Abstract
Fiber-reinforced polymer composites are being used in an increasingly wide range of products. They are particularly popular in automotive and aerospace sectors because they offer an attractive combination of stiffness, strength and low mass. Adhesively-bonded joints of such materials are preferred by many designers due to their assembling advantages over other traditional mechanical joining systems, such as bolted and riveted joints. In this study, some experimental works have been carried out on adhesively-bonded adherends manufactured from a woven carbon fiber-reinforced polymer matrix composite (Hexply 8552S/A280-5H, produced by Hexcel), by using a film adhesive (AF163-2K produced by 3 M). The bonded specimens were prepared in the Single Lap Joint (SLJ) configuration, and tested in tensile and also in four-point bending loading. In order to assess the joint performance, three different overlap lengths, 15 mm, 25 mm and 40 mm, and two different thicknesses of the composite adherends, 2 mm and 3 mm, were used. The results shown that the parameters are controlled by the loading modes; while the overlap length increases the joint performance significantly in tensile loading, the opposite was the case for those in bending loading, which was affected mainly by the adherend thicknesses. The results were related to the mechanisms of joint failures; while the joints in the tensile failed in the adhesive layer with some exceptions, those in the bending mainly failed in the plies adjacent to the layer. The current study indicates that one of the important factors affecting the joint strength of the adherends manufactured from the laminated composites is the local failure of the plies. It is thought more focused-studies would be needed to lessen such problems, which would be possible via in-depth numerical analysis.
Export citation and abstract BibTeX RIS
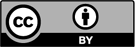
Content from this work may be used under the terms of the Creative Commons Attribution 3.0 licence. Any further distribution of this work must maintain attribution to the author(s) and the title of the work, journal citation and DOI.