, 27]. Also, when IL molecules are incorporated into the PEDOT:PSS system, due to their small sizes, they can more easily interact with both the positively-charged PEDOT and the negatively-charged PSS chains. This leads to a charge screening effect that weakens the Coulombic interaction between the PEDOT and PSS chains. Therefore, larger PEDOT-rich domains can form due to the dissociation between PEDOT and PSS, which aids in enhancing the conductivity of the films [28]. Compared to PEDOT:PSS, the XRD patterns of PEDOT:PSS/SWCNT-COOH/IL in figure 5(c) show sharp diffraction peaks at 2θ = 26.57°, indicating better crystalline and more ordered structure for PEDOT:PSS/SWCNT-COOH/IL film [29]. Raman spectra were conducted to prove the separation between PEDOT unit and PSS chain. Figure 5(d) shows Raman spectra of pristine PEDOT:PSS film and PEDOT:PSS/SWCNT-COOH/IL film under 532 nm semiconductor laser excitation. In figure 5(d), the band between 1400 and 1500 cm−1 corresponds to the stretching vibration of Cα = Cβ on the five-member ring of PEDOT [30, 31], and the band is observed to move towards lower wave numbers and becomes narrow. This means that the resonant structure of PEDOT chain changes from a benzoid to a quinoid structure [32, 33]. The benzoid structure may be the favorite structure for a coil conformation, while the quinoid structure may be the favorite structure for a linear or expanded-coil structure. Thus, we deduce that the coil conformation turns into linear or expanded-coil conformation, resulting in a marked increase in the work function of PEDOT:PSS.
The electrochemical performance of pristine PEDOT:PSS film and PEDOT:PSS/SWCNT-COOH/IL film was investigated using a standard three-electrode system in 1 M H2SO4 aqueous solution. Figure 6(a) shows CV curves for the two kinds of electrode films at scan rate of 10 mV s−1. The specific capacitance value of PEDOT:PSS/SWCNT-COOH/IL film calculated from the integrated area of CV curves is 41.96 F · g−1, which is three times higher than PEDOT:PSS film (13.71 F · g−1). Figure 6(b) shows Nyquist plots of the electrode films in 1 M H2SO4 in a frequency range from 10 kHz to 10 mHz. The equivalent series resistance of PEDOT:PSS/SWCNT-COOH/IL film is much lower than PEDOT:PSS film (inset of figure 6(b)), showing greater conductivity in aqueous solution.
Figure 6. Electrochemical performance characteristics conducted in a three-electrode system in 1 M H2SO4 electrolyte. (a) Cyclic voltammograms of the pristine PEDOT:PSS and PEDOT:PSS/SWCNT-COOH/IL electrode films. (b) Nyquist plots of the pristine PEDOT:PSS and PEDOT:PSS/SWCNT-COOH/IL electrode films.
Download figure:
Standard image High-resolution image3.2. Properties of gradual phase inversion PVDF-HFP
The comparative morphological studies of casting PVDF-HFP film and gradual phase inversion PVDF-HFP film have been carried out by SEM and images are shown in figure 7. Figure 7(a) shows surface of casting PVDF-HFP film is dense and smooth. As presented in figure 7(c), the surface morphology of gradual phase inversion PVDF-HFP film becomes porous. Also, to compare the cross-section SEM images shown in figures 7(b) and (d), the gradual phase inversion PVDF-HFP film presents a porous structure.
Figure 7. SEM images of casting PVDF-HFP film (a) surface, (b) cross-section. SEM images of gradual phase inversion PVDF-HFP film (c) surface, (d) cross-section.
Download figure:
Standard image High-resolution imageFigure 8(a) shows Nyquist plots of the electrolyte films with blocking electrodes in a frequency range from 10 kHz to 10 mHz. As illustrated in figure 8(b), the ionic conductivity of gradual phase inversion PVDF-HFP/EMIBF4 electrolyte film is 7.29 mS · cm−1, which is almost twice of the ionic conductivity of casting PVDF-HFP/EMIBF4 electrolyte film. The increasement of ionic conductivity is related to the high ionic liquid uptake of the gradual phase inversion PVDF-HFP film due to its porous structure.
Figure 8. (a) Nyquist plots of casting PVDF-HFP film and gradual phase inversion PVDF-HFP film. (b) Ionic liquid uptake and ionic conductivity of casting PVDF-HFP/EMIBF4 and gradual phase inversion PVDF-HFP/EMIBF4 electrolyte. (c) Comparison of XRD patterns of casting PVDF-HFP film and gradual phase inversion PVDF-HFP film. (d) Stress–strain curves of casting PVDF-HFP film and gradual phase inversion PVDF-HFP film.
Download figure:
Standard image High-resolution imageNot only the morphology of the PVDF-HFP film obtained by the gradual phase inversion method has become porous, but the crystallinity has decreased through the gradual phase inversion. Wide-angle XRD was used to provide information about the crystallinity degree of the PVDF-HFP films. A comparison of XRD patterns of different method processed PVDF-HFP films is displayed in figure 8(c). From the diffraction patterns, peaks are observed at 2θ = 18.35°, 20.00°, 26.51° for casting PVDF-HFP film, which is in line with previous reported result [34]. However, it is shown that the crystal peaks at 2θ = 18.35°, 26.51° of gradual phase inversion PVDF-HFP film disappeared. Also, the broad diffraction peak centered at 2θ = 20.00° of casting PVDF-HFP film slightly shifted to 2θ = 20.35° of the gradual phase inversion PVDF-HFP film. Besides, the full width half maximum (FWHM) values are increased from 0.673° (casting PVDF-HFP film) to 0.909° (gradual phase inversion PVDF-HFP film). The crystallinity degree of polymers is in positive correlation with the value of FWHM [35]. These results indicate that the gradual phase inversion PVDF-HFP film had a lower crystallinity than the casting PVDF-HFP film.
To study the mechanical properties of two different kinds of PVDF-HFP films, tensile tests with a mechanical tester have been conducted and the stress–strain curves are presented in figure 8(d). As presented in figure 8(d), the tensile modulus of the gradual phase inversion PVDF-HFP film (20.96 MPa) is much lower than the casting PVDF-HFP film (106.87 MPa). Thus the actuator body fabricated by the gradual phase inversion method makes the whole device easy to bend.
3.3. Performance of actuators
In order to study the improved performance of the PEDOT:PSS/SWCNT-COOH/IL electrode, the actuator was assembled by laminating two pieces of the PEDOT:PSS/SWCNT-COOH/IL electrode films with casting PVDF-HFP/EMIBF4 electrolyte film through the hot pressing method. And the PEDOT:PSS electrode based actuator fabricated by the same way for contrast. Although due to the presence of ionic liquids, biocompatibility is not very good, which could be solved by packaging with soft materials. Figure 9(a) introduced the response of the two kinds of actuators under the input voltage of 1 V at a frequency of 0.05 Hz. The peak to peak displacement of the PEDOT:PSS/SWCNT-COOH/IL electrode based actuator is up to 3.79 mm, which is more than twice of the PEDOT:PSS electrode based actuator. The high bending performance of the actuator is as a result of the good electrical and mechanical properties of the PEDOT:PSS/SWCNT-COOH/IL electrode. However, the response speed is lower because the device is much thicker (about 0.7 mm) compared to most actuator devices (about 0.11 mm) [20]. And a possible solution is to increase the ionic conductivity of the electrolyte layer and accelerate the internal ion migration.
Figure 9. (a) Comparison performance of actuators based on PEDOT:PSS/SWCNT-COON/IL electrode and PEDOT:PSS electrode under 1 V at 0.05 Hz. (b) Comparison performance of actuators based on gradual phase inversion PVDF-HFP and casting PVDF-HFP under 1 V at 0.05 Hz. (c) Displacement of the square tubular actuator under 1 V at 0.05 Hz. (d) Displacement of the square tubular actuator under 1 V from 0.025–0.5 Hz.
Download figure:
Standard image High-resolution imageIt is inconvenient and time-consuming to fabricate a square tubular actuator with PVDF-HFP/EMIBF4 electrolyte film prepared by traditional casting method. Therefore, two different types of actuators were assembled by laminating two pieces of the PEDOT:PSS/SWCNT-COOH/IL electrode films with gradual phase inversion PVDF-HFP/EMIBF4 electrolyte film and casting PVDF-HFP/EMIBF4 electrolyte film, respectively, through the same hot pressing method mentioned above. Figure 9(b) shows the response of the actuators with different electrolyte film under the input voltage of 1 V at a frequency of 0.05 Hz. The peak to peak displacement of the actuator with gradual phase inversion PVDF-HFP/EMIBF4 electrolyte film reaches 4.21 mm, which is a little higher than the actuator with casting PVDF-HFP/EMIBF4 electrolyte film (3.79 mm). Compared with a self-contained tubular conducting polymer actuator [14], whose maximum deflection reaches 3.72 mm under the driven voltage of 2 V, the displacement of the actuator with gradual phase inversion PVDF-HFP/EMIBF4 electrolyte is much larger. The improved performance of the actuator is due to the lower tensile modulus of the gradual phase inversion PVDF-HFP film, which makes the actuator easier to bend.
The square tubular actuator was also assembled by laminating two pieces of the PEDOT:PSS/SWCNT-COOH/IL electrode films with a gradual phase inversion PVDF-HFP square tube absorbed EMIBF4 through hot pressing. Figure 9(c) displays the displacement of the square tubular actuator under 1 V at 0.05 Hz. The peak to peak displacement of the square tubular actuator is 1.156 mm. The actuation performance under 0.025–0.5 Hz is shown in figure 9(d). The displacement of the square tubular actuator varies with the change of frequency. The lower the frequency is the bigger peak to peak displacement the tubular actuator can reach.
To demonstrate the active bending and guiding functions of the square tube actuator as the smart catheter, a customized platform with furcate channels was used. As presented in figure 10, the width of the central channel is 6 mm and the angle between central channel and branch channel is 30°, meeting the bending angle of most blood vessels, which is much larger than that of IPMC active catheter (20° maximum deflection angle under 3 V) fabricated by Fang et al [36] Besides, we lowered the thickness of the actuator to 0.7 mm to obtain larger deformation. Figure 10 shows the bending of the actuator at DC 1 V with the duration is less than 1 min. The actuator can deflect from central channel to branch channel in both directions, which makes the actuator a good candidate to serve as the smart catheter in minimally invasive diagnosis and therapy.
Figure 10. Actuator before and after bending resulting from the application of ±1 V to the actuator with 0.7 mm thick and 25 mm long.
Download figure:
Standard image High-resolution image4. Conclusions
In this paper, we reported an easy to fabricate square tubular conducting polymer actuator, which can be used as a smart catheter. This actuator based on the PEDOT:PSS/SWCNT-COOH/IL composite electrode. The doping of carboxylic SWCNTs generates conjugate effect and hydrogen bonding with PEDOT:PSS, which not only obviously changes polymer structure but also enhances the electrical and mechanical properties of the electrodes. Besides, with the addition of IL, the stretchability and flexibility of PEDOT:PSS film was highly improved. It is found that the conductivity of PEDOT:PSS/SWCNT-COOH/IL composite electrode (3.14 S · cm−1) performed ten times higher than pristine PEDOT:PSS film (0.29 S · cm−1) and the strain (38.15%) is four times that of pristine PEDOT:PSS film (10.39%). Moreover, a PVDF-HFP square tube with high ionic conductivity and low Young's modulus was fabricated through a uncomplicated and efficient gradual phase inversion method. This PVDF-HFP square tube, which also has lower crystallinity and tensile modulus than traditional casting PVDF-HFP, can act as the actuator body and electrolyte layer. Due to the high electrical conductivity of the composite electrode and low Young's modulus of actuator body, the obtained square tubular actuator can bend in two dimensions under the low voltage (∼1 V). A simulated vessel model is constructed and the square tube actuator succeeded in real-time active bending and guiding, which will have broad application prospects in the interventional medicine field. In short, we prepared electrode films with low modulus and good electrical conductivity by doping IL and SWCNT-COOH. In addition, we used the gradual phase inversion PVDF-HFP film to assemble a high-conductivity square tube actuator for the applications of catheter.
Acknowledgments
We thank the National Key R&D Program of China (Project No. 2018YFC2000900), Start-up Fund of Hong Kong Polytechnic University (BE1H), the Science and Technology of Jiangsu Province (Project No. BE2016086), and Hong Cheng Seagull Project of Jiangxi Province (Grant No. 2018DI03), and National Natural Science Foundation of China No. 21975214).