Abstract
Gas turbine components experience large temperature gradients due to thermal cycling that often result in cracking. When brazing wide gaps greater than 500 μm in width, capillary action is inadequate to fill the joint and activated diffusion healing (ADH) is applied for repairs. ADH utilizes a mixture of a low melting temperature filler metal and an additive powder with a composition similar to that of the base metal. This research studies the effect of processing parameters on the microstructure and mechanical properties of repaired joints on DS René 108 superalloy. AWS BNi-2 and BNi-5 grade filler metals were mixed with MAR-M 247 alloy powder at weight percent ratios of 40:60, 50:50, and 60:40. For BNi-2 containing brazes, the mechanical properties improved with increasing additive powder. In contrast, the BNi-5 containing brazes showed an opposite trend. Brazing temperatures were held at 1200°C and 1232°C. The mechanical properties for both braze alloys improved at the higher brazing temperature. Diffusion hold temperatures were held at 1100°C and 1121°C for 2 h and 4 h. For the BNi-2 alloys, the higher temperature and longer brazing time improved mechanical properties. For the BNi-5 alloys, the lower brazing temperature and shorter brazing time improved mechanical properties.






















Similar content being viewed by others
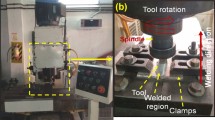
References
Schwartz M (2003) Brazing 2nd Edition, Materials Park: ASM International
Mattheij JHG (1985) Role of brazing in repair of superalloy components advantages and limitations. Mater Sci Technol 1:608–612
Miglietti W, Toit MD (2010) High strength, ductile braze repairs for stationary gas turbine components—part I. J Eng Gas Turbines Power 132(8):82102
Huang X, Miglietti W (2012) Wide gap braze repair of gas turbine blades and vanes—A Review. J Eng Gas Turbines Power 134(1):10801
Heikinheimo LS, Laukkanen A, Veivo J (2005) Joint characterisation for repair brazing of superalloys. Welding in the World 49:5–12
Gale WF, Butts DA (2004) Transient liquid phase bonding. Sci Technol Weld Join 9(4):283–300
Wu X, Chandel RS, Li H, Seow H, Wu S (2000) Induction brazing of Inconel 718 to Inconel X-750 using Ni–Cr–Si–B amorphous foil. J Mater Process Technol 104(1–2):34–43
Wu X, Chandel RS, Li H (2001) Evaluation of transient liquid phase bonding between nickel-based superalloys. J Mater Sci 6:1539–1546
Pouranvari M, Ekrami A, Kokabi AH (2008) Microstructure development during transient liquid phase bonding of GTD-111 nickel-based superalloy. J Alloys Compd 461(1–2):641–647
Duvall DS, Owczarski WA, Paulonis DF (1974) TLP bonding--A new method. Weld J April:203–214
Ramirez JE and Liu S (1992) Diffusion brazing in the nickel-boron system. Weld J 365–376
Pouranvari M, Ekrami A, Kokabi AH (2013) TLP bonding of cast IN718 nickel based superalloy: process–microstructure–strength characteristics. Material Science Engineering A 568:76–82
Idowu OA, Ojo OA, Chaturvedi MC (2006) Microstructural study of transient liquid phase bonded cast INCONEL 738LC superalloy. Metall Mater Trans A 37A:2787–2796
Cook GO, Sorensen CD (2011) Overview of transient liquid phase and partial transient liquid phase bonding. J Mater Sci 46(16):5305–5323
Jacobson DM, Humpston G (2005) Principles of brazing. ASM International, Materials Park
Hoppin BYGS, Berry TF (1970) Activated diffusion bonding a new joining process produces high strength joints. Welding Research Supplement:505–509
Pallos KJ (2001) Gas turbine repair technology. GE Power Systems 4(1)
Su CY, Lih WC, Chou CP, Tsai HC (2001) Activated diffusion brazed repair for IN738 hot section components of gas turbines. J Mater Process Technol 115(3):326–332
Kim YH, Kim KT, Kim IH (2006) Effect of mixing ratio on mechanical properties of wide-gap brazed ni-based superalloy with NI-Si-B alloy powder. Key Eng Mater 306–308:935–940
Lim LC, Lee WY, Lai MO (1995) Nickel base wide gap brazing with preplacement technique part 1 - effect of material and process parameters on formation of macrovoids. Mater Sci Technol 11(10):1041–1045
Zhang XP, Shi YW (2004) A dissolution model of base metal in liquid brazing filler metal during high temperature brazing. Scr Mater 50(7):1003–1006
Arafin MA, Medraj M, Turner DP, Bocher P (Nov. 2007) Effect of alloying elements on the isothermal solidification during TLP bonding of SS 410 and SS 321 using a BNi-2 interlayer. Mater Chem Phys 106(1):109–119
Arafin MA, Medraj M, Turner DP, Bocher P (2007) Transient liquid phase bonding of Inconel 718 and Inconel 625 with BNi-2: modeling and experimental investigations. Mater Sci Eng A 447(1–2):125–133
Saha RK, Khan TI (2009) Microstructural developments in TLP bonds using thin interlayers based on Ni–B coatings. Mater Charact 60(9):1001–1007
Bouse GK, Schaeffer JC, Henry MF, Company GE (2008) Optimizing SC René N4 alloyfor DS AFT-stagebucketapplicationsinindustrialgasturbines. TMS:99–108
Praxair Surface TechnologiesPraxair S.T. Technology, Inc, 2016. [Online]. Available: http://www.praxairsurfacetechnologies.com/. [Accessed: 11-Dec-2016]
Brazing Products Vitta Corporation. [Online]. Available: http://vitta.com/bproducts.html
ASTM Standard E3-11 (2014) Standard guide for preparation of metallographic specimens. ASTM International, West Conshohocken, PA 2014
ASTM Standard E562-11 (2014) Standard test method for determining volume fraction by systematic manual point count. ASTM International, West Conshohocken, PA 2014
ASTM Standard D6272-10 (2014) Standard test method for flexural properties of unreinforced and reinforced plastics and electrical insulating materials by four-point bending 1. ASTM International, West Conshohocken, PA 2014
Standard Method for Evaluating the Strength of Brazed Joints (2008)American Welding Society,C3.2 M/C3.2
Pouranvari M, Ekrami A, Kokabi AH (2009) Effect of bonding temperature on microstructure development during TLP bonding of a nickel base superalloy. J Alloys Compd 469(1–2):270–275
H.Okamoto, K.Cenzual (2002) Hafnium-Nickel Binary Phase Diagram. ASM International-ASM Alloy Phase Diagram Database
Nelson SD (2014) Multiphase wide gap braze alloys for the repair of nickel - base superalloy turbine Components: development and characterization. M.S. Thesis, CSM, Golden, CO
Nelson SD, Liu S, Kottilingam S, Madeni JC (2014) Spreading and solidification behavior of nickel wide-gap brazes. Welding in the World 58(4):593–600
Acknowledgements
This work was performed under the NSF Ma2JIC Center program and the financial support from GE Power and Water is gratefully acknowledged. Special thanks go to Bryan Riggs at Ohio State University for the microhardness mapping.
Author information
Authors and Affiliations
Corresponding author
Additional information
Recommended for publication by Commission XVII - Brazing, Soldering and Diffusion Bonding
Rights and permissions
About this article
Cite this article
Hawk, C., Liu, S. & Kottilingam, S. Effect of processing parameters on the microstructure and mechanical properties of wide-gap braze repairs on nickel-superalloy René 108. Weld World 61, 391–404 (2017). https://doi.org/10.1007/s40194-016-0420-y
Received:
Accepted:
Published:
Issue Date:
DOI: https://doi.org/10.1007/s40194-016-0420-y