Abstract
Application of ultrasonic waves has been considerably progressed during the last decade and piezoelectric ceramics have had a common use as the driving source of such waves. However, there is not enough documented information on design and technology of manufacturing a high power ultrasonic transducer. In this paper, an attempt has been made to analyze the stress produced along the oscillating PZT employed ultrasonic head by applying the principles of acoustic wave propagation. Then, based on such analysis, general principles of PZT transducer design, excited by a DC-biased alternating electrical source, has been derived and finally a typical such transducer has been designed, manufactured and tested. By employing finite element modal analysis, the resonance frequency of the transducer was determined and compared with the experimental results. It was concluded that, the constitutive piezoelectric equations referred to in most sources and books are not valid for analyzing the acoustical dynamic stress in ultrasonic transducers. Instead, the analysis should be done with considering the dynamic behavior (elastic, damping and Inertia factors) of the problem.











Similar content being viewed by others
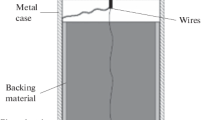
Notes
For example, ref. [15] suggests the values of Q m = 7.5 and Q m = 27,500 for Quartz when oscillating in water and air, respectively.
References
W.P. Mason, Electromechanical Transducers and Wave Filters (Van Nostrand, Princeton, NJ, 1948)
W.P., Mason, Piezoelectric Crystals and their Applications to Ultrasonic (Van Nostrand-Reinhold, Princeton, NJ, 1950)
H. Allik, T.J.R. Hugues, Int. J. Numer. Methods Eng. 2, 151–157 (1970)
D. Boucher, M. Lagier, C. Maerfeld, IEEE Trans. Sonics Ultrasonic. 28, 318–330 (1981)
E. Mori, et al, Ultrasonic International 1977 Conference Proceeding, p. 262, 1977
E. Mori, Y. Tsuda, Proceeding of Ultrasonic International, pp. 307–312, 1981
L. Shuya, Appl. Acoust. 44, 249–257 (1955)
S. Hirase et al., Ultrasonics, 34, 213–217 (1996)
D.J. Powell, G. Hayward, R.Y. Ting, IEEE Trans. Ultrason Ferroelect. Freq. Contr. 45(3), 667–679 (1998)
J. Randeraat, Piezoelectric Ceramics (Mullard, London, 1974), p. 5
M. Shahini, A. Abdullah, M. Rezaei, Design and Manufacture of an Ultrasonic Transducer with 1 kW Power and 22 kHz Frequency Using Piezoceramics. Master of science thesis, Faculty of Mechanical Engineering, AmirKabir University of Technology, 2004
F.S. Tse, I.E. Morse, R.T. Hinkle, Mechanical Vibrations, Theory and Applications, 2nd edn. (Allyn and Bacon, Boston, MA, 1978)
Data Book, Piezoelectric Crystals (Finnsonic, Finland, 1997)
M. Prokic, Piezoelectric Transducers Modeling and Characterization (MPInterconsulting, Switzerland, 2004)
W. Seto, Theory and Problems of Acoustics ((McGraw-Hill, New York, 1971), p. 188
R. Frederick, Ultrasonic Engineering (Wiley, New York, 1965), p. 284
M. Toda, Ultrasonic Transducer Having Impedance Matching Layer. US Patent no. 0027400, 2002
H. Leung, M. Wai, L. Wa Chan, C. Kee Liu, Ultrasonic Transducer. US Patent no. 0062395 A1, 2003
A. Abdullah, Electro-Physical Processes, Postgraduate Lecture Notes. Faculty of Engineering, Tarbiat Modarres University, 1991
Morgan Electro Ceramics Web Site, Piezoelectric Ceramics Properties and Applications, Chapter 6
M. Prokic, BLT Common Recommendation Regarding Dimensions (MPInterconsulting, Switzerland, 2004)
H.A. Rijna, Proceedings of NATO Advanced Study Institute, 225–249 (1980)
J.E. Shigley, Mechanical Engineering Design ((McGraw-Hill, New York, 1986), pp. 305–306
E. Oberg, F.D. Jones, Machinery’s Handbook (Industrial, New York), pp. 1415–1416
M. Prokic, Nodal Plane Position and Output Amplitude (MPInterconsulting, Switzerland, 2004)
A. Shahidi, F. Keymaram, F. Farahmand, Design and Manufacture of Ultrasonic Cutter for Surgery. Master of science thesis, Department of Mechanical Engineering, Sharif University of Technology, 2004
Acknowledgements
This work was funded by Highly-Distinguished Solid Mechanics Center at AmirKabir University of Technology. Thanks should also be given to Advanced Manufacturing Research Center (AMRC) for their contribution to manufacture the parts, and to Electromagnets Laboratory of Electrical Department of AmirKabir University of Technology where the required equipments were provided to test the transducer. Authors express their sincere appreciation to Dr. Prokic and his colleagues at MPInterconsulting for providing invaluable empirical data and helpful comments.
Author information
Authors and Affiliations
Corresponding author
Rights and permissions
About this article
Cite this article
Abdullah, A., Shahini, M. & Pak, A. An approach to design a high power piezoelectric ultrasonic transducer. J Electroceram 22, 369–382 (2009). https://doi.org/10.1007/s10832-007-9408-8
Received:
Accepted:
Published:
Issue Date:
DOI: https://doi.org/10.1007/s10832-007-9408-8