Abstract
Welding thick plate has become a topic of interest for multiple industrial sectors for many years. However, there are plenty of difficulties on the joining technology of medium-thickness titanium alloy plate waiting to be solved urgently. In this paper, the microstructure and residual stress distribution of 7.5-mm-thick TC4 titanium alloy jointed by laser-multi-pass-narrow-gap welding are investigated by simulated and experimental methods. It is demonstrated that the columnar crystals in the lower molten pool are significantly finer than that in the upper molten pool, of which the growth direction is consistent with the direction of the maximum temperature gradient of simulation results. Results also indicate that multiple heat effect is the main cause of the acicular martensite coarsening. In addition, stress field simulation results reveal that high transverse tensile stress appears near the interlayer. There is a stress concentration phenomenon occurring at the weld toe and weld root, and the stress concentration coefficient of the weld root reaches 2.13.














Similar content being viewed by others
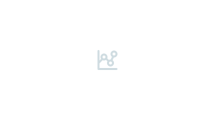
References
Akman E, Demir A, Canel T, Sınmazc T (2009) Laser welding of Ti6Al4V titanium alloys. J Mater Process Technol 209:3705–3713
Schneider A, Gumenyuk A, Lammers M, Malletschek A, Rethmeier M (2014) Laser bead welding of thick titanium sheets in the field of marine technology. Phys Procedia 56:582–590
Peng W, Yelkenci D, Chen JH, Chang BH, Du D, Shan JG (2019) Numerical analysis of the effect of welding positions on formation quality during laser welding of TC4 titanium alloy parts in aerospace industry. J Laser Appl 31:022401
Zhang XQ, Yang JG, Liu XS, Chen XH, Fang HY, Shen QU (2019) Numerical simulation of weld tab length influence on welding residual stress and distortion of aero-engine disk. Front Mater Sci China 3(3):306–309
Wang JF, Sun QJ, Feng JC, Wang SL, Zhao HY (2017) Characteristics of welding and arc pressure in TIG narrow gap welding using novel magnetic arc oscillation. Int J Adv Manuf Technol 90:413–420
Chen J, Wei YH, Zhan XH, Pan P (2017) microstructure and mechanical property of laser-welded butt joints of 5A06 Al alloy with static magnetic field support. Int J Adv Manuf Technol 92:1677–1686
Fu PF, Mao ZY, Zuo CJ, Wang YJ, Wang CM (2014) Microstructures and fatigue properties of electron bead welds with bead oscillation for heavy section TC4-DT alloy. Chin J Aeronaut 27(4):1015–1021
Olshanskaya TV, Salomatova ES, Belenkiy VY, Trushnikov DN, Permyakov GL (2017) Electron bead welding of aluminum alloy AlMg6 with a dynamically positioned electron bead. Int J Adv Manuf Technol 89:3439–3450
Keßler B, Brenner B, Dittrich D, Standfuß J, Beyer E, Leyens C (2019) Laser-multi-pass-narrow-gap-welding of nickel superalloy-Alloy 617OCC. J Laser Appl 31:022412
Guo W, Crowther D, Francis JA, Thompson A, Li L (2015) Process-parameter interactions in ultra-narrow gap laser welding of high strength steels. Int J Adv Manuf Technol 84:2547–2566
Yang WX, Xin JJ, Fang C, Dai WH, Wei J, Wu JF, Song YT (2019) Microstructure and mechanical properties of ultra-narrow gap laser weld joint of 100mm-thick SUS304 steel plates. J Mater Process Tech 265:130–137
Keßler B, Brenner B, Dittrich D, Standfuß J, Beyer E, Leyens C, Maier G (2019) Laser multi-pass narrow-gap welding—a promising technology for joining thick-walled components of future power plants. MATEC Web of Conferences 269:02011
Zhan XH, Wu YF, Kang Y, Liu X, Chen XD (2019) Simulated and experimental studies of laser-MIG hybrid welding for plate-pipe dissimilar steel. Int J Adv Manuf Technol 101:1611–1622
Auwal ST, Ramesh S, Yusof F, Manladan SM (2018) A review on laser bead welding of titanium alloys. Int J Adv Manuf Technol 97:1071–1098
Bunaziv I, Frostevarg J, Akselsen OM, Kaplan AFH (2018) The penetration efficiency of thick plate laser-arc hybrid welding. Int J Adv Manuf Technol 97:2907–2919
Kashaev N, Ventzke V, Fomichev V, Fomin F, Riekehr S (2016) Effect of Nd:YAG laser bead welding on weld morphology and mechanical properties of Ti-6Al-4V butt joints and T-joints. Opt Lasers Eng 86:172–180
Xue X, Pereira AB, Amorim J, Liao J (2017) Effects of pulsed Nd: YAG laser welding parameters on penetration and microstructure characterization of a DP1000 steel butt joint. Metals. 7:292
Liu C, Zhang JX, Xue CB (2011) Numerical investigation on residual stress distribution and evolution during multipass narrow gap welding of thick-walled stainless steel pipes. Fusion Eng Des 86:288–295
Zhan Y, Zhang ED, Ge YM, Liu CS (2018) Residual stress in laser welding of TC4 titanium alloy based on ultrasonic laser technology. Appl Sci 8(10):1997
Kobryn P. A, Moore E. H, Semiatin S. L (2000) The effect of laser power and traverse speed on microstructure porosity and built height in laser-deposited Ti-6Al-4V, Scr Mater 43: 299-305.
Wu X, Liang J, Mei J, Mitchell C, Goodwin PS, Voice W (2004) Microstructures of laser-deposited Ti-6Al-4V. Mater Design 25:137–144
Deng D, Murakawa H (2006) Numerical simulation of temperature field and residual stress in multi-pass welds in stainless steel pipe and comparison with experimental measurements. Comput Mater Sci 37:269–277
Zain-ul-Abdein M, Nelias D, Jullien JF, Deloison D (2009) Prediction of laser bead welding-induced distortions and residual stresses by numerical simulation for aeronautic application. J Mater Process Technol 209:2907–2917
Yang XY, Chen H, Zhang CZ, Zhu ZT, Cai C, Huang S (2019) Microstructure and stress distribution of narrow-gap rotating laser welding thick Al-Mg alloy joint. J Laser Appl 31:022002
Behúlová M, Babalová E, Nagy M (2017) Simulation model of Al-Ti dissimilar laser welding-brazing and its experimental verification. Mater Sci Eng 179:012007
Kou S (2003) Welding Metallurgy. Wiley, New York
Yang X, Li S, Qi H (2014) Ti-6Al-4V welded joints via electron bead welding: microstructure, fatigue properties, and fracture behavior. Mater Sci Eng A 597:225–231
Duquennoy M, Ouaflouh M, Qian M.L, Jenot F, Ourak M (2001) Ultrasonic characterization of residual stresses in steel rods using a laser line source and piezoelectric transducers. NDT&E Int 34: 355-362.
Teng TL, Chang PH, Tseng WC (2003) Effect of welding sequences on residual stresses. Comput Struct 81:273–286
Author information
Authors and Affiliations
Corresponding author
Additional information
Publisher’s note
Springer Nature remains neutral with regard to jurisdictional claims in published maps and institutional affiliations.
Rights and permissions
About this article
Cite this article
Liu, J., Zhan, X., Gao, Z. et al. Microstructure and stress distribution of TC4 titanium alloy joint using laser-multi-pass-narrow-gap welding. Int J Adv Manuf Technol 108, 3725–3735 (2020). https://doi.org/10.1007/s00170-020-05623-0
Received:
Accepted:
Published:
Issue Date:
DOI: https://doi.org/10.1007/s00170-020-05623-0